Sintering and smelting are two distinct processes used in material science and metallurgy, each with unique mechanisms and applications. Sintering involves compacting and bonding powdered materials into a solid mass using heat and pressure without reaching the material's melting point. This process relies on atomic diffusion to bond particles, resulting in improved mechanical properties. Smelting, on the other hand, involves heating a material to its melting point to induce a phase change from solid to liquid, which is then refined to extract metals or create alloys. While sintering is energy-efficient and provides controlled bonding, smelting requires higher temperatures and energy, often leading to imperfections. Understanding these differences is crucial for selecting the appropriate process based on material properties and desired outcomes.
Key Points Explained:
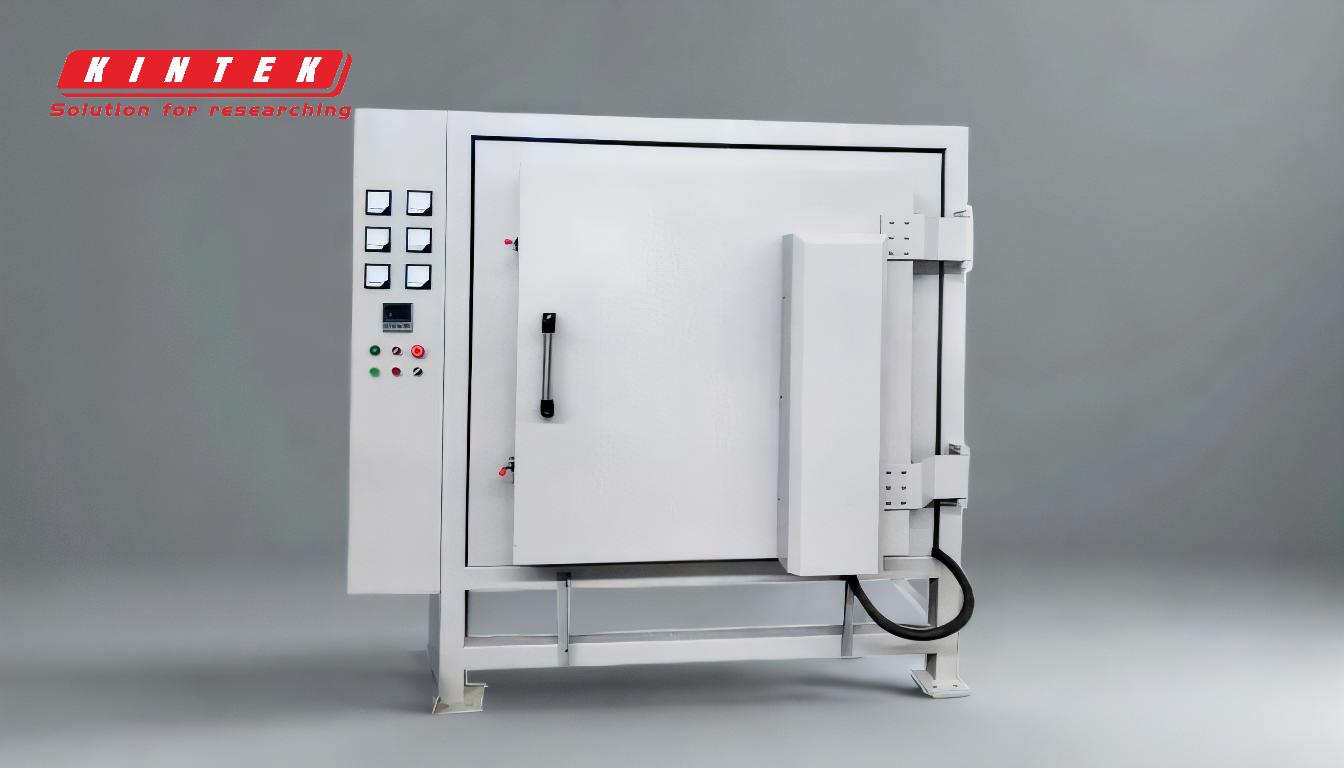
-
Definition and Mechanism:
- Sintering: A process that compacts powdered materials into a solid mass using heat and pressure without reaching the material's melting point. It relies on atomic diffusion to bond particles, enhancing mechanical properties like strength and hardness.
- Smelting: A process that involves heating a material to its melting point to induce a phase change from solid to liquid. This liquid is then refined to extract metals or create alloys.
-
Temperature Requirements:
- Sintering: Occurs at temperatures below the material's melting point, making it more energy-efficient. The lower temperature allows for better control over the bonding process and reduces the risk of material degradation.
- Smelting: Requires temperatures high enough to melt the material, which can be energy-intensive. The high temperatures are necessary to achieve the phase change and refine the metal.
-
Energy Consumption:
- Sintering: Consumes less energy compared to smelting due to the lower temperatures involved. This makes sintering a more cost-effective and environmentally friendly option for certain applications.
- Smelting: Requires significant energy input to reach and maintain the high temperatures needed for melting and refining. This can lead to higher operational costs and environmental impact.
-
Material Properties and Outcomes:
- Sintering: Produces materials with improved mechanical properties, such as increased strength, hardness, and density. The process allows for precise control over the final product's characteristics, making it suitable for creating complex shapes and high-performance components.
- Smelting: Often results in materials with potential imperfections due to the high temperatures and phase changes involved. However, smelting is essential for extracting pure metals and creating alloys with specific properties.
-
Applications:
- Sintering: Commonly used in powder metallurgy, ceramics, and additive manufacturing. It is ideal for producing parts with intricate geometries, high precision, and enhanced mechanical properties.
- Smelting: Primarily used in metallurgy for extracting metals from ores and creating alloys. It is essential for producing raw materials used in various industries, including construction, automotive, and electronics.
-
Control and Consistency:
- Sintering: Offers more control over the bonding process, leading to consistent and predictable results. The ability to bond materials without melting allows for the creation of uniform and defect-free components.
- Smelting: Can be less predictable due to the high temperatures and phase changes involved. The process may introduce impurities and inconsistencies, requiring additional refining steps to achieve the desired quality.
Understanding the differences between sintering and smelting is crucial for selecting the appropriate process based on the material properties, desired outcomes, and application requirements. Each process has its advantages and limitations, making them suitable for different industrial and manufacturing contexts.
Summary Table:
Aspect | Sintering | Smelting |
---|---|---|
Definition | Bonds powdered materials without melting, using heat and pressure. | Melts materials to extract metals or create alloys. |
Temperature | Below melting point, energy-efficient. | Above melting point, energy-intensive. |
Energy Consumption | Lower energy use, cost-effective. | High energy use, higher operational costs. |
Material Properties | Improves strength, hardness, and density. | May introduce imperfections but essential for pure metals and alloys. |
Applications | Powder metallurgy, ceramics, additive manufacturing. | Metallurgy, metal extraction, alloy production. |
Control & Consistency | Offers precise control, consistent results. | Less predictable, may require additional refining. |
Need help choosing between sintering and smelting? Contact our experts today for tailored solutions!