A rotary furnace, also known as a rotary kiln or tube furnace, is a versatile thermal equipment used for various industrial processes. Its primary function is to heat, mix, and process granular or powdery materials through continuous rotation and controlled heating. The furnace consists of a long, slightly inclined barrel that rotates around its central axis, ensuring uniform heat distribution and consistent material processing. Rotary furnaces are widely used for calcination, oxidation, roasting, drying, and thermal decomposition in industries such as cement production, metal recovery, and mineral processing. They are particularly effective for processes like extracting mercury from ores, recovering valuable metals, and treating lead-acid battery scrap.
Key Points Explained:
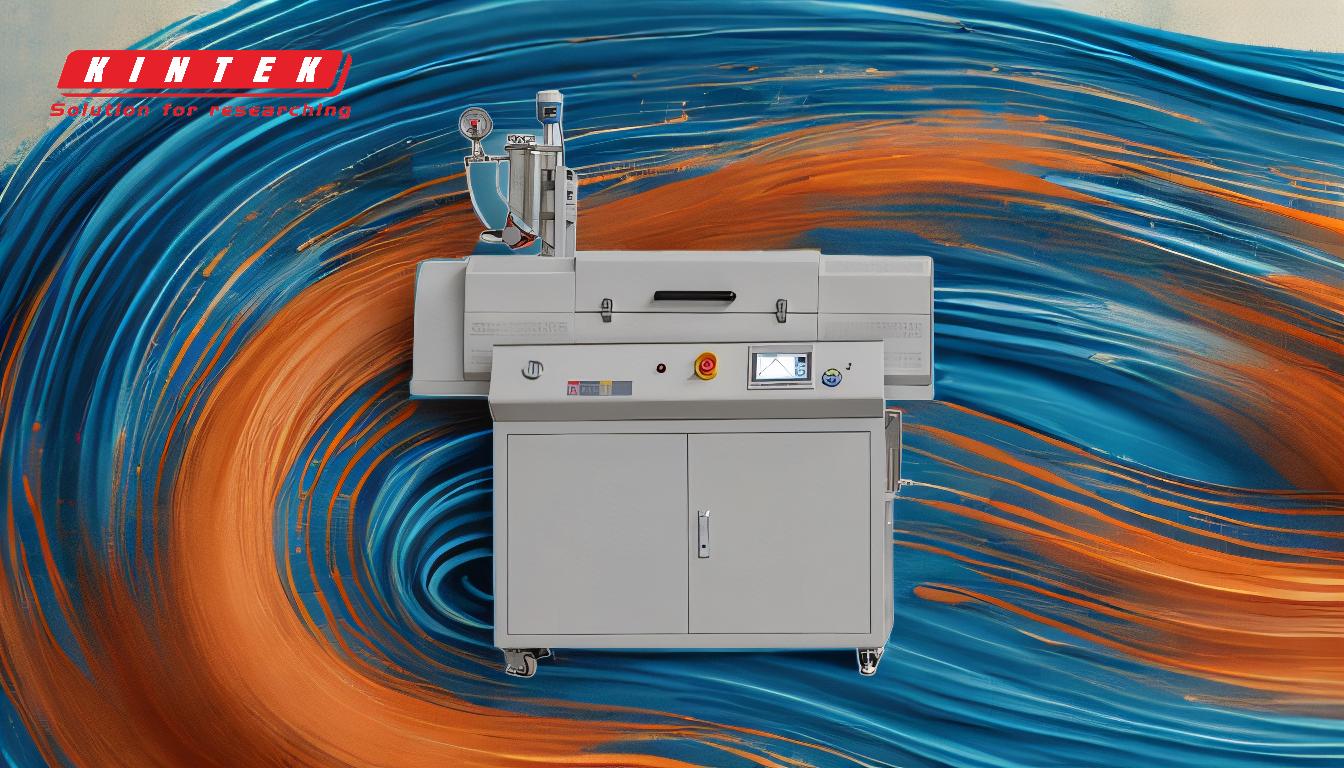
-
Primary Function of a Rotary Furnace:
- A rotary furnace is designed to heat and process materials continuously. It achieves this by rotating a long, cylindrical barrel around its central axis, ensuring uniform mixing and heating of the materials inside.
- The furnace is used for various thermal processes, including calcination, oxidation, roasting, and drying, making it a versatile tool in industrial applications.
-
Structure and Operation:
- The furnace consists of a long, slightly inclined barrel that rotates slowly. This rotation ensures that materials are evenly mixed and exposed to heat.
- Heat is typically supplied externally, often through electric heating elements, and the rotation ensures consistent radial temperature distribution.
-
Industrial Applications:
- Calcination: Rotary furnaces are commonly used in the production of Portland cement, where raw materials are heated to high temperatures to induce thermal decomposition.
- Metal Recovery: They are used to extract valuable metals, such as mercury from ores or lead from lead-acid battery scrap.
- Oxidation and Reduction: The furnace facilitates oxidation (reducing electrons in a sample) and reduction processes, such as converting lead sulphate or lead oxides into metallic lead.
-
Material Processing:
- The furnace is ideal for processing granular and powdery materials. The rotation ensures that materials are continuously mixed, preventing clumping and ensuring uniform heat exposure.
- This makes it suitable for drying, roasting, and other physicochemical processes.
-
Advantages of Rotary Furnaces:
- Uniform Heat Distribution: The rotating design ensures consistent heating, which is critical for processes like calcination and metal recovery.
- Continuous Processing: The furnace operates as a continuous plug flow reactor, allowing for efficient and uninterrupted material processing.
- Versatility: Its ability to handle a wide range of materials and processes makes it a valuable asset in industries such as mining, metallurgy, and cement production.
-
Specific Use Cases:
- Lead Recovery: Rotary furnaces are extensively used in the recycling industry to recover lead from lead-acid battery scrap and other lead-containing materials.
- Mineral Processing: They are employed in the extraction of metals like mercury and the thermal treatment of ores and concentrates.
- Cement Production: The calcination process in cement production relies heavily on rotary furnaces to heat raw materials to the required temperatures.
In summary, the rotary furnace is a critical piece of equipment in various industries, offering efficient and uniform heating for a wide range of materials and processes. Its rotating design and ability to handle continuous processing make it indispensable for applications such as calcination, metal recovery, and oxidation.
Summary Table:
Aspect | Details |
---|---|
Primary Function | Continuous heating and processing of granular/powdery materials. |
Structure | Long, inclined rotating barrel for uniform heat distribution. |
Key Applications | Calcination, oxidation, roasting, drying, metal recovery, and more. |
Industries Served | Cement production, metal recovery, mineral processing, and recycling. |
Advantages | Uniform heating, continuous processing, and versatility. |
Learn how a rotary furnace can optimize your industrial processes—contact our experts today!