RF (Radio Frequency) and microwave plasma are both forms of plasma generated using electromagnetic waves, but they differ significantly in their frequency ranges, generation mechanisms, and applications. RF plasma operates at lower frequencies (typically 3 kHz to 300 MHz), while microwave plasma operates at much higher frequencies (300 MHz to 300 GHz). These differences in frequency lead to variations in plasma density, energy distribution, and the types of applications they are suited for. RF plasma is often used in processes requiring lower energy and precise control, such as semiconductor manufacturing, while microwave plasma is favored for high-energy applications like material synthesis and surface treatment.
Key Points Explained:
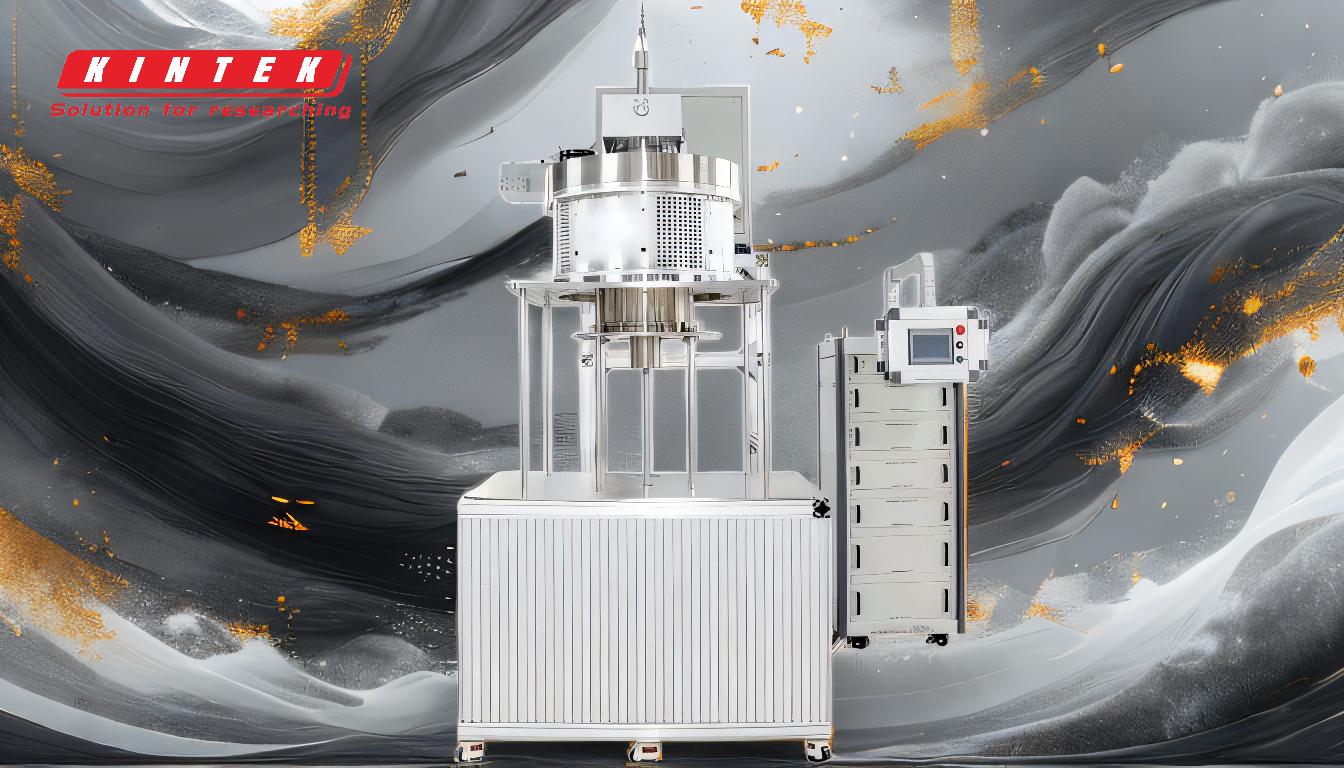
-
Frequency Range:
- RF Plasma: Operates in the frequency range of 3 kHz to 300 MHz. This lower frequency range allows for better control over the plasma, making it suitable for applications requiring precision.
- Microwave Plasma: Operates at much higher frequencies, typically between 300 MHz and 300 GHz. The higher frequency results in greater energy transfer to the plasma, making it more intense and suitable for high-energy processes.
-
Plasma Generation Mechanism:
- RF Plasma: Generated using electrodes or inductive coupling. The lower frequency allows for a more stable and controllable plasma, which is ideal for delicate processes like thin-film deposition.
- Microwave Plasma: Generated using microwave radiation, often through a waveguide or resonant cavity. The high-frequency electromagnetic waves create a more energetic plasma, which is beneficial for applications requiring rapid heating or material breakdown.
-
Energy Distribution:
- RF Plasma: The energy distribution in RF plasma is more uniform and controlled, making it suitable for processes where precision and consistency are critical.
- Microwave Plasma: The energy distribution is more intense and localized, which can lead to higher plasma densities and temperatures. This makes microwave plasma ideal for applications like material synthesis and surface modification.
-
Applications:
- RF Plasma: Commonly used in semiconductor manufacturing, plasma etching, and surface treatment where precise control over the plasma is necessary.
- Microwave Plasma: Preferred for high-energy applications such as diamond film deposition, plasma cleaning, and waste treatment. The intense energy of microwave plasma allows for rapid processing and high throughput.
-
Plasma Density and Temperature:
- RF Plasma: Typically has lower plasma density and temperature compared to microwave plasma. This makes it suitable for processes that require gentle treatment of materials.
- Microwave Plasma: Exhibits higher plasma density and temperature due to the higher frequency and energy input. This is advantageous for processes that require rapid and intense energy transfer.
-
Equipment and Cost:
- RF Plasma: The equipment for generating RF plasma is generally less complex and less expensive compared to microwave plasma systems. This makes RF plasma more accessible for smaller-scale applications.
- Microwave Plasma: Requires more sophisticated equipment, such as high-frequency generators and waveguides, which can be more expensive. However, the higher energy output justifies the cost for applications requiring intense plasma.
-
Control and Stability:
- RF Plasma: Offers better control and stability, making it ideal for applications where precise manipulation of the plasma is required.
- Microwave Plasma: While less stable than RF plasma, the higher energy output of microwave plasma makes it suitable for applications where rapid and intense energy transfer is needed.
By understanding these key differences, purchasers can make informed decisions about which type of plasma technology best suits their specific application needs.
Summary Table:
Aspect | RF Plasma | Microwave Plasma |
---|---|---|
Frequency Range | 3 kHz to 300 MHz | 300 MHz to 300 GHz |
Generation Mechanism | Electrodes or inductive coupling | Microwave radiation via waveguide or resonant cavity |
Energy Distribution | Uniform and controlled | Intense and localized |
Applications | Semiconductor manufacturing, plasma etching, surface treatment | Diamond film deposition, plasma cleaning, waste treatment |
Plasma Density/Temp | Lower density and temperature | Higher density and temperature |
Equipment & Cost | Less complex and less expensive | More sophisticated and expensive |
Control & Stability | Better control and stability | Higher energy output, less stability |
Need help choosing the right plasma technology for your application? Contact our experts today!