The sintering temperature plays a critical role in determining the density of a sintered body. Higher sintering temperatures generally lead to increased density by reducing porosity, as the material particles bond more effectively and pores shrink or close. However, excessively high temperatures can cause grain growth, which may degrade material properties like strength and hardness. Conversely, insufficient sintering temperatures result in incomplete densification, leaving the material porous and weak. Optimal sintering temperature balances densification and material integrity, ensuring the desired mechanical properties are achieved.
Key Points Explained:
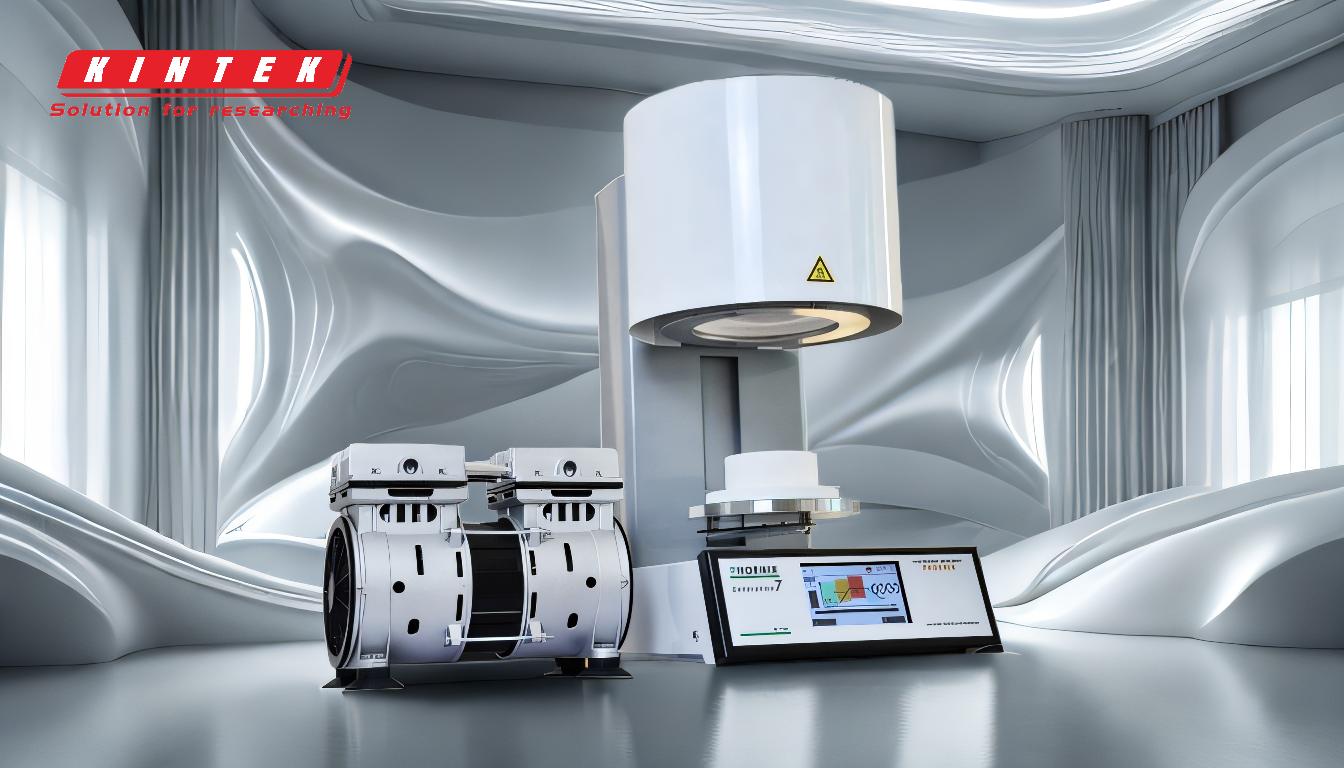
-
Relationship Between Sintering Temperature and Density:
- Sintering temperature directly influences the density of the sintered body.
- Higher temperatures promote particle bonding and pore closure, leading to increased density.
- Insufficient temperatures result in incomplete densification, leaving the material porous.
-
Effect of Excessive Sintering Temperature:
- Extremely high temperatures can cause grain growth, which negatively impacts material properties.
- Grain growth reduces strength and hardness, as larger grains create weaker grain boundaries.
- Excessive temperatures may also lead to defects such as cracking or warping.
-
Optimal Sintering Temperature:
- There is an ideal sintering temperature range that maximizes density while maintaining material integrity.
- For example, zirconia achieves maximum strength at around 1500℃. Deviations from this temperature, even by 150℃, can significantly reduce strength due to grain growth.
-
Role of Sintering Time:
- Sintering time works in tandem with temperature to influence density.
- Longer sintering times at optimal temperatures can further enhance densification.
- However, excessively long sintering times at high temperatures can lead to over-sintering, causing grain growth and property degradation.
-
Impact of Sintering Atmosphere:
- The sintering atmosphere (e.g., reducing or inert) affects the final density and properties.
- A reducing atmosphere prevents oxidation and promotes densification by reducing surface oxides.
- The choice of atmosphere can optimize the sintering process for specific materials.
-
Microstructural Changes During Sintering:
- Sintering alters the microstructure, including grain size, pore size, and grain boundary distribution.
- These changes directly influence the material's mechanical properties, such as strength and durability.
- Proper control of sintering temperature ensures a fine-grained, dense microstructure with minimal defects.
-
Balancing Density and Material Properties:
- The goal of sintering is to achieve a fully dense part with the desired mechanical properties.
- Overemphasis on density alone can lead to compromised strength or hardness due to grain growth.
- A balanced approach ensures optimal density and material performance.
In summary, sintering temperature is a critical factor in determining the density and overall quality of a sintered material. Proper control of temperature, time, and atmosphere ensures a dense, strong, and durable product, while deviations from optimal conditions can lead to defects or degraded properties.
Summary Table:
Factor | Impact on Sintered Material |
---|---|
Higher Sintering Temperature | Increases density by reducing porosity; excessive temperatures cause grain growth and defects. |
Insufficient Temperature | Results in incomplete densification, leaving the material porous and weak. |
Optimal Temperature | Balances densification and material integrity, ensuring strength and durability. |
Sintering Time | Longer times enhance densification; excessive times at high temperatures cause grain growth. |
Sintering Atmosphere | Affects density and properties; reducing atmospheres prevent oxidation and promote densification. |
Microstructural Changes | Influences grain size, pore size, and grain boundaries, directly affecting mechanical properties. |
Achieve the perfect balance of density and material strength—contact our experts today to optimize your sintering process!