Evaporative deposition is a manufacturing process used to create thin film coatings on substrates by vaporizing a source material and allowing the vapor to condense onto the substrate. This technique is widely used to achieve coatings with specific properties such as insulation, conductivity, or wear resistance. The process involves several methods, including thermal evaporation, electron beam evaporation, and sputter deposition, each with unique mechanisms and applications. Thermal evaporation, for instance, heats the source material until it vaporizes, while electron beam evaporation uses a high-energy electron beam for vaporization. The process typically occurs in a vacuum chamber to ensure a free path for the vaporized particles to deposit uniformly on the substrate.
Key Points Explained:
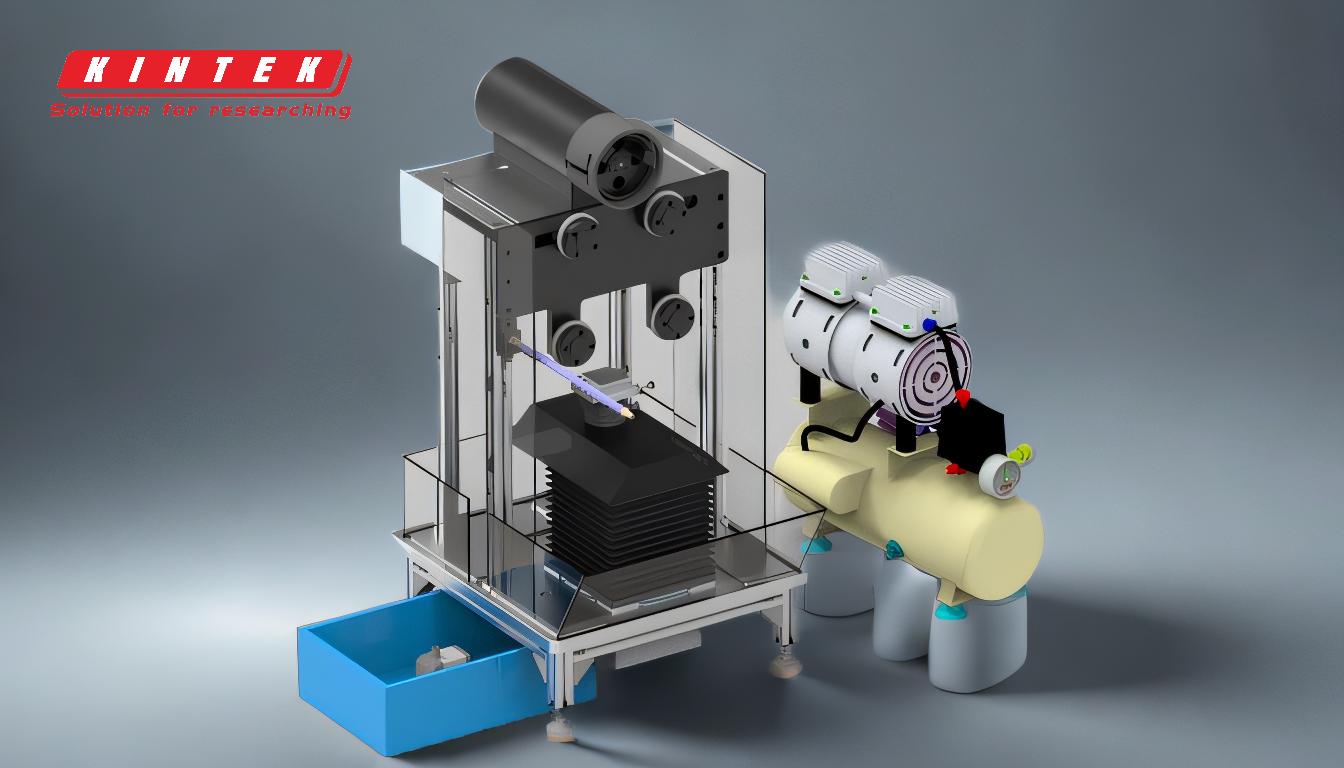
-
Overview of Evaporative Deposition:
- Evaporative deposition is a process where a material is vaporized and then deposited onto a substrate to form a thin film.
- This technique is commonly used to create coatings with specific functional properties such as insulation, conductivity, or wear resistance.
- The process is carried out in a vacuum chamber to ensure a free path for the vaporized particles and to maintain a high-vacuum environment.
-
Techniques Used in Evaporative Deposition:
-
Thermal Evaporation:
- The source material is heated until it vaporizes.
- The evaporation boat is heated by an electric current, causing the material to melt and evaporate.
- The gaseous material molecules are accelerated by heating and deposit on the substrate to form a film.
-
Electron Beam Evaporation:
- A high-energy electron beam is used to vaporize the material.
- This method allows for precise control over the deposition process and is suitable for materials with high melting points.
-
Sputter Deposition:
- A plasma or ion beam is used to knock off atoms from the source material.
- The sputtered atoms then deposit onto the substrate to form a thin film.
-
Other Techniques:
- Laser Beam Evaporation: Uses a laser to vaporize the material.
- Arc Evaporation: Utilizes an electric arc to vaporize the material.
- Molecular Beam Epitaxy (MBE): A highly controlled process used for growing thin films with precise atomic layer control.
- Ion Plating Evaporation: Combines evaporation with ion bombardment to enhance film adhesion and density.
-
Thermal Evaporation:
-
Process Details:
- The process occurs in a vacuum chamber to minimize contamination and ensure a free path for the vaporized particles.
- A vacuum pump maintains the high-vacuum environment necessary for the process.
- The vapor stream crosses the chamber, and coating particles attach to the substrate, forming a thin film.
-
Applications:
- Evaporative deposition is used in various industries to create thin film coatings with specific properties.
- Common applications include creating coatings for insulation, conductivity, wear resistance, and optical properties.
- The technique is also used in the production of semiconductors, solar cells, and optical coatings.
-
Advantages and Considerations:
-
Advantages:
- High purity of the deposited films due to the vacuum environment.
- Ability to deposit a wide range of materials, including metals, alloys, and compounds.
- Precise control over film thickness and composition.
-
Considerations:
- The process requires specialized equipment and a high-vacuum environment, which can be costly.
- Some materials may require high temperatures or specific conditions for vaporization, limiting the range of materials that can be used.
-
Advantages:
By understanding these key points, one can appreciate the complexity and versatility of the evaporative deposition technique, making it a valuable tool in modern manufacturing and material science.
Summary Table:
Aspect | Details |
---|---|
Overview | Vaporizes material to deposit thin films on substrates in a vacuum chamber. |
Key Techniques | Thermal Evaporation, Electron Beam Evaporation, Sputter Deposition |
Applications | Insulation, conductivity, wear resistance, semiconductors, solar cells |
Advantages | High purity, precise control, wide material compatibility |
Considerations | High cost, specialized equipment, material limitations |
Discover how evaporative deposition can enhance your manufacturing process—contact us today for expert guidance!