PVD (Physical Vapor Deposition) and electroplating are two distinct methods used for coating materials, each with unique processes, advantages, and limitations. PVD involves the physical vaporization of a material in a vacuum environment, which then condenses onto a substrate to form a thin film. This process is typically carried out at high temperatures and is known for its ability to deposit a wide range of materials, including metals, alloys, and ceramics. In contrast, electroplating is an electrochemical process where a metal coating is deposited onto a substrate by passing an electric current through an electrolyte solution containing the metal ions. Electroplating is generally performed at room temperature and is commonly used for decorative finishes, corrosion resistance, and improving surface properties. The choice between PVD and electroplating depends on factors such as the desired coating properties, substrate material, and application requirements.
Key Points Explained:
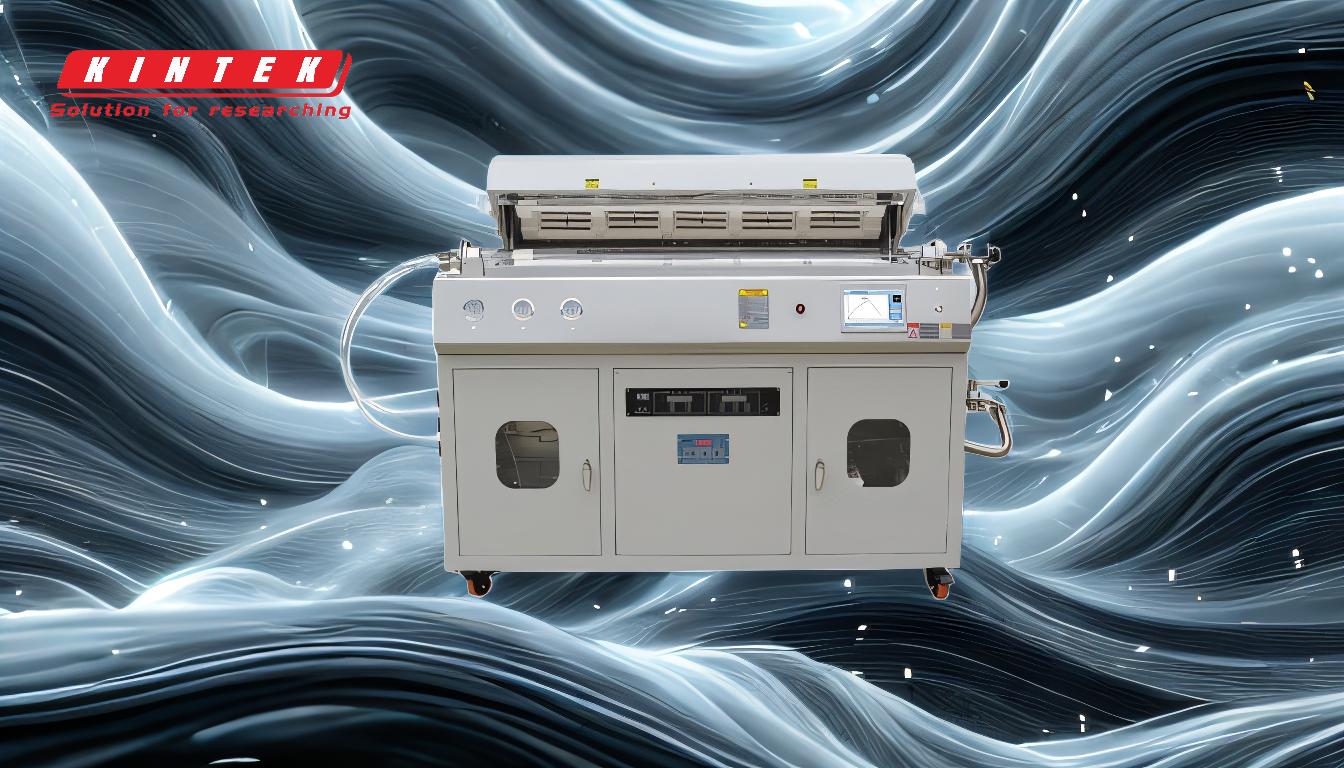
-
Process Mechanism:
- PVD: Involves the physical vaporization of a material in a vacuum, followed by its condensation onto a substrate. This process is typically carried out at high temperatures and does not involve chemical reactions.
- Electroplating: An electrochemical process where metal ions in a solution are reduced and deposited onto a substrate by passing an electric current. This process is usually performed at room temperature.
-
Temperature Requirements:
- PVD: Requires high temperatures for the vaporization and deposition of materials, which can limit its use with temperature-sensitive substrates.
- Electroplating: Generally performed at room temperature, making it suitable for a wider range of materials, including those that are sensitive to high temperatures.
-
Coating Materials:
- PVD: Can deposit a broader range of materials, including metals, alloys, and ceramics. This versatility makes PVD suitable for various industrial applications.
- Electroplating: Primarily used for depositing metals and metal alloys. It is commonly used for decorative finishes, corrosion resistance, and improving surface properties.
-
Coating Properties:
- PVD: Produces coatings that are less dense and less uniform compared to CVD (Chemical Vapor Deposition) but are faster to apply. PVD coatings are known for their high hardness and wear resistance.
- Electroplating: Produces dense and uniform coatings, but the process is generally slower compared to PVD. Electroplated coatings are often used for their aesthetic appeal and protective qualities.
-
Bond Strength:
- PVD: Creates a mechanical bond between the coating and the substrate, which is generally weaker than the diffusion-type bond formed in CVD.
- Electroplating: Forms a strong metallurgical bond between the coating and the substrate, providing excellent adhesion and durability.
-
Environmental and Safety Considerations:
- PVD: Operates in a vacuum environment, which minimizes the risk of contamination and reduces the production of harmful by-products. However, the high temperatures and vacuum conditions can be energy-intensive.
- Electroplating: Involves the use of chemical solutions, which can pose environmental and safety concerns due to the handling and disposal of hazardous chemicals.
-
Applications:
- PVD: Commonly used in industries requiring high-performance coatings, such as aerospace, automotive, and cutting tools. PVD is also used for decorative coatings on consumer products.
- Electroplating: Widely used in industries for decorative finishes, corrosion protection, and improving surface properties. It is also used in electronics for creating conductive layers on circuit boards.
In summary, PVD and electroplating are two distinct coating methods, each with its own set of advantages and limitations. The choice between the two depends on the specific requirements of the application, including the desired coating properties, substrate material, and environmental considerations.
Summary Table:
Aspect | PVD | Electroplating |
---|---|---|
Process Mechanism | Physical vaporization in a vacuum, no chemical reactions | Electrochemical process using electric current and metal ions |
Temperature | High temperatures required | Room temperature |
Coating Materials | Metals, alloys, ceramics | Primarily metals and alloys |
Coating Properties | Less dense, high hardness, wear-resistant | Dense, uniform, decorative, protective |
Bond Strength | Mechanical bond (weaker than CVD) | Strong metallurgical bond |
Environmental Impact | Vacuum environment, minimal contamination, energy-intensive | Chemical solutions, hazardous waste, environmental concerns |
Applications | Aerospace, automotive, cutting tools, decorative coatings | Decorative finishes, corrosion protection, electronics |
Need help deciding between PVD and electroplating for your project? Contact our experts today!