Sputtering pressure is a critical parameter in the sputtering process, significantly influencing the energy distribution, direction, and deposition quality of sputtered particles. At higher pressures, sputtered ions collide more frequently with gas atoms, leading to a diffusive motion that moderates their energy and direction. This results in a more random deposition pattern, which can improve coverage but may reduce the kinetic energy of the particles. Conversely, lower pressures allow for more ballistic impacts, where particles retain higher energy and directionality, leading to denser and more uniform thin films. The pressure also affects the sputtering rate, which is determined by factors such as the sputter yield, ion current density, and material properties. Understanding and controlling sputtering pressure is essential for optimizing film quality, deposition rate, and process efficiency.
Key Points Explained:
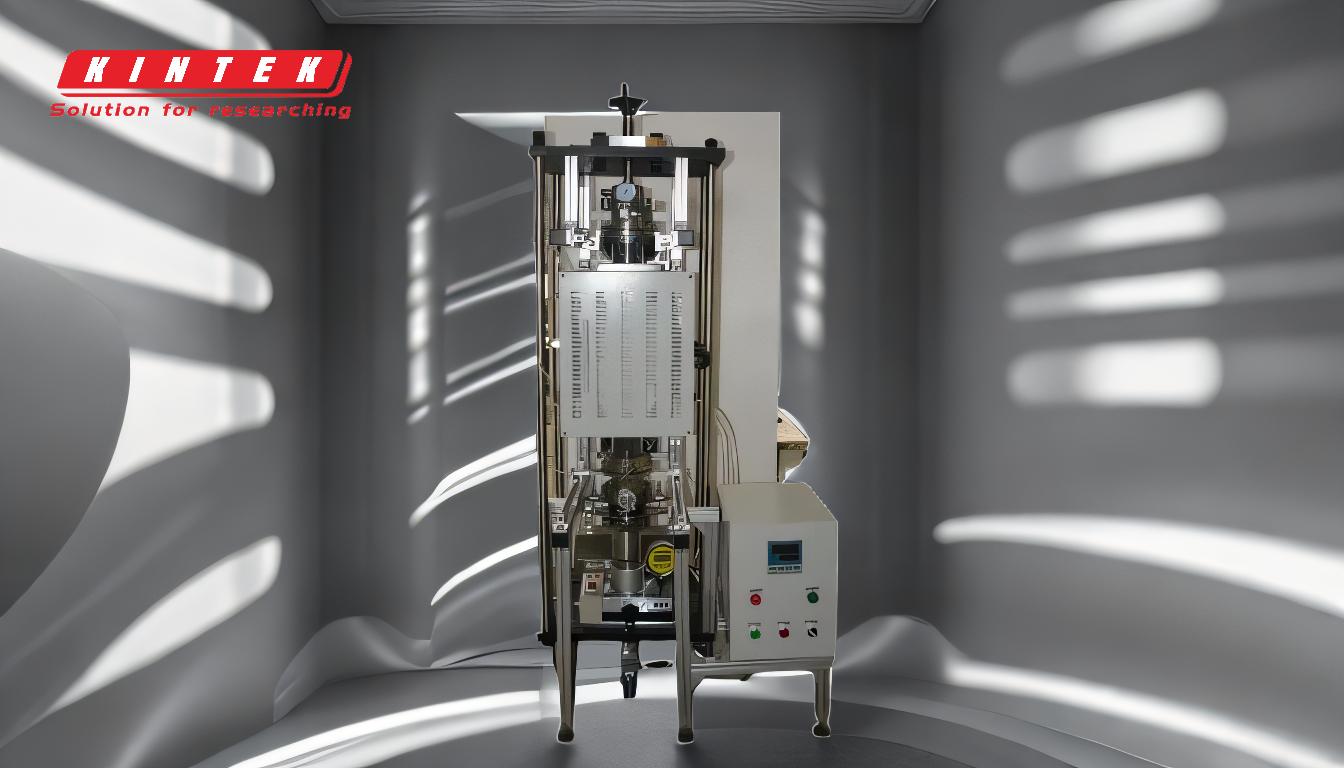
-
Impact on Particle Energy and Direction:
- At higher sputtering pressures, sputtered ions collide more frequently with gas atoms, leading to a diffusive motion. This moderates their kinetic energy and randomizes their direction, resulting in a more uniform but less energetic deposition.
- At lower pressures, particles experience fewer collisions, retaining higher kinetic energy and more directional motion, which can lead to denser and more uniform thin films.
-
Effect on Deposition Quality:
- Higher pressures improve coverage by spreading the deposition more evenly across the substrate, but the reduced kinetic energy of particles may result in less dense films.
- Lower pressures favor high-energy ballistic impacts, which enhance film density and uniformity but may reduce coverage if not properly controlled.
-
Influence on Sputtering Rate:
- The sputtering rate, defined as the number of monolayers per second sputtered from the target, is influenced by pressure through its effect on the ion current density and mean free path of particles.
- Higher pressures can reduce the sputtering rate due to increased collisions and energy loss, while lower pressures can increase the rate by allowing more direct and energetic impacts.
-
Role in Process Control:
- Pressure, along with deposition temperature, is a decisive process parameter that must be carefully controlled to achieve desired film properties.
- Adjusting the background gas pressure allows the process to range from high-energy ballistic impacts to low-energy thermalized motion, providing flexibility in tailoring film characteristics.
-
Interaction with Other Factors:
- The sputtering yield, which depends on the energy of incident ions, the mass of ions and target atoms, and the binding energy of atoms in the solid, is indirectly influenced by pressure through its effect on ion energy and collision frequency.
- The type of power source (DC or RF) and material properties also interact with pressure to determine the overall sputtering process efficiency and film quality.
By understanding these key points, equipment and consumable purchasers can make informed decisions about optimizing sputtering pressure to achieve specific film properties and process goals.
Summary Table:
Aspect | High Pressure | Low Pressure |
---|---|---|
Particle Energy & Direction | More collisions with gas atoms, lower kinetic energy, random deposition pattern. | Fewer collisions, higher kinetic energy, directional motion for denser films. |
Deposition Quality | Improved coverage but less dense films due to reduced particle energy. | Enhanced film density and uniformity, but coverage may decrease. |
Sputtering Rate | Reduced rate due to increased collisions and energy loss. | Increased rate with more direct and energetic impacts. |
Process Control | Adjustable to achieve low-energy thermalized motion for specific film properties. | Adjustable to achieve high-energy ballistic impacts for tailored characteristics. |
Need help optimizing sputtering pressure for your process? Contact our experts today!