Spark Plasma Sintering (SPS) and conventional sintering differ significantly in their methods of heat generation, processing times, and the resulting material properties. SPS utilizes internal Joule heating, enabling rapid heating and cooling rates, achieving near-theoretical density at lower temperatures and in much shorter times compared to conventional sintering. This makes SPS particularly advantageous for sintering advanced materials, including nanocrystalline and gradient functional materials, without compromising their original characteristics. Conventional sintering, on the other hand, relies on external heating elements, leading to slower processing times and potentially higher temperatures, which can affect material properties.
Key Points Explained:
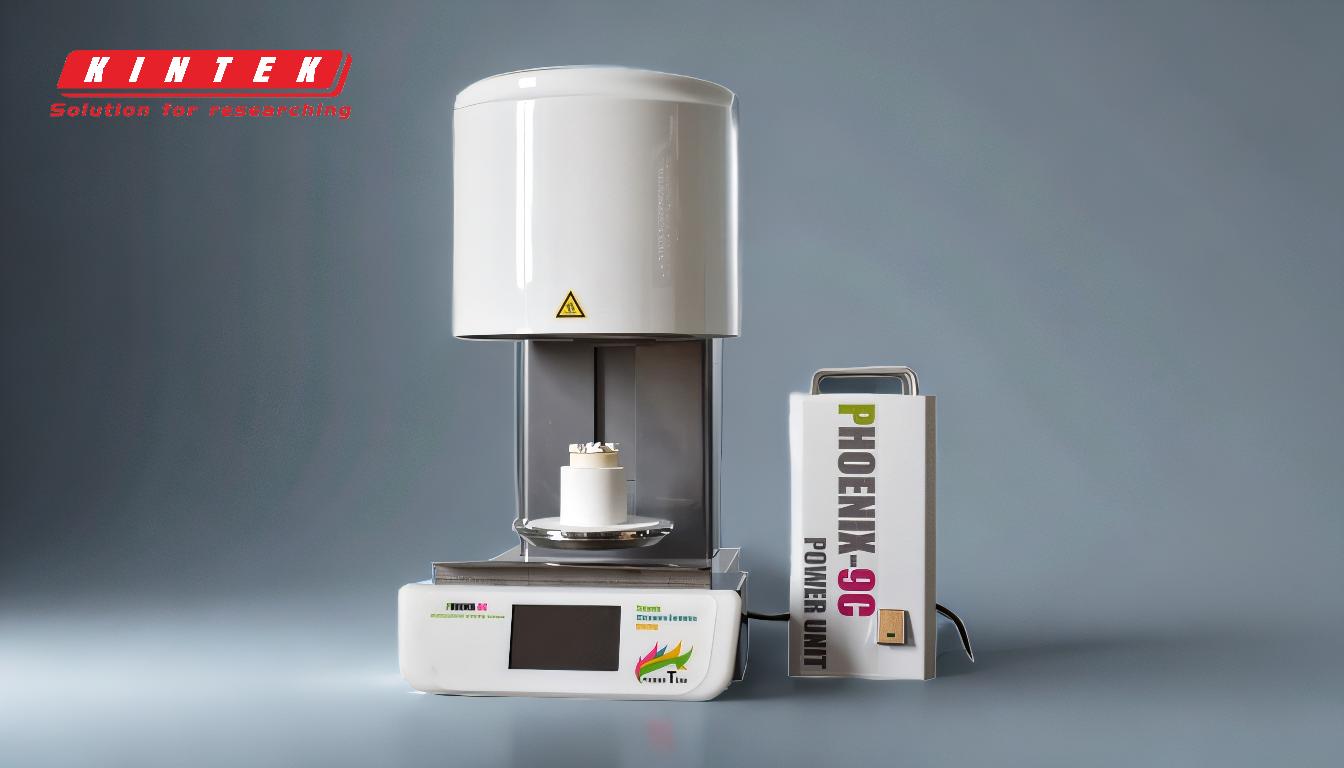
-
Heat Generation Method:
- Spark Plasma Sintering (SPS): Heat is generated internally through Joule heating, where an electric current passes directly through the graphite mold and the powder briquette. This internal heating mechanism allows for precise temperature control and rapid heating rates.
- Conventional Sintering: Heat is provided by external heating elements, such as furnaces. This method relies on thermal conduction from the outside, leading to slower and less uniform heating.
-
Processing Time:
- SPS: The sintering process is extremely fast, often completed within minutes, due to the high heating and cooling rates (up to 1000 K/min). This rapid processing can densify ceramics and other materials 10 to 100 times faster than conventional methods.
- Conventional Sintering: The process typically takes several hours, as it depends on slower heat transfer from external sources. This longer duration can lead to grain growth and other undesirable changes in material properties.
-
Temperature Requirements:
- SPS: Achieves near-theoretical density at lower sintering temperatures. The internal Joule heating allows for efficient energy transfer directly to the material, reducing the need for high external temperatures.
- Conventional Sintering: Often requires higher temperatures to achieve similar densities, which can lead to thermal degradation of the material.
-
Material Properties:
- SPS: The rapid sintering process preserves the original characteristics of the material, making it ideal for sintering amorphous, nanocrystalline, and gradient functional materials. This is particularly important for advanced materials where maintaining nanostructure or specific material gradients is crucial.
- Conventional Sintering: The slower process and higher temperatures can lead to grain growth and other changes in material microstructure, potentially degrading the material's properties.
-
Applications:
- SPS: Particularly effective for sintering advanced materials, including those with complex compositions or requiring precise control over microstructure. It is also suitable for sintering bonds between different metals or between metals and non-metals.
- Conventional Sintering: More commonly used for traditional materials where rapid sintering is not a critical requirement, and where the material can withstand higher temperatures without degradation.
In summary, Spark Plasma Sintering offers significant advantages over conventional sintering in terms of speed, temperature efficiency, and the ability to maintain material integrity. These benefits make SPS a preferred method for sintering advanced and complex materials, where traditional sintering methods may fall short.
Summary Table:
Aspect | Spark Plasma Sintering (SPS) | Conventional Sintering |
---|---|---|
Heat Generation | Internal Joule heating via electric current through the graphite mold and powder briquette. | External heating elements like furnaces, relying on thermal conduction from outside. |
Processing Time | Extremely fast (minutes), with high heating/cooling rates (up to 1000 K/min). | Slower (several hours), due to slower heat transfer from external sources. |
Temperature | Achieves near-theoretical density at lower temperatures. | Requires higher temperatures, potentially leading to thermal degradation. |
Material Properties | Preserves original characteristics, ideal for nanocrystalline and gradient functional materials. | May cause grain growth and microstructure changes, potentially degrading properties. |
Applications | Advanced materials, complex compositions, and precise microstructure control. | Traditional materials where rapid sintering is not critical and higher temperatures are tolerated. |
Learn more about how Spark Plasma Sintering can revolutionize your material processing—contact our experts today!