A muffle furnace is a specialized heating device designed to achieve high temperatures in a controlled and isolated environment. Its heating mechanism primarily relies on electrical resistance, where electric current passes through heating elements, generating heat through Joule heating. This heat is then transferred to the chamber via conduction, convection, and radiation. The chamber, made of refractory materials, ensures minimal heat loss and maintains a consistent temperature. A PID controller and thermocouple regulate and monitor the temperature, making it suitable for precise applications like ashing, heat treatment, and material testing. The furnace's design separates the sample from combustion byproducts, ensuring clean and accurate heating.
Key Points Explained:
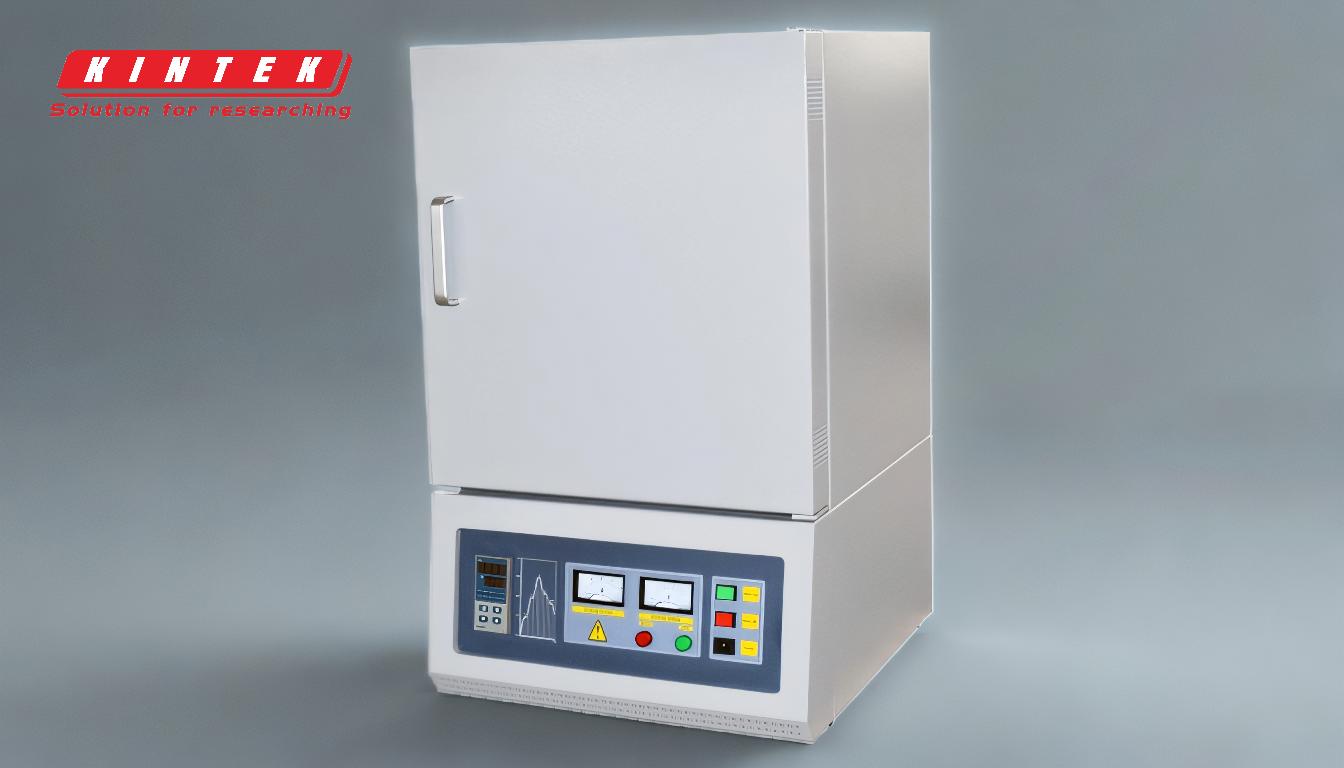
-
Heating Mechanism: Electrical Resistance (Joule Heating)
- The primary heating mechanism in a muffle furnace is electrical resistance. When an electric current passes through heating elements (typically made of materials like Nichrome), it encounters resistance, generating heat. This phenomenon is known as Joule heating.
- The heat generated is proportional to the square of the current and the resistance of the heating elements. This ensures efficient energy conversion from electrical to thermal energy.
-
Heat Transfer Methods
- Conduction: Heat is transferred from the heating elements to the walls of the muffle chamber through direct contact.
- Convection: The heated air inside the chamber circulates, distributing heat evenly across the sample.
- Radiation: The heated walls of the chamber emit infrared radiation, which directly heats the sample placed inside.
- These combined methods ensure uniform and efficient heating of the sample.
-
Insulation and Chamber Design
- The muffle chamber is constructed from refractory materials such as ceramic fiber or refractory bricks. These materials have high thermal resistance, minimizing heat loss and maintaining high temperatures within the chamber.
- The chamber is designed to isolate the sample from external factors and combustion byproducts, ensuring a clean and controlled environment for heating.
-
Temperature Regulation
- A PID (Proportional-Integral-Derivative) controller is used to regulate the temperature. It adjusts the power supplied to the heating elements based on feedback from a thermocouple, ensuring precise temperature control.
- The thermocouple measures the temperature inside the chamber and sends this data to the controller, which adjusts the current flow to maintain the desired temperature.
-
Applications and Advantages
- Muffle furnaces are used in various applications, including ashing, heat treatment, material testing, and research.
- The design ensures rapid heating, recovery, and cooling, making it energy-efficient and suitable for high-temperature processes.
- The separation of the sample from combustion byproducts ensures clean and accurate results, making it ideal for analytical and industrial purposes.
-
Modern Features
- Modern muffle furnaces often include advanced features such as digital displays, programmable temperature profiles, and safety mechanisms like over-temperature protection.
- These features enhance usability, precision, and safety, making muffle furnaces indispensable in laboratories and industrial settings.
By understanding these key points, a purchaser can evaluate the suitability of a muffle furnace for their specific needs, ensuring optimal performance and efficiency in their heating processes.
Summary Table:
Aspect | Details |
---|---|
Heating Mechanism | Electrical resistance (Joule heating) using materials like Nichrome. |
Heat Transfer | Conduction, convection, and radiation for uniform heating. |
Chamber Design | Made of refractory materials (e.g., ceramic fiber) for minimal heat loss. |
Temperature Control | PID controller and thermocouple for precise regulation. |
Applications | Ashing, heat treatment, material testing, and research. |
Modern Features | Digital displays, programmable profiles, and over-temperature protection. |
Upgrade your lab with a high-performance muffle furnace—contact us today to learn more!