A tube furnace is a versatile and efficient heating device widely used in industries such as metallurgy, glass, heat treatment, and new energy. Its high-temperature capabilities vary depending on the type and design, with standard tube furnaces reaching up to 1800°C and specialized graphite tube furnaces capable of achieving temperatures as high as 3000°C. The furnace's structure typically includes a cylindrical cavity surrounded by heating coils embedded in a thermally insulating matrix, with temperature control managed through feedback from a thermocouple. It is crucial to operate the tube furnace within its rated temperature limits to avoid overheating or overloading, ensuring safe and efficient performance.
Key Points Explained:
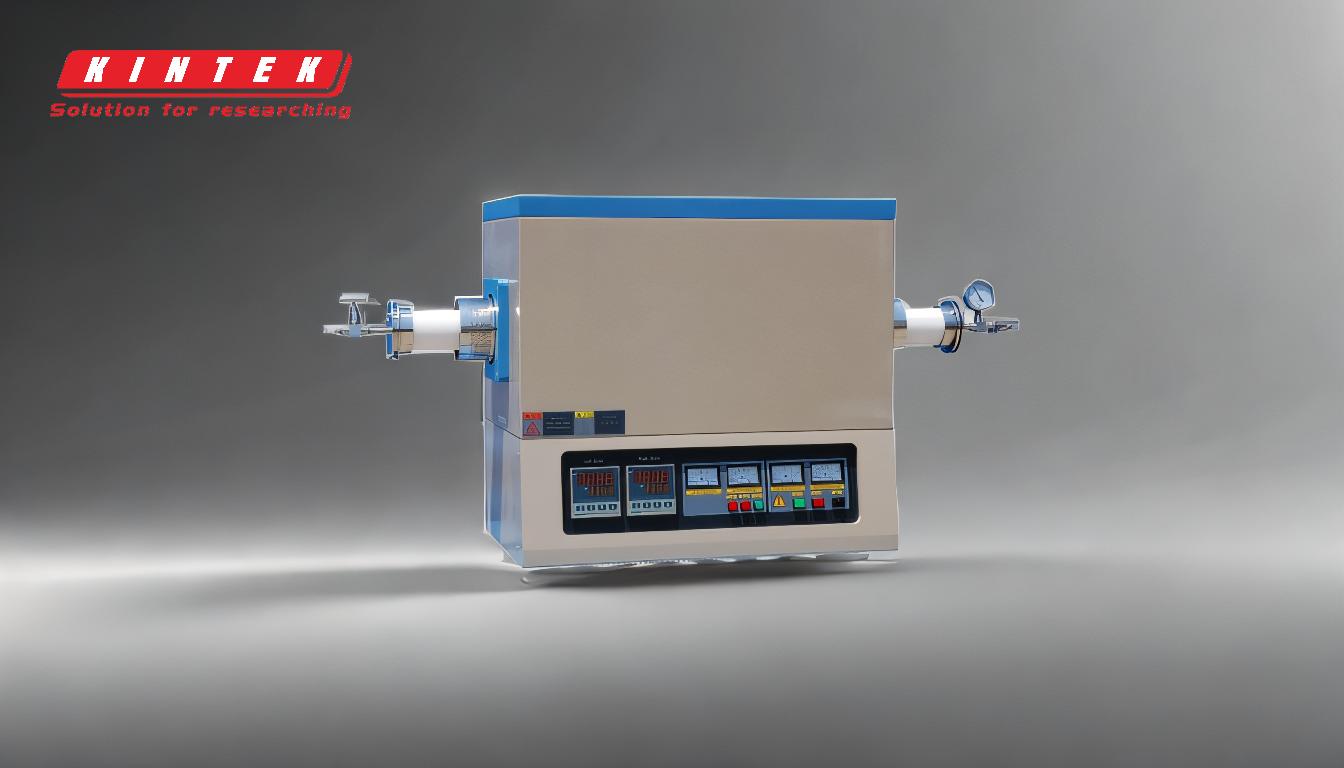
-
High-Temperature Range of Tube Furnaces:
- Standard tube furnaces can reach temperatures up to 1800°C, making them suitable for a wide range of industrial applications.
- Specialized graphite tube furnaces can achieve even higher temperatures, up to 3000°C, which are ideal for extreme heat treatment processes.
- Some tube furnaces are capable of maintaining high temperatures (up to 1600°C) even in challenging environments, such as a pure hydrogen atmosphere.
-
Structure and Design:
- A tube furnace typically consists of a cylindrical cavity surrounded by heating coils embedded in a thermally insulating matrix.
- The furnace may include a working tube or vessel where materials are exposed to varying temperatures for specific durations.
- Heating elements surround the tube, and a thermocouple is often incorporated to provide precise temperature control through feedback mechanisms.
-
Operational Guidelines:
- Tube furnaces must be operated within their rated temperature limits to prevent overheating or overloading, which can damage the equipment or compromise safety.
- Proper usage ensures high thermal efficiency, continuous production, and easy operation, making tube furnaces a reliable choice for industrial applications.
-
Applications:
- Tube furnaces are widely used in industries such as metallurgy, glass manufacturing, heat treatment, and new energy.
- Their ability to provide consistent and high temperatures makes them suitable for processes like material synthesis, annealing, and sintering.
-
Sample Handling:
- Samples are typically placed inside the tube using ceramic or metal boats and are manipulated with a long push rod.
- The tube's dimensions usually range from 50 cm to 100 cm in length and 25 mm to 100 mm in diameter, accommodating various sample sizes.
For more detailed information about tube furnaces, you can visit: tube furnace.
Summary Table:
Feature | Details |
---|---|
Standard Tube Furnace | Up to 1800°C, suitable for general industrial applications. |
Graphite Tube Furnace | Up to 3000°C, ideal for extreme heat treatment processes. |
Hydrogen Atmosphere | Maintains up to 1600°C in challenging environments like pure hydrogen. |
Applications | Metallurgy, glass manufacturing, heat treatment, and new energy industries. |
Sample Handling | Uses ceramic/metal boats and push rods; tube dimensions: 50-100 cm length, 25-100 mm diameter. |
Unlock the full potential of tube furnaces for your industrial needs—contact us today for expert guidance!