Sintering and fusing (or melting) are both processes used to bind materials, particularly metals, but they differ significantly in their mechanisms, temperature requirements, and outcomes. Sintering involves heating materials to a temperature below their melting point, often combined with pressure, to bond particles together through atomic diffusion. This process avoids liquefaction, resulting in a solid mass with controlled porosity and minimal imperfections. Fusing, on the other hand, involves heating the material to its melting point, causing a complete phase change from solid to liquid. This requires higher energy and can lead to imperfections such as shrinkage or warping. Sintering is preferred for materials with high melting points and applications requiring precise control over the final product's properties.
Key Points Explained:
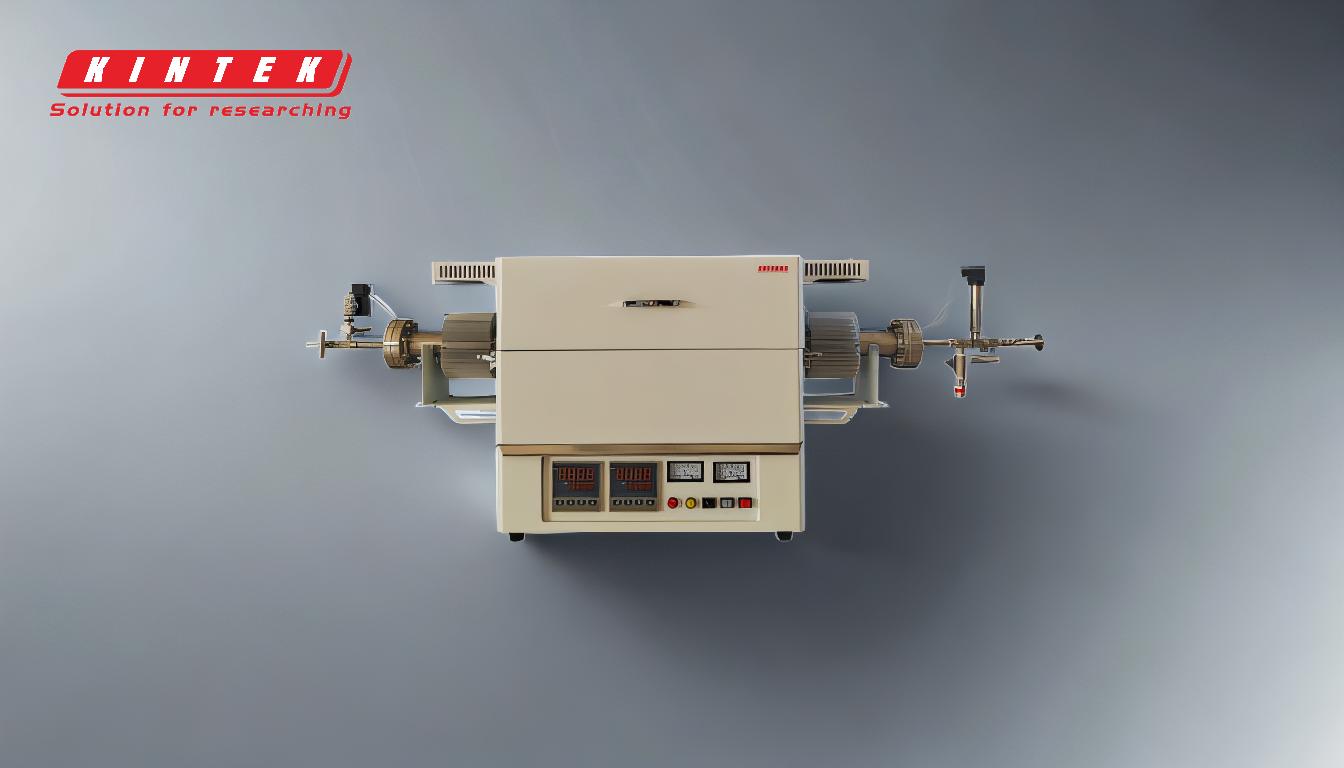
-
Temperature Requirements:
- Sintering: Occurs at temperatures below the material's melting point. This allows for bonding without liquefaction, making it suitable for materials with extremely high melting points, such as tungsten and molybdenum.
- Fusing: Requires heating the material to its melting point, inducing a complete phase change from solid to liquid. This process demands significantly higher energy.
-
Mechanism of Bonding:
- Sintering: Relies on atomic diffusion across particle boundaries under heat and pressure. The particles densify and merge without melting, resulting in a solid mass with controlled porosity.
- Fusing: Involves melting the material, which then solidifies into a unified mass upon cooling. This process can lead to imperfections like shrinkage or warping due to the complete phase change.
-
Energy and Control:
- Sintering: Requires less energy compared to fusing and offers greater control over the final product's properties, such as porosity and density. This makes it ideal for applications requiring precision.
- Fusing: Consumes more energy and is less controllable, often resulting in imperfections. It is typically used when a fully dense, liquid-phase bond is necessary.
-
Applications and Materials:
- Sintering: Commonly used for materials with high melting points and in applications where controlled porosity is beneficial, such as in filters, bearings, and certain types of ceramics.
- Fusing: Used in processes like casting, welding, and soldering, where a liquid phase is required to join materials or create complex shapes.
-
Process Steps:
-
Sintering:
- Preparation: Mixing primary materials and coupling agents, followed by compressing the powder into the desired shape.
- Heating: Heating to remove the coupling agent and fuse the primary material into a low-porosity whole.
- Particle Merging: Particles densify and merge, often accelerated using liquid phase sintering (LPS).
- Solidification: Cooling and solidifying into a unified mass.
-
Fusing:
- Melting: Heating the material to its melting point to induce a liquid phase.
- Solidification: Cooling the liquid to form a solid mass, often with imperfections due to the phase change.
-
Sintering:
-
Types of Sintering:
- Transient Liquid Phase Sintering: Involves adding a material (e.g., copper to iron) that melts at sintering temperatures, creating a temporary liquid phase that hardens upon cooling.
- Permanent Liquid Phase Sintering: Uses a permanent liquid material (e.g., carbide) that flows into openings and cracks, further bonding the materials together.
-
Advantages and Disadvantages:
-
Sintering:
- Advantages: Lower energy consumption, controlled porosity, minimal imperfections, suitable for high-melting-point materials.
- Disadvantages: Limited to materials that can bond without melting, may require additional processing steps.
-
Fusing:
- Advantages: Creates a fully dense bond, suitable for complex shapes and joining dissimilar materials.
- Disadvantages: Higher energy consumption, risk of imperfections, limited to materials that can withstand melting.
-
Sintering:
By understanding these key differences, one can choose the appropriate process based on the material properties and desired outcomes for specific applications.
Summary Table:
Aspect | Sintering | Fusing |
---|---|---|
Temperature | Below melting point | At melting point |
Mechanism | Atomic diffusion under heat and pressure | Complete phase change from solid to liquid |
Energy Consumption | Lower | Higher |
Control | High control over porosity and density | Less control, risk of imperfections |
Applications | Filters, bearings, ceramics | Casting, welding, soldering |
Advantages | Lower energy, minimal imperfections, suitable for high-melting-point materials | Fully dense bond, suitable for complex shapes |
Disadvantages | Limited to materials that bond without melting | Higher energy, risk of shrinkage or warping |
Need help choosing the right process for your application? Contact our experts today!