Traditional sintering and selective laser sintering (SLS) are both processes used to create solid objects from powdered materials, but they differ significantly in their methods, applications, and suitability for various production needs. Traditional sintering, often used in powder metallurgy, involves compacting powdered material into a mold and then heating it to just below its melting point to fuse the particles. This method is highly accurate, cost-effective for mass production, and requires molds. In contrast, selective laser sintering is an additive manufacturing (3D printing) technique that uses a laser to selectively fuse powdered material layer by layer, guided by a CAD file. SLS does not require molds, offers greater design flexibility, and is better suited for prototyping and low-volume production, though it is generally less accurate and more expensive than traditional sintering.
Key Points Explained:
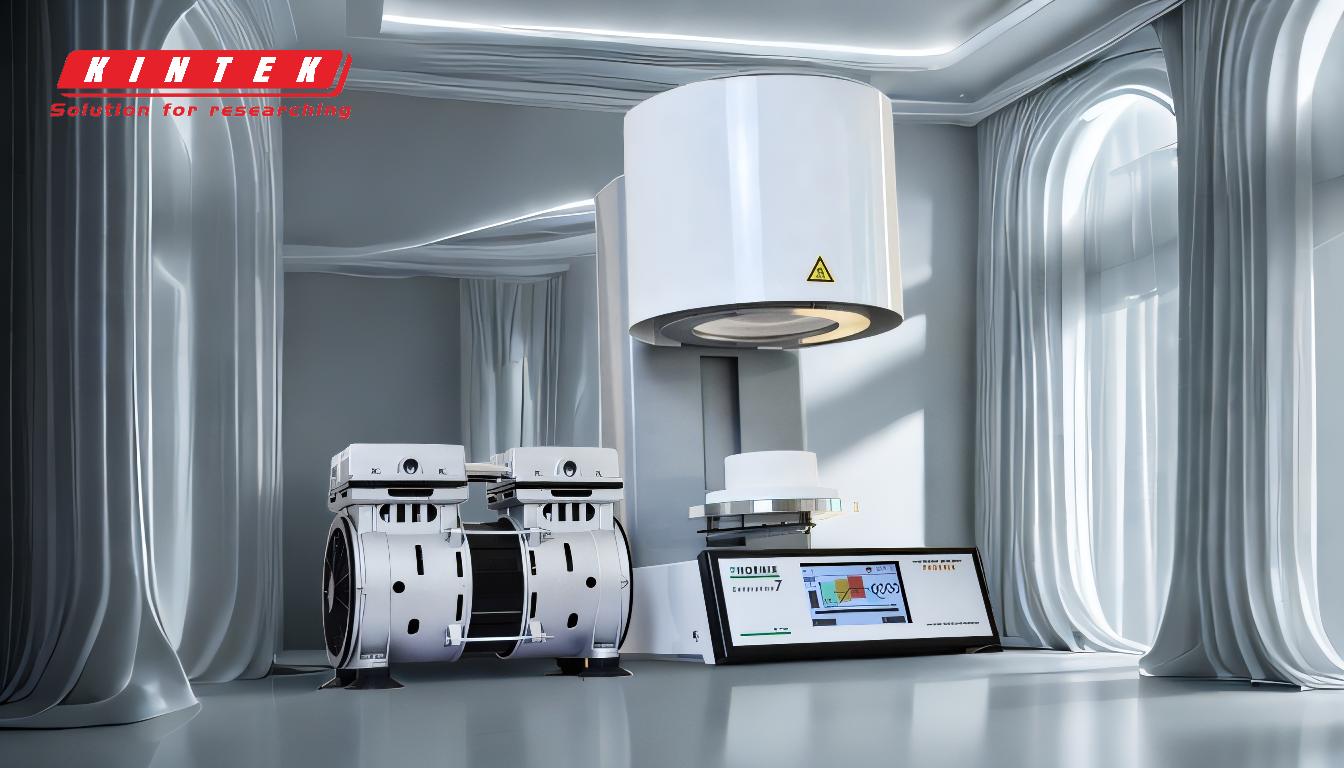
-
Process Methodology:
- Traditional Sintering: Involves compacting powdered material into a mold and then heating it to fuse the particles. The mold defines the shape of the final product.
- Selective Laser Sintering (SLS): Uses a laser to selectively fuse powdered material layer by layer, guided by a CAD file. This process does not require a mold, allowing for more complex geometries.
-
Mold Requirement:
- Traditional Sintering: Requires a mold to shape the object, which can limit design flexibility and increase costs for complex shapes.
- Selective Laser Sintering: Does not require a mold, enabling the creation of intricate and complex designs without additional tooling costs.
-
Production Suitability:
- Traditional Sintering: More suitable for low-cost, mass production due to its accuracy and cost-effectiveness. It is ideal for producing large quantities of identical parts.
- Selective Laser Sintering: Better suited for prototyping and low-volume production. It is not typically used for mass production due to higher costs and slower production rates.
-
Accuracy and Cost:
- Traditional Sintering: Generally more accurate and cheaper for mass production. The use of molds ensures consistent and precise parts.
- Selective Laser Sintering: Less accurate and more expensive compared to traditional sintering. The lack of molds and the layer-by-layer process can introduce slight variations.
-
Design Flexibility:
- Traditional Sintering: Limited by the need for molds, which can restrict the complexity of the designs.
- Selective Laser Sintering: Offers greater design flexibility, allowing for the creation of complex and intricate geometries that would be difficult or impossible to achieve with traditional sintering.
-
Applications:
- Traditional Sintering: Commonly used in industries requiring high-volume production of parts, such as automotive and aerospace.
- Selective Laser Sintering: Often used in industries requiring rapid prototyping, custom parts, and low-volume production, such as medical devices and consumer products.
In summary, while both traditional sintering and selective laser sintering are used to create solid objects from powdered materials, they differ in their methodologies, mold requirements, production suitability, accuracy, cost, design flexibility, and applications. Traditional sintering is more cost-effective and accurate for mass production, whereas selective laser sintering offers greater design flexibility and is better suited for prototyping and low-volume production.
Summary Table:
Aspect | Traditional Sintering | Selective Laser Sintering (SLS) |
---|---|---|
Process Methodology | Compacts powder into a mold, then heats to fuse | Uses a laser to fuse powder layer by layer (no mold) |
Mold Requirement | Requires molds | No molds needed |
Production Suitability | Ideal for mass production | Best for prototyping and low-volume production |
Accuracy | More accurate for mass production | Less accurate due to layer-by-layer process |
Cost | Cost-effective for high-volume production | More expensive, suitable for low-volume |
Design Flexibility | Limited by mold requirements | High flexibility, supports complex geometries |
Applications | Automotive, aerospace (high-volume parts) | Medical devices, consumer products (prototyping) |
Still unsure which sintering method is best for your project? Contact our experts today for personalized advice!