Thin film deposition is a critical process in materials science and engineering, enabling the creation of layers of material ranging from a few nanometers to several micrometers in thickness. Among the various techniques, evaporation is a widely used physical vapor deposition (PVD) method. This technique involves heating a material in a vacuum until it vaporizes, then allowing the vapor to condense on a substrate, forming a thin film. Evaporation is particularly valued for its simplicity, ability to produce high-purity films, and compatibility with a wide range of materials. This method is commonly used in industries such as electronics, optics, and solar energy, where precise control over film thickness and composition is essential.
Key Points Explained:
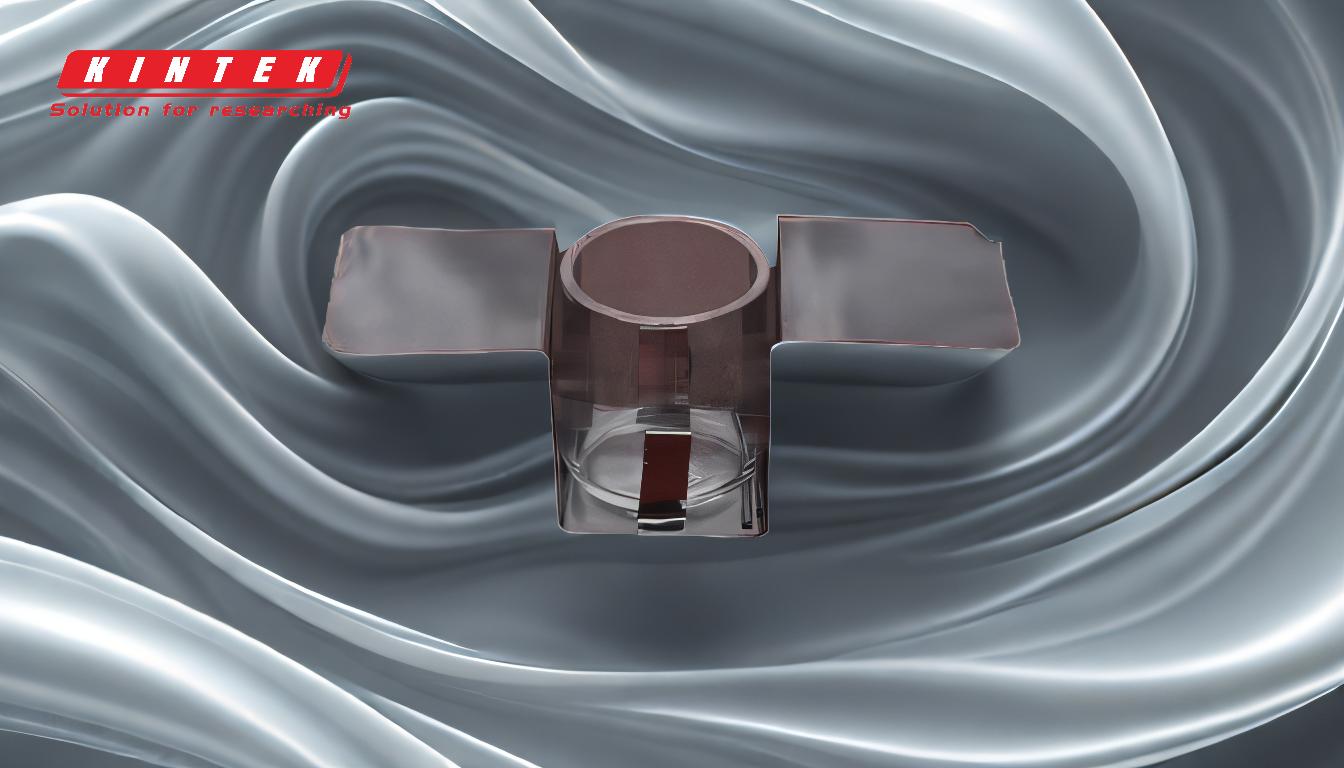
-
Overview of Thin Film Deposition:
- Thin film deposition techniques are broadly categorized into chemical and physical methods.
- Chemical methods include processes like chemical vapor deposition (CVD), sol-gel, and electroplating.
- Physical methods, such as sputtering and evaporation, rely on physical processes to deposit material onto a substrate.
-
Evaporation as a Physical Vapor Deposition (PVD) Technique:
- Evaporation is a PVD method where a material is heated in a vacuum until it vaporizes.
- The vaporized material then travels through the vacuum and condenses on a cooler substrate, forming a thin film.
- This technique is particularly useful for depositing metals, alloys, and some compounds.
-
Types of Evaporation Techniques:
- Thermal Evaporation: Involves heating the material using a resistive heater or an electron beam until it evaporates. This method is suitable for materials with relatively low melting points.
- Electron Beam Evaporation: Uses a focused electron beam to heat and vaporize the material. This method is ideal for materials with high melting points, as it provides localized heating and avoids contamination from the crucible.
- Molecular Beam Epitaxy (MBE): A more advanced form of evaporation used for growing high-quality crystalline films, often at the atomic level.
-
Advantages of Evaporation:
- High Purity: Since the process occurs in a vacuum, there is minimal contamination from impurities.
- Precision: Evaporation allows for precise control over film thickness, often down to the nanometer scale.
- Versatility: A wide range of materials, including metals, semiconductors, and insulators, can be deposited using this method.
-
Applications of Evaporation in Thin Film Deposition:
- Electronics: Used to deposit conductive layers in semiconductor devices and integrated circuits.
- Optics: Applied in the production of reflective coatings, anti-reflective coatings, and optical filters.
- Solar Energy: Utilized in the fabrication of thin-film solar cells, where precise control over film properties is crucial for efficiency.
-
Comparison with Other Deposition Techniques:
- Sputtering: Unlike evaporation, sputtering involves bombarding a target material with ions to eject atoms, which then deposit on the substrate. Sputtering is often preferred for materials that are difficult to evaporate or when better adhesion is required.
- Chemical Vapor Deposition (CVD): CVD involves chemical reactions to deposit films, often resulting in higher-quality films with better conformality over complex geometries. However, CVD typically requires higher temperatures and more complex equipment compared to evaporation.
-
Challenges and Considerations:
- Material Limitations: Not all materials are suitable for evaporation, especially those with very high melting points or those that decompose before vaporizing.
- Uniformity: Achieving uniform film thickness over large areas can be challenging, particularly for complex substrate geometries.
- Vacuum Requirements: The need for a high vacuum environment increases equipment costs and complexity.
In summary, evaporation is a versatile and widely used technique for depositing thin films, offering advantages in terms of purity, precision, and material compatibility. While it has some limitations, particularly with high-melting-point materials and large-area uniformity, it remains a cornerstone of thin film technology across various industries.
Summary Table:
Aspect | Details |
---|---|
Type | Physical Vapor Deposition (PVD) |
Process | Material is heated in a vacuum, vaporizes, and condenses on a substrate. |
Techniques | Thermal Evaporation, Electron Beam Evaporation, Molecular Beam Epitaxy (MBE) |
Advantages | High purity, precise thickness control, versatile material compatibility. |
Applications | Electronics, optics, solar energy. |
Challenges | Material limitations, uniformity issues, vacuum requirements. |
Discover how the evaporation technique can enhance your thin film processes—contact our experts today!