An endothermic atmosphere is a controlled gas environment created by the catalytic reaction of a hydrocarbon gas (such as liquefied petroleum gas, natural gas, or city gas) with air at high temperatures. This process occurs in a generator or converter equipped with a catalyst, typically nickel-impregnated refractory, and is externally heated to temperatures between 1,000°C and 1,150°C. The resulting atmosphere primarily consists of carbon monoxide (CO), hydrogen (H2), and nitrogen (N2), with trace amounts of water vapor (H2O), carbon dioxide (CO2), and hydrocarbons. This atmosphere is widely used in heat treatment processes, such as carburizing and annealing, to prevent oxidation and decarburization of metals while enabling precise control over surface chemistry.
Key Points Explained:
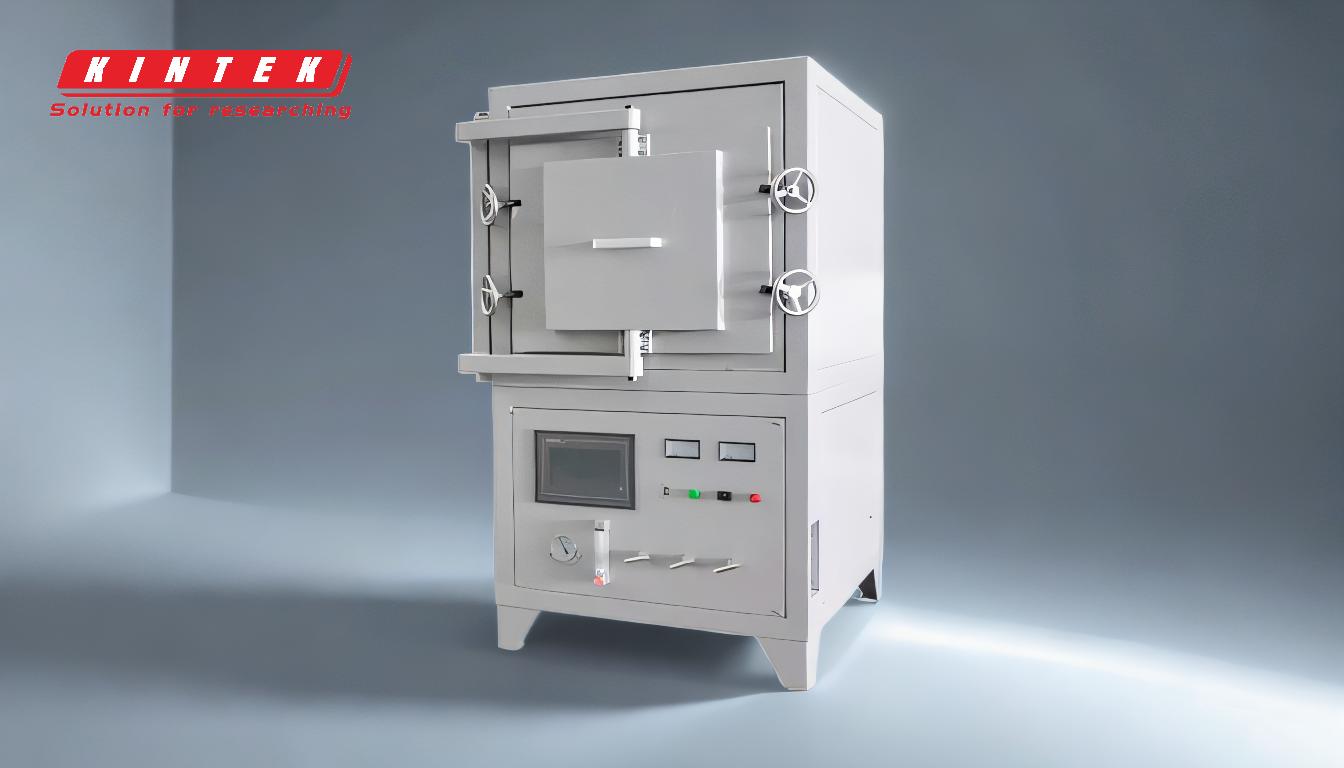
-
Definition and Purpose of Endothermic Atmosphere:
- An endothermic atmosphere is a gas mixture produced through a controlled chemical reaction. It is primarily used in industrial heat treatment processes to create a protective environment that prevents oxidation and decarburization of metals while allowing for precise control over surface properties.
-
Raw Materials and Process:
- The process begins with a hydrocarbon gas, such as liquefied petroleum gas, natural gas, or city gas, mixed with air in a specific ratio. This mixture is then passed through a reaction chamber or generator containing a catalyst.
- The catalyst, often nickel-impregnated refractory, facilitates the reaction at high temperatures, typically between 1,000°C and 1,150°C. External heating is applied to maintain the required temperature for the reaction to occur.
-
Chemical Composition:
- The primary components of an endothermic atmosphere are:
- Carbon monoxide (CO): 20–24%
- Hydrogen (H2): 30–41%
- Nitrogen (N2): 38–45%
- Trace amounts of water vapor (H2O), carbon dioxide (CO2), and hydrocarbons are also present. These components are critical for achieving the desired metallurgical properties during heat treatment.
- The primary components of an endothermic atmosphere are:
-
Applications in Heat Treatment:
- Endothermic atmospheres are widely used in processes such as:
- Carburizing: Introducing carbon into the surface of steel to increase hardness.
- Annealing: Softening metals to improve machinability or ductility.
- Neutral hardening: Preventing oxidation and decarburization while hardening metals.
- The controlled environment ensures consistent results and enhances the quality of treated materials.
- Endothermic atmospheres are widely used in processes such as:
-
Advantages of Using Endothermic Atmospheres:
- Oxidation Prevention: The atmosphere creates a reducing environment that prevents the formation of oxides on metal surfaces.
- Decarburization Control: By maintaining a specific carbon potential, the atmosphere prevents the loss of carbon from the metal surface.
- Precision and Consistency: The controlled composition allows for precise adjustments to meet specific metallurgical requirements.
-
Equipment and Catalyst:
- The generator or converter used in the process is designed to withstand high temperatures and corrosive environments. The catalyst, typically nickel-based, is critical for ensuring the efficient conversion of the hydrocarbon-air mixture into the desired gas composition.
-
Cooling and Delivery:
- After the reaction, the gas mixture is rapidly cooled to stabilize its composition before being delivered to the heat treatment furnace. This ensures that the atmosphere remains consistent and effective during the treatment process.
By understanding these key points, equipment and consumable purchasers can make informed decisions about the use of endothermic atmospheres in their operations, ensuring optimal results in heat treatment processes.
Summary Table:
Key Aspect | Details |
---|---|
Definition | Controlled gas environment for heat treatment, preventing oxidation. |
Raw Materials | Hydrocarbon gas (e.g., LPG, natural gas) mixed with air. |
Process | Catalytic reaction at 1,000°C–1,150°C using nickel-based catalysts. |
Composition | CO (20–24%), H2 (30–41%), N2 (38–45%), with traces of H2O, CO2, hydrocarbons. |
Applications | Carburizing, annealing, neutral hardening. |
Advantages | Prevents oxidation, controls decarburization, ensures precision. |
Equipment | High-temperature generators with nickel-based catalysts. |
Optimize your heat treatment processes with endothermic atmospheres—contact our experts today for tailored solutions!