Sintering and fusion (or melting) are two distinct processes used to bind materials, particularly metals, but they differ significantly in their mechanisms, energy requirements, and outcomes. Sintering involves heating materials to a temperature just below their melting point, often combined with pressure, to bond particles without liquefaction. This process is energy-efficient and suitable for materials with high melting points, such as tungsten and molybdenum. In contrast, fusion involves heating the material to its melting point, causing a complete phase change from solid to liquid, which requires significantly more energy and can lead to imperfections. Sintering provides more control and consistent results, making it ideal for creating parts with enhanced properties like strength and hardness.
Key Points Explained:
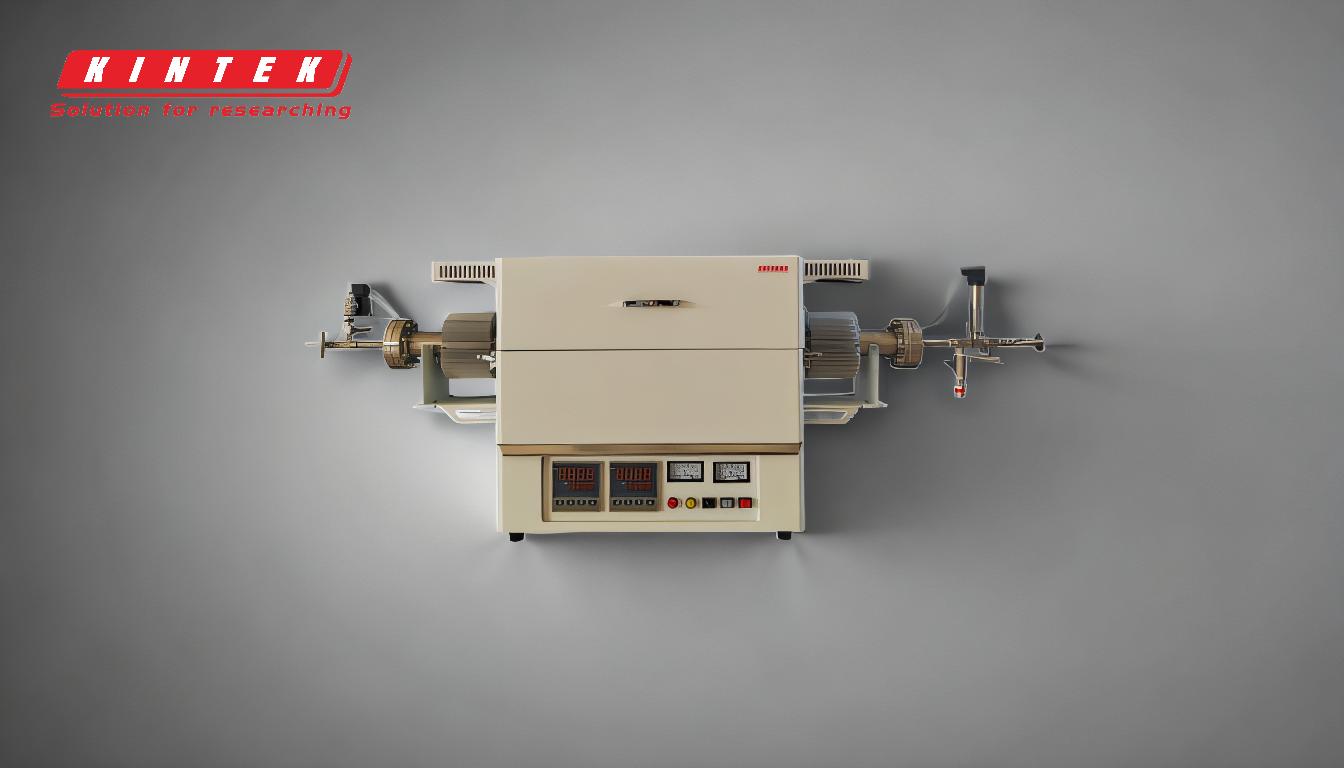
-
Temperature Requirements:
- Sintering: Occurs at temperatures below the melting point of the material. This allows particles to bond without reaching the energy threshold required for liquefaction. For example, sintering can be performed at relatively low temperatures if sufficient pressure is applied.
- Fusion (Melting): Requires the material to reach its melting point, where it transitions from a solid to a liquid state. This process demands significantly higher temperatures and energy.
-
Energy Efficiency:
- Sintering: More energy-efficient due to the lower temperatures involved. This makes it a preferred method for materials with high melting points.
- Fusion (Melting): Less energy-efficient because it requires temperatures high enough to induce a complete phase change, consuming more energy.
-
Mechanism of Bonding:
- Sintering: Uses a combination of heat and pressure to bond particles. The atoms diffuse across particle boundaries, fusing them together without liquefaction.
- Fusion (Melting): Relies solely on heat to turn the material into a liquid, which then solidifies to form bonds.
-
Material Properties:
- Sintering: Enhances properties like strength and hardness. It is often used for materials with extremely high melting points, such as tungsten and molybdenum.
- Fusion (Melting): Can result in imperfections due to the high temperatures and phase change involved. It is less controlled compared to sintering.
-
Applications:
- Sintering: Suitable for creating parts from metals with high melting points and for applications requiring consistent results and enhanced material properties.
- Fusion (Melting): Used when a complete phase change is necessary, often in casting and molding processes.
-
Control and Consistency:
- Sintering: Provides more control over the process, leading to consistent and predictable results.
- Fusion (Melting): Less control due to the high temperatures and potential for imperfections during the phase change.
-
Examples:
- Sintering: Rolling snow into a ball is a form of pressure-based sintering.
- Fusion (Melting): Melting ice into water is a simple example of fusion.
In summary, sintering and fusion are fundamentally different processes with distinct advantages and applications. Sintering is more energy-efficient, provides better control, and is suitable for high-melting-point materials, while fusion involves higher energy consumption and is used when a complete phase change is required.
Summary Table:
Aspect | Sintering | Fusion (Melting) |
---|---|---|
Temperature | Below melting point | At melting point |
Energy Efficiency | More efficient due to lower temperatures | Less efficient due to higher energy requirements |
Bonding Mechanism | Heat and pressure bond particles without liquefaction | Heat causes complete phase change from solid to liquid |
Material Properties | Enhances strength and hardness; ideal for high-melting-point materials | Can lead to imperfections; less controlled |
Applications | High-melting-point materials, consistent results | Casting, molding, and processes requiring complete phase change |
Control & Consistency | High control, predictable results | Less control, potential for imperfections |
Examples | Rolling snow into a ball | Melting ice into water |
Discover the best process for your material bonding needs—contact our experts today!