Sintering temperature plays a critical role in determining the final properties of ceramics, including strength, hardness, chemical stability, and microstructure. Precise control of sintering temperature is essential to achieve optimal results, as deviations can lead to issues such as excessive grain growth, reduced strength, or compromised dimensional accuracy. For example, zirconia ceramics exhibit maximum strength when sintered at around 1500°C, with even small deviations (e.g., ±150°C) significantly impacting performance. The sintering process involves diffusion mechanisms that are highly temperature-dependent, making consistent temperature control during heating, holding, and cooling phases vital for producing high-quality ceramics with uniform microstructure and desired mechanical properties.
Key Points Explained:
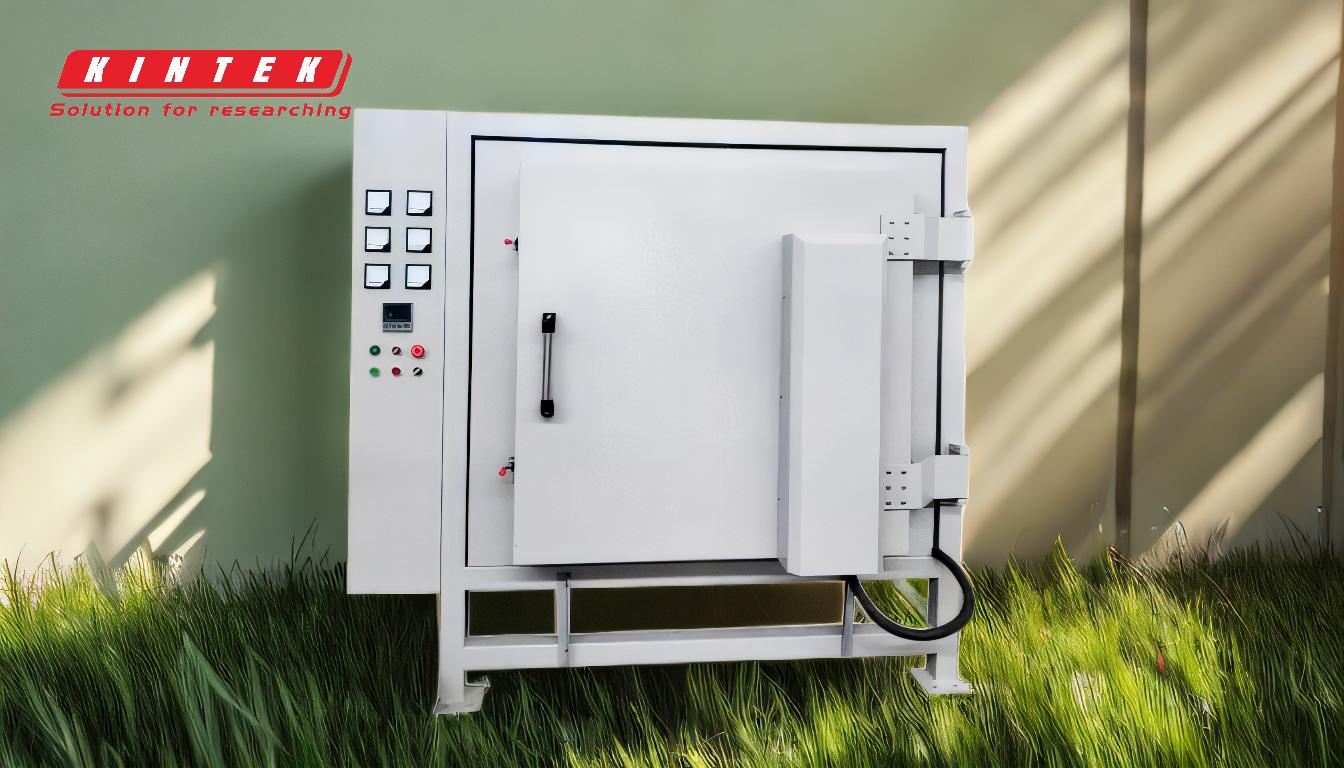
-
Importance of Sintering Temperature
- Sintering is the process of transforming ceramic powder into a dense, polycrystalline material through diffusion and mass transfer.
- Temperature directly influences grain boundary diffusion and bulk diffusion, which are critical for achieving densification and a uniform microstructure.
- Proper sintering temperature ensures the ceramic's strength, hardness, chemical stability, and dimensional accuracy.
-
Optimal Sintering Temperature for Zirconia
- Studies show that sintering zirconia at approximately 1500°C maximizes its strength.
- Deviations of ±150°C from this temperature can lead to grain growth, reducing the material's strength.
- Higher temperatures (e.g., above 1500°C) result in significant drops in strength due to excessive grain coarsening.
-
Impact of Temperature on Microstructure
- Sintering temperature controls grain size and distribution, which are critical for mechanical properties.
- Excessive temperatures can cause rapid grain growth, leading to a non-uniform microstructure and reduced toughness.
- Precise temperature control (e.g., not exceeding 1450°C for hard metals) preserves small grain sizes, enhancing hardness and wear resistance.
-
Temperature Control During Sintering Phases
- The ramp rate from 900°C to the top temperature, the consistency of temperature during the hold phase, and the cooling rate back to 900°C are critical for achieving optimal results.
- Inconsistent temperature control during these phases can lead to defects such as warping, cracking, or uneven densification.
-
Applications in Dental Ceramics
- For dental zirconia crowns, veneers, and implants, sintering temperature directly affects color, size, and strength.
- Proper temperature control ensures that intricate details and workmanship are preserved, maintaining the aesthetic and functional quality of the final product.
-
Economic and Manufacturing Benefits
- Sintering enables the production of complex shapes and geometries that are difficult to achieve with traditional manufacturing methods.
- It allows for lower-cost tooling and rapid mass production while maintaining precision and repeatability.
- Combining multiple materials through sintering can enhance properties such as toughness and abrasion resistance.
-
Challenges and Considerations
- Achieving precise temperature control requires advanced equipment and monitoring systems.
- The sintering environment (e.g., atmosphere, pressure) and material composition (e.g., particle size, distribution) also influence the outcome.
- Deviations in temperature can compromise the ceramic's performance, making process optimization essential.
In summary, sintering temperature is a critical factor in ceramic manufacturing, influencing microstructure, mechanical properties, and final product quality. Precise control of temperature during all phases of sintering is essential to achieve the desired properties and ensure consistency in advanced ceramic applications.
Summary Table:
Key Aspect | Details |
---|---|
Importance of Sintering Temperature | Influences grain boundary diffusion, densification, and microstructure. |
Optimal Sintering for Zirconia | ~1500°C maximizes strength; deviations of ±150°C reduce performance. |
Impact on Microstructure | Controls grain size; excessive temperatures cause non-uniform structures. |
Temperature Control Phases | Ramp rate, hold phase, and cooling rate are critical for consistent results. |
Applications in Dental Ceramics | Affects color, size, and strength of dental crowns and implants. |
Economic Benefits | Enables complex shapes, lower-cost tooling, and rapid mass production. |
Challenges | Requires advanced equipment and precise monitoring to avoid defects. |
Achieve optimal ceramic properties with precise sintering temperature control—contact our experts today!