The effect of frequency on induction hardening is significant and directly influences the depth and efficiency of the hardening process. Higher frequencies result in a greater current density difference between the surface and the interior of the workpiece, leading to a thinner heating layer. This allows for precise control over the depth of hardening, making it ideal for applications requiring shallow hardening. When the surface temperature exceeds the critical point of the steel, rapid cooling can be applied to achieve the desired surface hardness. This relationship between frequency and hardening depth is crucial for selecting the appropriate induction heating parameters for specific applications.
Key Points Explained:
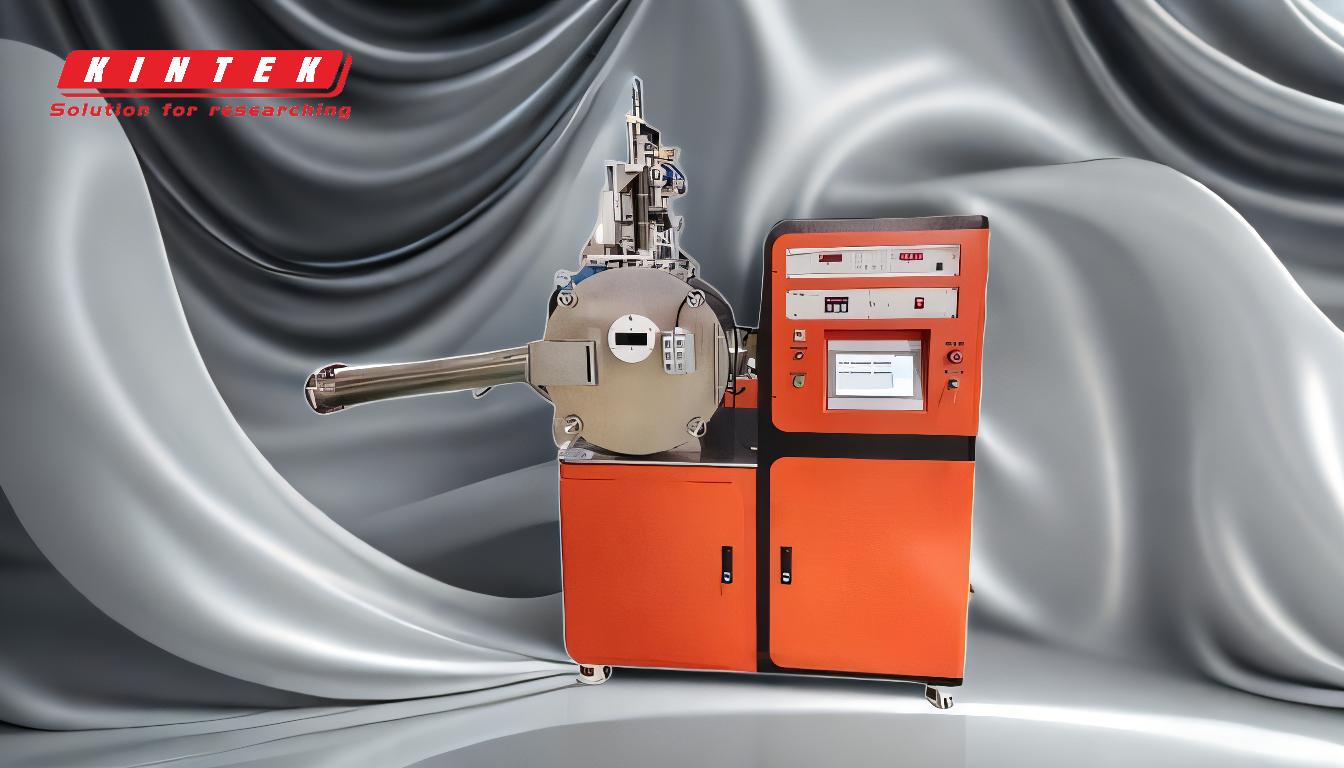
-
Relationship Between Frequency and Current Density:
- Higher frequencies cause a greater concentration of current near the surface of the workpiece, a phenomenon known as the skin effect.
- This results in a higher current density at the surface compared to the interior, which directly affects the depth of heating.
-
Effect on Heating Layer Thickness:
- As frequency increases, the heating layer becomes thinner because the current is concentrated closer to the surface.
- This allows for precise control over the depth of hardening, which is particularly useful for applications requiring shallow hardening, such as gears or bearings.
-
Critical Temperature and Rapid Cooling:
- The heating layer must reach a temperature above the critical point of the steel to enable phase transformation (e.g., austenitization).
- Once this temperature is achieved, rapid cooling (quenching) is applied to lock in the hardened microstructure, resulting in a hard surface layer.
-
Applications and Practical Considerations:
- High-frequency induction hardening is ideal for small or thin components where shallow hardening is required.
- Lower frequencies are used for larger components or when deeper hardening is needed, as the current penetrates further into the material.
-
Advantages of Higher Frequency Induction Hardening:
- Precision: Allows for targeted hardening of specific areas.
- Efficiency: Reduces energy waste by focusing heat on the surface.
- Speed: Faster heating cycles due to concentrated energy.
-
Limitations and Trade-offs:
- Higher frequencies may not be suitable for components requiring deep hardening.
- Equipment capable of generating high frequencies can be more expensive and complex.
By understanding the relationship between frequency and induction hardening, manufacturers can optimize the process to achieve the desired surface properties for their specific applications. This knowledge is essential for selecting the right equipment and parameters to ensure consistent and high-quality results.
Summary Table:
Aspect | Details |
---|---|
Frequency & Current Density | Higher frequencies increase surface current density (skin effect). |
Heating Layer Thickness | Higher frequencies result in thinner heating layers. |
Critical Temperature | Surface must exceed steel's critical point for phase transformation. |
Applications | High-frequency: shallow hardening (gears, bearings). Low-frequency: deep hardening. |
Advantages | Precision, efficiency, and faster heating cycles. |
Limitations | Not suitable for deep hardening; higher equipment costs. |
Optimize your induction hardening process with the right frequency—contact our experts today!