Vacuum brazing is a specialized heat treatment process used to join metal components without the use of flux, ensuring clean and oxidation-free joints. It involves heating the assembled components in a vacuum brazing furnace to a temperature above the melting point of the filler metal but below the melting point of the base metals. The vacuum environment prevents oxidation and contamination, resulting in high-quality, durable joints. The process is widely used in industries requiring precision and reliability, such as aerospace, automotive, and electronics.
Key Points Explained:
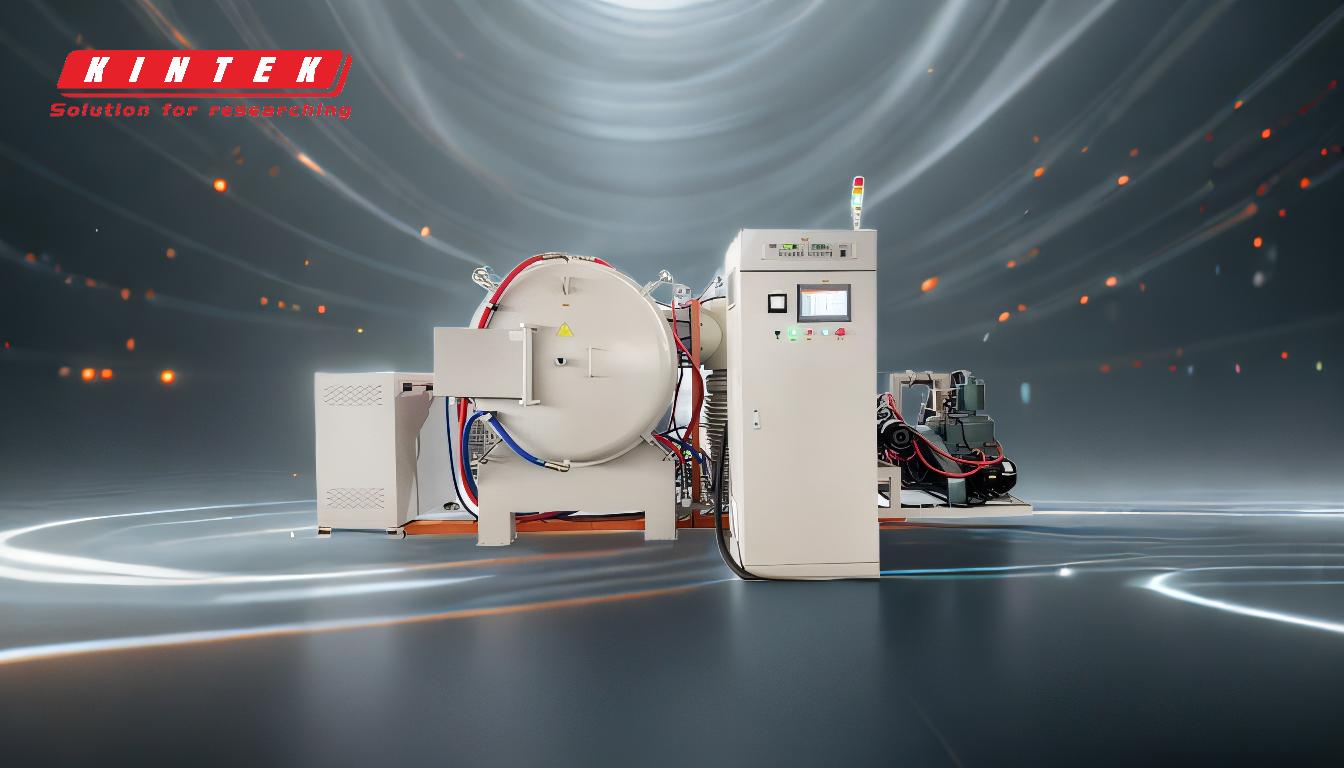
-
Vacuum Environment:
- A vacuum brazing furnace operates in a controlled vacuum environment, typically ranging from low to ultra-high vacuum levels (1.33 ~ 1.33 × 10^-3 Pa for medium-frequency vacuum heat treatment furnaces).
- The absence of oxygen prevents oxidation, ensuring that the metal surfaces remain clean and uncontaminated during the heating process.
-
Temperature Control:
- Advanced computer-controlled systems in vacuum furnaces ensure precise temperature control, which is critical for achieving consistent and accurate heating.
- This precision is essential for maintaining the integrity of the base metals while allowing the filler metal to melt and flow properly.
-
Preparation Before Brazing:
- Proper preparation of the metal components is crucial. This includes cleaning the surfaces to remove any contaminants that could interfere with the brazing process.
- The components are then assembled and filled with the appropriate filler metal, which is chosen based on the specific requirements of the materials being joined.
-
Brazing Process:
- The assembled components are placed in the vacuum furnace and heated to the required temperature. The filler metal melts and flows into the joint, creating a strong bond between the base metals.
- The vacuum environment ensures that the filler metal flows evenly and forms a clean, oxidation-free joint.
-
Inspection After Brazing:
- After the brazing process, the joints are inspected to ensure they meet the required standards of quality and durability.
- This inspection may include visual checks, non-destructive testing, and mechanical testing to verify the integrity of the brazed joint.
-
Applications and Advantages:
- Vacuum brazing is used in industries where high precision and reliability are essential, such as aerospace, automotive, and electronics.
- The process offers several advantages, including the ability to join dissimilar metals, produce clean and oxidation-free joints, and achieve high-strength bonds without the need for flux.
By following these steps and utilizing the controlled environment of a vacuum brazing furnace, manufacturers can achieve high-quality, durable joints that meet the stringent requirements of modern industries.
Summary Table:
Key Aspect | Details |
---|---|
Vacuum Environment | Operates in low to ultra-high vacuum (1.33 ~ 1.33 × 10^-3 Pa) to prevent oxidation. |
Temperature Control | Advanced computer-controlled systems ensure precise and consistent heating. |
Preparation | Clean surfaces and assemble components with appropriate filler metal. |
Brazing Process | Heat components in a vacuum furnace to melt filler metal and form strong joints. |
Inspection | Inspect joints for quality and durability using visual and mechanical tests. |
Applications | Aerospace, automotive, and electronics industries. |
Advantages | Clean, oxidation-free joints; ability to join dissimilar metals; no flux required. |
Discover how vacuum brazing can enhance your manufacturing process—contact our experts today!