The primary difference between a two-plate mold and a three-plate mold lies in their design and functionality, particularly in how the runner system (the channel through which molten plastic flows into the mold cavity) is managed. In a two-plate mold, the runner system is located on the parting line between the A and B plates and is ejected along with the part. In contrast, a three-plate mold has an additional plate that separates the runner system from the part, allowing the runner to be ejected separately. This design enables more complex part geometries and automated runner removal, making three-plate molds suitable for high-volume production. However, two-plate molds are simpler, more cost-effective, and easier to maintain, making them ideal for less complex parts and lower production volumes.
Key Points Explained:
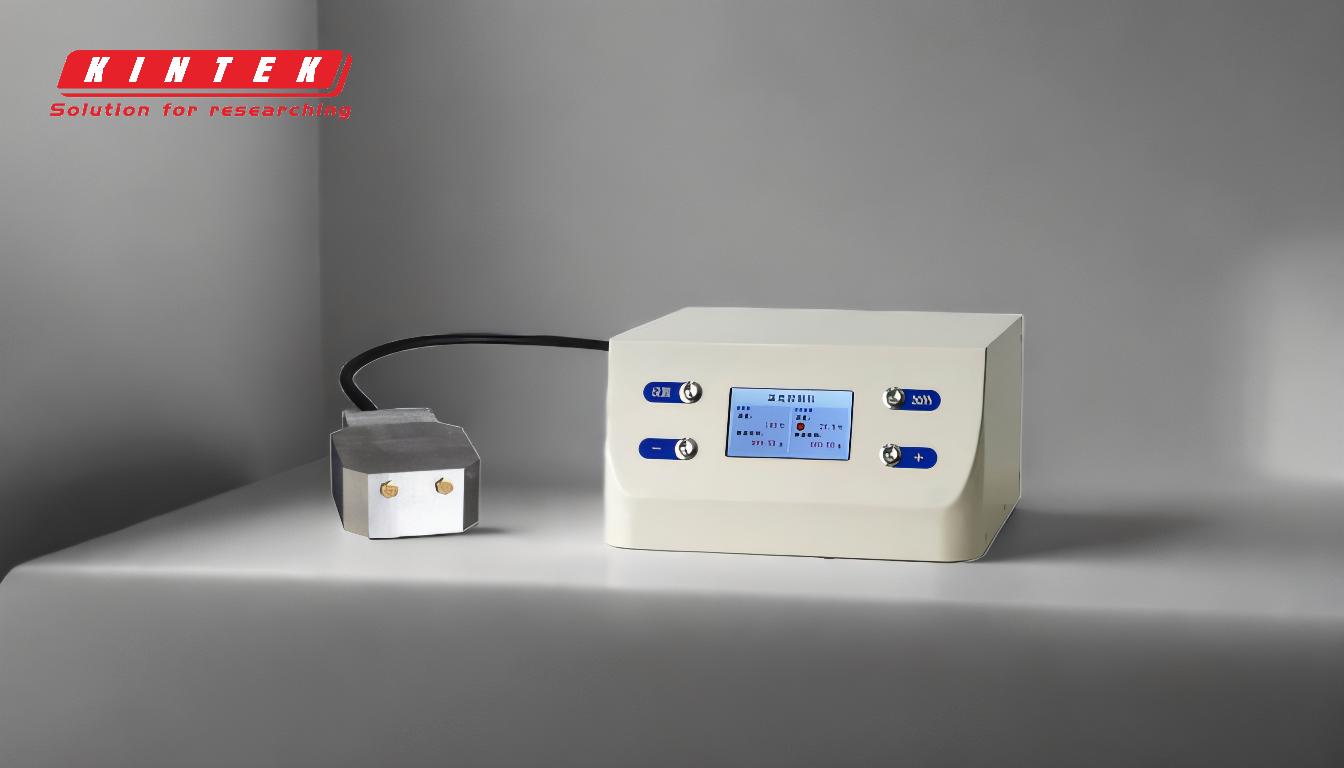
-
Basic Structure and Design:
- Two-Plate Mold: Consists of two main plates: the A plate (cavity side) and the B plate (core side). The runner system is located on the parting line between these plates.
- Three-Plate Mold: Includes an additional plate, known as the runner plate, which separates the runner system from the part. This design allows the runner system to be ejected independently of the part.
-
Runner System Location and Ejection:
- Two-Plate Mold: The runner system is ejected along with the part, as it is located on the parting line. This can complicate the ejection process, especially for parts with complex geometries.
- Three-Plate Mold: The runner system is ejected separately from the part, thanks to the additional runner plate. This allows for more precise control over the ejection process and reduces the risk of damage to the part.
-
Complexity and Cost:
- Two-Plate Mold: Simpler in design, easier to manufacture, and generally less expensive. This makes it a cost-effective choice for simpler parts and lower production volumes.
- Three-Plate Mold: More complex due to the additional plate and the need for a more intricate ejection system. This increases both the initial cost and the maintenance requirements, but it can be justified for high-volume production and more complex part designs.
-
Applications and Suitability:
- Two-Plate Mold: Ideal for simpler parts and lower production volumes where cost and ease of maintenance are primary concerns. It is also easier to set up and operate, making it suitable for smaller-scale operations.
- Three-Plate Mold: Better suited for high-volume production and more complex part geometries. The ability to eject the runner system separately allows for greater design flexibility and can improve the overall efficiency of the molding process.
-
Maintenance and Operational Considerations:
- Two-Plate Mold: Easier to maintain due to its simpler design. Fewer moving parts mean less wear and tear, and any required maintenance is generally more straightforward.
- Three-Plate Mold: Requires more frequent maintenance due to the additional plate and more complex ejection system. However, for high-volume production, the benefits in terms of efficiency and part quality often outweigh the increased maintenance needs.
In summary, the choice between a two-plate and a three-plate mold depends on the specific requirements of the production process, including the complexity of the part, the volume of production, and the available budget. While two-plate molds offer simplicity and cost-effectiveness, three-plate molds provide greater flexibility and efficiency for more demanding applications.
Summary Table:
Aspect | Two-Plate Mold | Three-Plate Mold |
---|---|---|
Design | Simpler, with two main plates (A and B plates). | More complex, with an additional runner plate. |
Runner System | Located on the parting line; ejected with the part. | Separated by the runner plate; ejected independently. |
Cost | Lower initial and maintenance costs. | Higher initial and maintenance costs. |
Applications | Ideal for simpler parts and lower production volumes. | Suitable for high-volume production and complex part geometries. |
Maintenance | Easier to maintain due to fewer moving parts. | Requires more frequent maintenance due to additional complexity. |
Need help choosing the right mold for your production? Contact our experts today for personalized guidance!