Wet bag and dry bag isostatic pressing are two distinct methods used in the manufacturing of high-density components, particularly in industries like ceramics, metals, and advanced materials. Wet bag pressing is better suited for producing large or complex parts and can achieve higher densities due to minimal friction. However, it is less efficient and less automated, making it ideal for small batch or laboratory production. Dry bag pressing, on the other hand, is highly automated, faster, and more efficient, making it ideal for mass production of simpler shapes. The key differences lie in the mold setup, automation potential, production rate, and suitability for different production scales.
Key Points Explained:
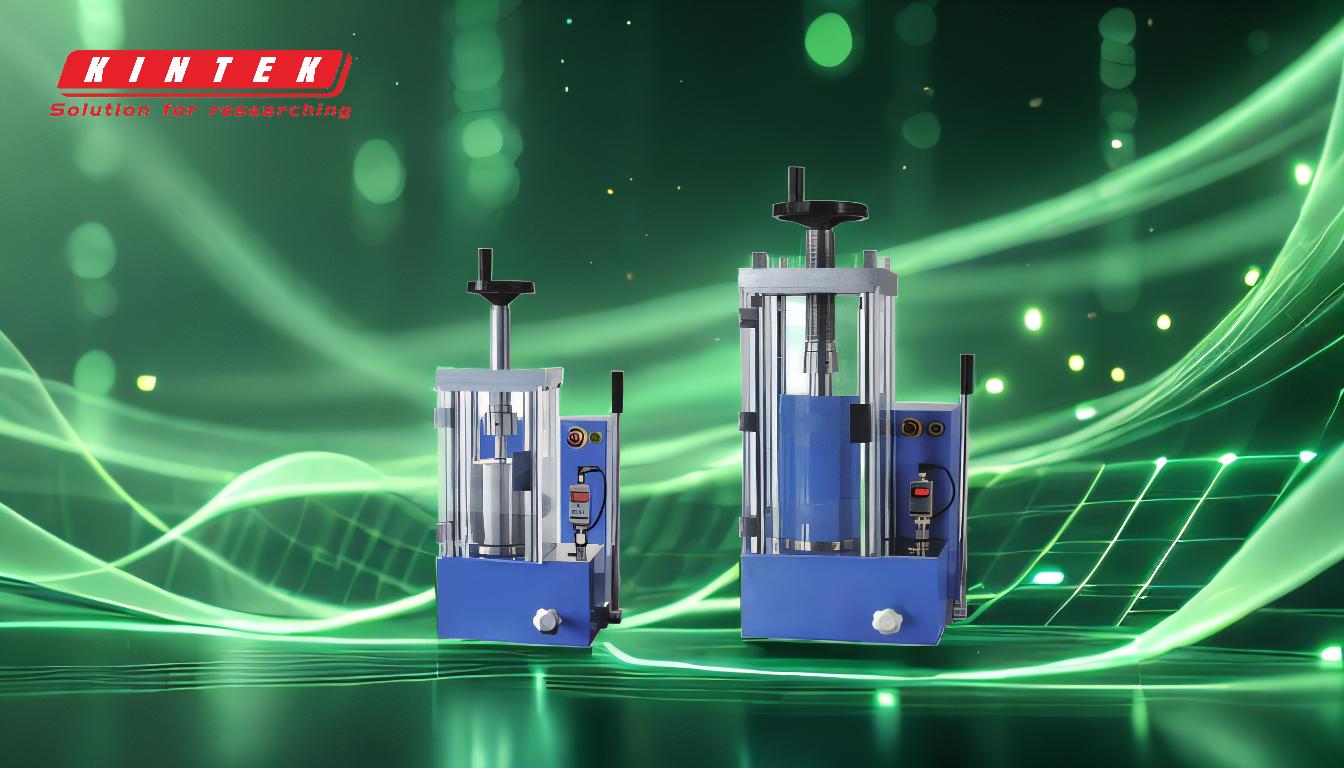
-
Mold Setup and Process:
- Wet Bag Pressing: In this method, the mold (a deformable rubber sleeve) is filled with powder or a preformed green body and then submerged in a pressure vessel containing a pressurized fluid. The mold is not fixed in the vessel, allowing for flexibility in handling large or complex parts. After pressing, the mold is removed from the vessel, making it an intermittent process.
- Dry Bag Pressing: Here, the mold is permanently fixed inside the pressure vessel. The powder is loaded into the mold while it remains in the vessel, and pressure is applied uniformly through the fluid. This setup allows for faster cycles and continuous production.
-
Automation and Productivity:
- Wet Bag Pressing: Due to the need for manual loading and unloading of molds, this method has lower productivity and limited automation. It is more labor-intensive and time-consuming, making it suitable for small batches or specialized applications.
- Dry Bag Pressing: This method is highly automated, enabling continuous production with minimal manual intervention. It can achieve production rates of up to 1500 parts per hour, making it ideal for mass production.
-
Suitability for Production Scales:
- Wet Bag Pressing: Best suited for laboratory preparation, small batch production, or the manufacturing of large and complex parts. Its adaptability allows for multiple molds to be processed simultaneously, but it is less efficient for high-volume production.
- Dry Bag Pressing: Designed for mass production of simpler shapes and parts. Its high automation and faster cycle times make it economically viable for large-scale manufacturing.
-
Density and Quality of Compacts:
- Wet Bag Pressing: Achieves slightly higher densities due to minimal friction during the pressing process. This makes it suitable for applications requiring high-density components.
- Dry Bag Pressing: While it may not achieve the same density levels as wet bag pressing, it still produces components with a compact microstructure, suitable for most industrial applications.
-
Cycle Times and Efficiency:
- Wet Bag Pressing: Cycle times range between 2 and 5 minutes, and the process involves more steps, making it less efficient overall.
- Dry Bag Pressing: Cycle times are shorter, typically 5–10 minutes per run, and the process is streamlined for efficiency, making it faster and more cost-effective for high-volume production.
In summary, wet bag isostatic pressing is ideal for specialized, low-volume, or complex part production, while dry bag isostatic pressing excels in high-volume, automated manufacturing of simpler components. The choice between the two depends on the specific requirements of the production process, including part size, complexity, and desired production scale.
Summary Table:
Aspect | Wet Bag Pressing | Dry Bag Pressing |
---|---|---|
Mold Setup | Mold is submerged in a pressure vessel; not fixed; suitable for large/complex parts | Mold is permanently fixed in the vessel; ideal for simpler shapes |
Automation | Less automated; manual loading/unloading; labor-intensive | Highly automated; minimal manual intervention; continuous production |
Production Scale | Best for small batches, laboratories, or complex parts | Designed for mass production of simpler components |
Density of Compacts | Achieves higher densities due to minimal friction | Slightly lower density but still suitable for most industrial applications |
Cycle Times | 2–5 minutes per cycle; less efficient | 5–10 minutes per cycle; faster and more cost-effective for high-volume production |
Need help choosing the right isostatic pressing method for your production? Contact our experts today for personalized advice!