Ceramics have been widely used in medical implants due to their biocompatibility, wear resistance, and aesthetic properties. However, they also come with several disadvantages that can limit their effectiveness in certain applications. These disadvantages include brittleness, susceptibility to fracture under stress, difficulty in achieving optimal surface finishes for osseointegration, and challenges in manufacturing complex shapes. Additionally, ceramics may not always provide the mechanical strength required for load-bearing implants, and their long-term performance can be affected by environmental factors such as moisture and pH levels. Understanding these limitations is crucial for selecting the right material for specific implant applications.
Key Points Explained:
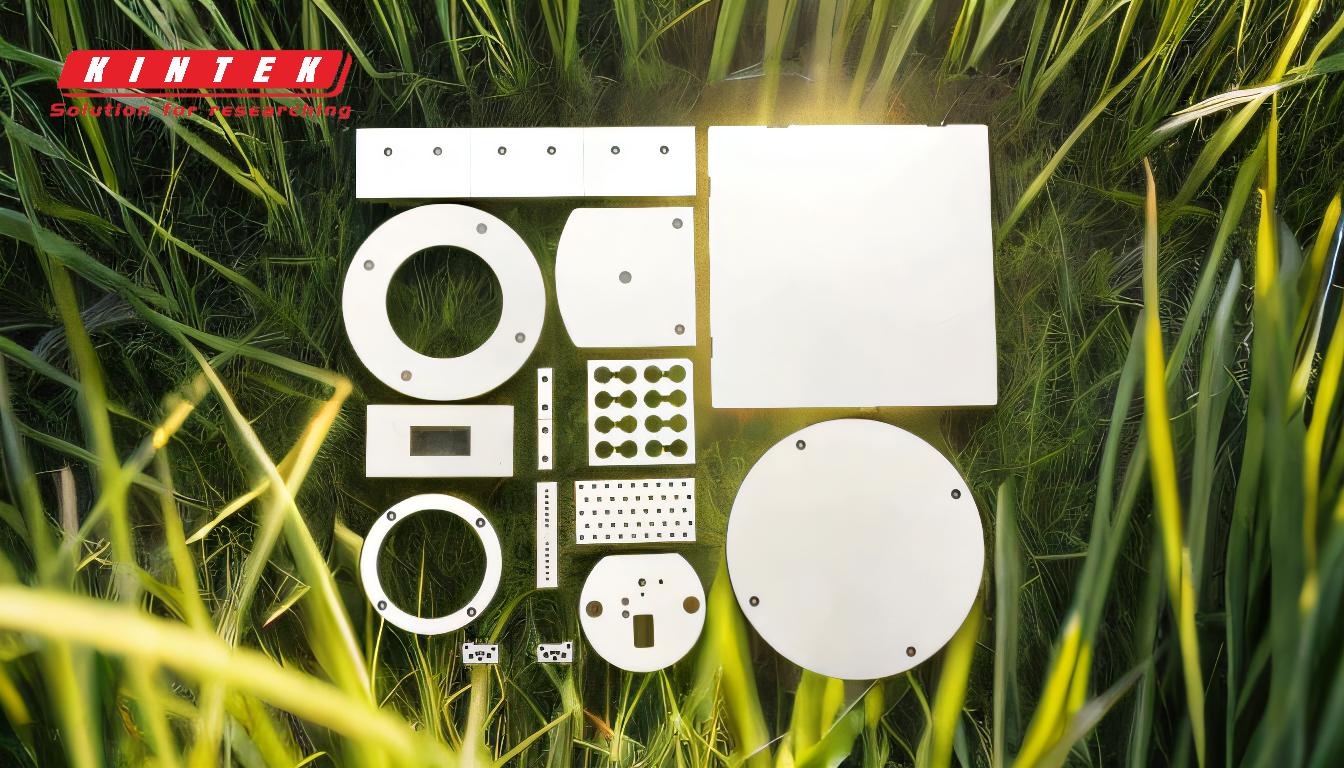
-
Brittleness and Fracture Susceptibility:
- Ceramics are inherently brittle materials, which makes them prone to cracking or fracturing under mechanical stress. This is a significant disadvantage in load-bearing implants, such as hip or knee replacements, where the material must withstand cyclic loading and high stresses.
- Unlike metals, which can deform plastically under stress, ceramics fail catastrophically once their fracture toughness is exceeded. This can lead to sudden implant failure, posing risks to patient safety.
-
Difficulty in Achieving Optimal Surface Finishes:
- For successful osseointegration (the bonding of the implant to bone), the surface of the implant must have specific roughness and porosity. Achieving these properties with ceramics can be challenging due to their hardness and brittleness.
- Improper surface finishing can lead to poor bone integration, increasing the risk of implant loosening and failure over time.
-
Challenges in Manufacturing Complex Shapes:
- Ceramics are difficult to machine and shape into complex geometries required for certain implants. This limits their use in applications where intricate designs are necessary for optimal performance.
- The manufacturing process for ceramic implants often involves high-temperature sintering, which can introduce defects such as microcracks or residual stresses, further compromising their mechanical properties.
-
Inadequate Mechanical Strength for Load-Bearing Applications:
- While ceramics are strong in compression, they often lack the tensile and shear strength required for load-bearing implants. This makes them less suitable for applications where the implant must endure significant mechanical forces.
- Metals and polymers are often preferred for such applications due to their superior mechanical properties and ability to withstand cyclic loading.
-
Environmental Sensitivity:
- Ceramics can be sensitive to environmental factors such as moisture, pH, and temperature changes. For example, in a moist environment, certain ceramics may undergo slow degradation, leading to a reduction in their mechanical properties over time.
- This sensitivity can affect the long-term performance of ceramic implants, particularly in dynamic or harsh physiological conditions.
-
Cost and Availability:
- High-purity ceramics required for medical implants can be expensive to produce and process. This increases the overall cost of ceramic implants compared to alternatives like metals or polymers.
- Additionally, the specialized manufacturing techniques and equipment needed for ceramic implants may limit their availability in certain regions or healthcare settings.
In summary, while ceramics offer several advantages for medical implants, their brittleness, manufacturing challenges, and sensitivity to environmental factors make them less suitable for certain applications. Careful consideration of these disadvantages is essential when selecting materials for implants, particularly in load-bearing or complex anatomical sites.
Summary Table:
Disadvantage | Key Details |
---|---|
Brittleness and Fracture Susceptibility | Prone to cracking under stress; catastrophic failure in load-bearing implants. |
Difficulty in Surface Finishing | Hard to achieve optimal roughness and porosity for osseointegration. |
Challenges in Manufacturing | Complex shapes are difficult to produce; high-temperature sintering risks. |
Inadequate Mechanical Strength | Lacks tensile and shear strength for load-bearing applications. |
Environmental Sensitivity | Degrades in moist or pH-varying environments; affects long-term performance. |
Cost and Availability | Expensive to produce; limited availability due to specialized manufacturing. |
Need help selecting the right material for your medical implants? Contact our experts today!