The effect of ball milling time on particle size is significant, as it directly influences the reduction of particle size through mechanical grinding. During the initial hours of milling (1–5 hours), the most substantial reduction in particle size occurs, with average particle size decreasing from 160 μm to 25 μm. Beyond this period, the rate of size reduction slows, but continued milling can still achieve finer particles, with sizes dropping below 10 μm after 10 hours of milling. Longer milling times and smaller grinding balls are generally required to produce smaller particles, as they increase the frequency of collisions and the efficiency of particle breakdown. Additionally, repeated milling cycles contribute to the erosion of larger particles, resulting in a higher proportion of smaller, nanosized fragments.
Key Points Explained:
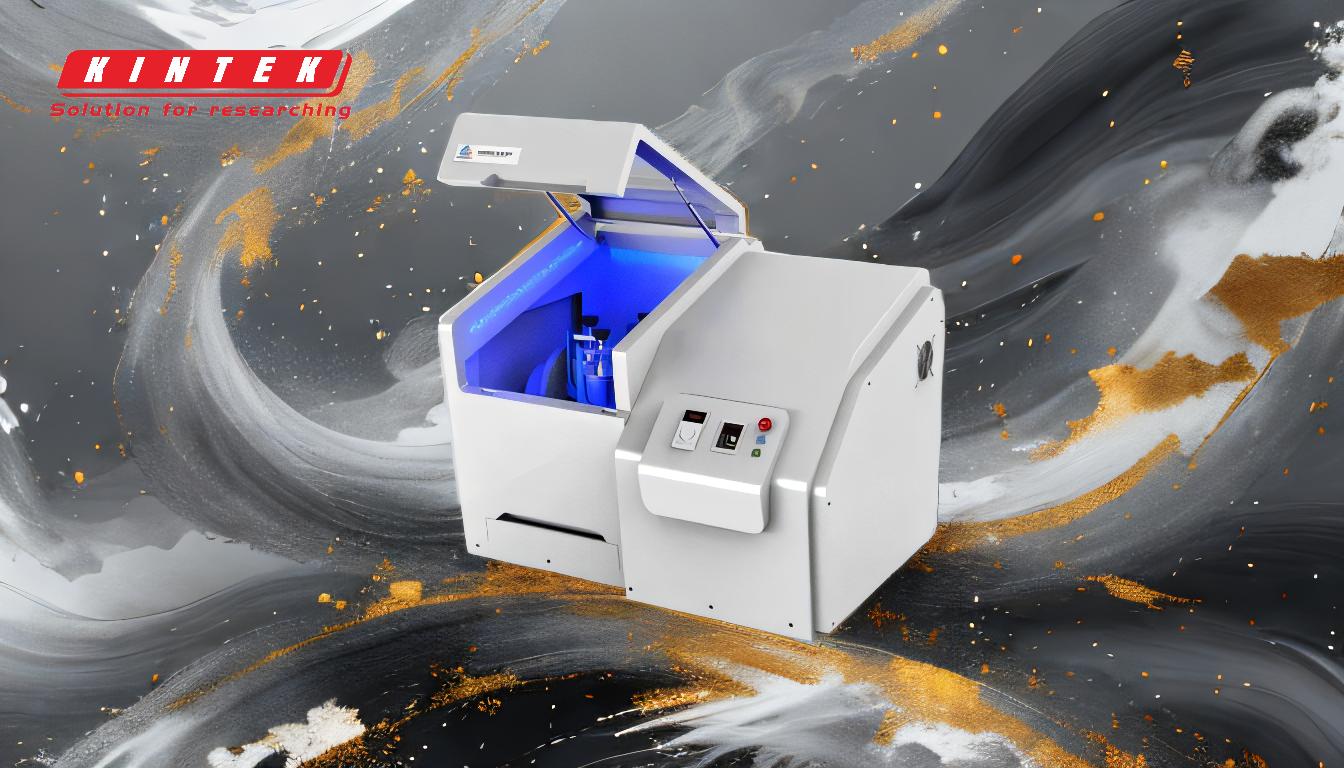
-
Initial Rapid Particle Size Reduction (1–5 Hours):
- The most significant reduction in particle size occurs during the first 1–5 hours of ball milling.
- Average particle size decreases dramatically, from 160 μm to 25 μm, during this period.
- This phase is characterized by the breakdown of larger particles into smaller fragments due to intense mechanical forces.
-
Slower Reduction Beyond 5 Hours:
- After the initial 5 hours, the rate of particle size reduction slows.
- Continued milling beyond this period still reduces particle size, but at a diminishing rate.
- For example, after 10 hours of milling, particle sizes can drop below 10 μm.
-
Importance of Milling Time and Ball Size:
- Longer milling times are generally required to achieve finer particles.
- Smaller grinding balls are more effective in producing smaller particles, as they increase the frequency of collisions and the efficiency of particle breakdown.
- The combination of longer milling times and smaller balls enhances the grinding process.
-
Effect of Repeated Milling Cycles:
- Increasing the number of milling cycles leads to a higher proportion of smaller particles.
- Repeated cycles cause the erosion of larger particles, resulting in the formation of nanosized fragments.
- This process is particularly evident in cryomilling, where smaller fragments break off from larger particles over time.
-
Practical Implications for Equipment and Consumable Purchasers:
- For purchasers aiming to achieve specific particle sizes, understanding the relationship between milling time and particle size is crucial.
- Selecting appropriate milling equipment with adjustable time settings and suitable ball sizes can optimize the grinding process.
- Longer milling times and smaller balls may be necessary for achieving finer particles, but this must be balanced against energy consumption and operational costs.
By carefully considering these factors, purchasers can make informed decisions about the equipment and consumables needed to achieve their desired particle size outcomes.
Summary Table:
Milling Time | Particle Size Reduction | Key Insights |
---|---|---|
1–5 hours | 160 μm → 25 μm | Most significant reduction due to intense mechanical forces. |
Beyond 5 hours | Slower reduction | Particle sizes drop below 10 μm after 10 hours. |
Longer milling | Finer particles | Smaller grinding balls enhance efficiency. |
Repeated cycles | Nanosized fragments | Erosion of larger particles increases smaller fragments. |
Need help optimizing your ball milling process? Contact our experts today to achieve your desired particle size!