The heat generated in a hydraulic system is primarily absorbed and managed through various cooling mechanisms and components designed to dissipate excess heat. These include heat exchangers, hydraulic oil coolers, and the hydraulic fluid itself, which acts as a heat transfer medium. Additionally, the system's design, such as the size of the reservoir and the flow rate of the fluid, plays a crucial role in heat dissipation. Proper maintenance, such as ensuring clean filters and adequate fluid levels, also helps in managing heat. Understanding these factors is essential for maintaining the efficiency and longevity of hydraulic systems.
Key Points Explained:
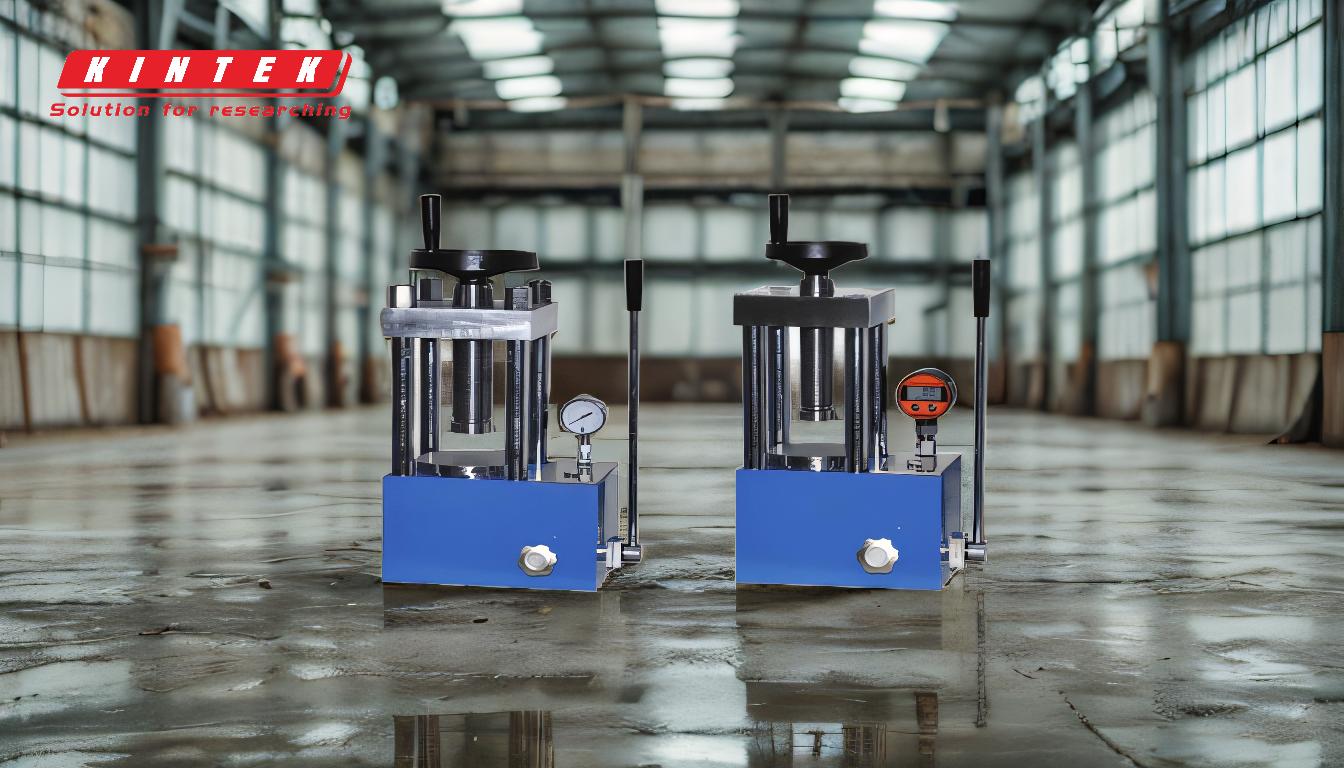
-
Hydraulic Fluid as a Heat Transfer Medium:
- Hydraulic fluid plays a dual role in the system: it transmits power and acts as a coolant. As the fluid circulates through the system, it absorbs heat generated by mechanical friction and fluid turbulence. The fluid then carries this heat to the reservoir or a heat exchanger, where it can be dissipated.
- The type of hydraulic fluid used can impact its heat absorption capacity. High-quality fluids with good thermal stability and viscosity are more effective in managing heat.
-
Heat Exchangers and Hydraulic Oil Coolers:
- Heat exchangers and hydraulic oil coolers are critical components in managing system temperature. They work by transferring heat from the hydraulic fluid to a cooling medium, such as air or water.
- Air-cooled heat exchangers use fans to blow air over fins or coils, while water-cooled systems use a separate water circuit to absorb and remove heat. The choice between air-cooled and water-cooled systems depends on the application and the operating environment.
- Proper sizing and placement of these coolers are essential to ensure they can handle the heat load generated by the system.
-
System Design and Reservoir Size:
- The design of the hydraulic system, including the size of the reservoir, plays a significant role in heat dissipation. A larger reservoir provides more surface area for heat to dissipate into the surrounding environment.
- The flow rate of the hydraulic fluid also affects heat management. A higher flow rate can help distribute heat more evenly and reduce localized hot spots within the system.
-
Maintenance and System Efficiency:
- Regular maintenance is crucial for effective heat management. Dirty or clogged filters can restrict fluid flow, leading to increased heat generation. Ensuring that filters are clean and fluid levels are adequate helps maintain optimal system performance.
- Monitoring system components, such as pumps and valves, for wear and tear can also prevent excessive heat generation. Worn components can cause inefficiencies that lead to increased friction and heat.
-
Environmental Factors:
- The operating environment can impact the heat management of a hydraulic system. Systems operating in high-temperature environments may require additional cooling measures, such as larger heat exchangers or more frequent maintenance.
- Conversely, systems operating in cooler environments may have an easier time dissipating heat, but it is still important to ensure that all components are functioning correctly to prevent overheating.
By understanding and addressing these key points, you can effectively manage the heat generated in a hydraulic system, ensuring its efficiency and longevity.
Summary Table:
Heat Absorption Mechanism | Key Details |
---|---|
Hydraulic Fluid | Acts as a coolant and heat transfer medium; absorbs heat from friction and turbulence. |
Heat Exchangers | Transfer heat from fluid to air or water; available in air-cooled and water-cooled types. |
Reservoir Size | Larger reservoirs provide more surface area for heat dissipation. |
Flow Rate | Higher flow rates distribute heat evenly and reduce hot spots. |
Maintenance | Clean filters and adequate fluid levels prevent overheating. |
Optimize your hydraulic system's heat management—contact our experts today for tailored solutions!