Industrial furnaces are designed to reach extremely high temperatures, and the maximum temperature they can achieve depends on the type of furnace and its construction materials. The highest temperature industrial furnaces can exceed 3000°C, with some specialized designs capable of reaching even higher temperatures. These furnaces are used in advanced manufacturing, research, and material processing applications. Key factors influencing the maximum temperature include the heating elements, insulation, and the furnace's ability to withstand thermal stress. Among the most advanced high-temperature furnaces are those utilizing advanced technologies like the igbt furnace, which offer precise temperature control and energy efficiency.
Key Points Explained:
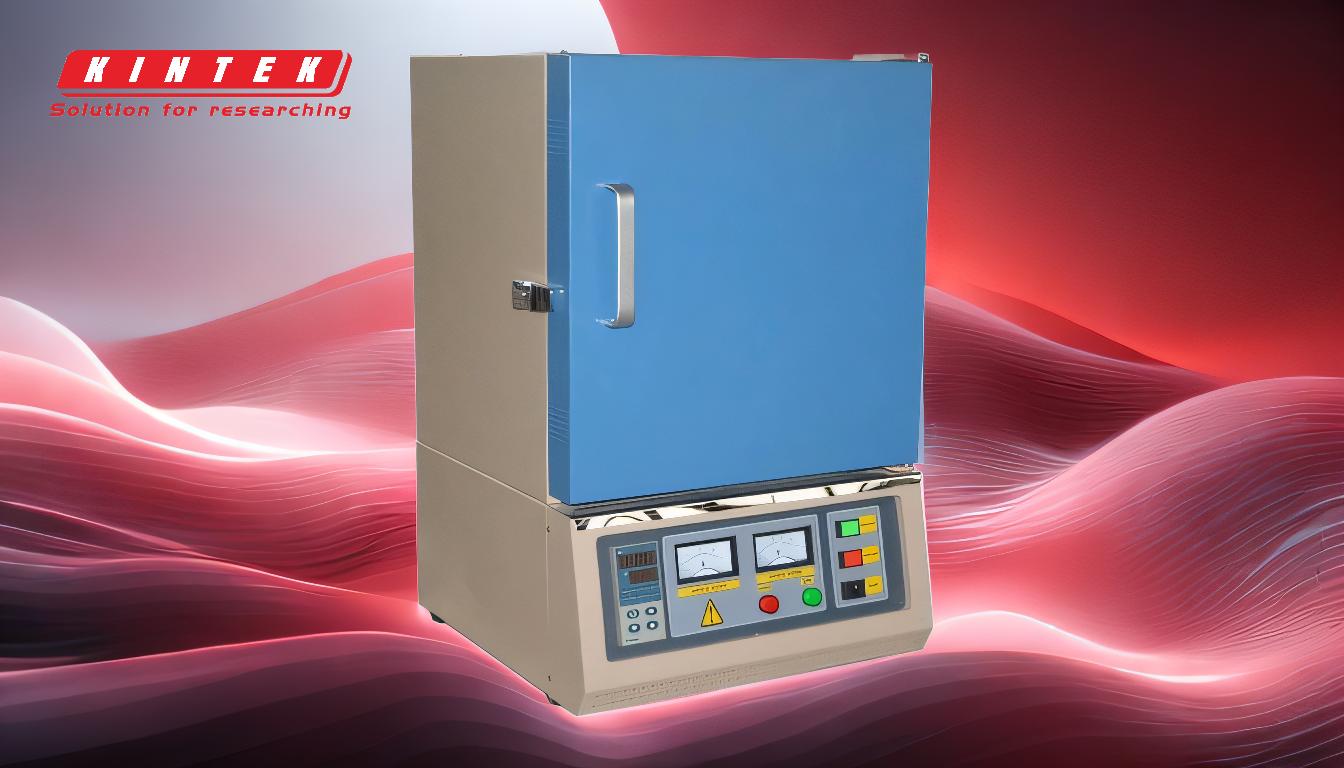
-
Types of High-Temperature Industrial Furnaces:
- Industrial furnaces are categorized based on their maximum operating temperatures. Some common types include:
- Muffle Furnaces: Typically used for processes requiring temperatures up to 1800°C, such as heat treatment and material testing.
- Induction Furnaces: These can reach temperatures up to 3000°C and are used for melting metals and alloys.
- Arc Furnaces: Capable of exceeding 3000°C, these are used in steelmaking and other high-temperature applications.
- Vacuum Furnaces: Designed for high-temperature processes in a controlled atmosphere, they can reach up to 3000°C or more.
- Industrial furnaces are categorized based on their maximum operating temperatures. Some common types include:
-
Factors Determining Maximum Temperature:
- Heating Elements: Materials like tungsten, molybdenum, and graphite are used in high-temperature furnaces due to their ability to withstand extreme heat.
- Insulation: High-quality insulation materials, such as ceramic fibers and refractory bricks, are essential to maintain high temperatures and reduce heat loss.
- Thermal Stress Resistance: The furnace design must account for thermal expansion and contraction to prevent structural failure at high temperatures.
-
Advanced Technologies in High-Temperature Furnaces:
- The igbt furnace is a notable example of advanced furnace technology. It uses Insulated Gate Bipolar Transistors (IGBTs) for precise temperature control and energy efficiency. These furnaces are particularly useful in applications requiring consistent high temperatures, such as semiconductor manufacturing and advanced material synthesis.
-
Applications of High-Temperature Industrial Furnaces:
- Material Processing: High-temperature furnaces are used for sintering, melting, and heat treatment of advanced materials like ceramics, composites, and superalloys.
- Research and Development: Laboratories use these furnaces for experiments requiring extreme temperatures, such as studying material properties under high heat.
- Industrial Manufacturing: Industries like aerospace, automotive, and electronics rely on high-temperature furnaces for producing high-performance components.
-
Challenges in Operating High-Temperature Furnaces:
- Energy Consumption: Achieving and maintaining extremely high temperatures requires significant energy input, making energy efficiency a critical consideration.
- Material Degradation: Prolonged exposure to high temperatures can cause wear and tear on furnace components, necessitating regular maintenance and replacement.
- Safety Concerns: High-temperature operations pose risks such as thermal burns and equipment failure, requiring robust safety protocols.
In summary, the highest temperature industrial furnaces can exceed 3000°C, with advanced designs like the igbt furnace offering precise control and efficiency. These furnaces are essential for high-temperature applications in manufacturing, research, and material processing, but they also present challenges related to energy use, material durability, and safety.
Summary Table:
Aspect | Details |
---|---|
Maximum Temperature | Exceeds 3000°C, with some designs reaching even higher temperatures. |
Types of Furnaces | Muffle (up to 1800°C), Induction (up to 3000°C), Arc (exceeds 3000°C), Vacuum (up to 3000°C+). |
Key Factors | Heating elements, insulation, and thermal stress resistance. |
Advanced Technologies | IGBT furnaces for precise control and energy efficiency. |
Applications | Material processing, R&D, aerospace, automotive, and electronics. |
Challenges | High energy consumption, material degradation, and safety concerns. |
Unlock the potential of high-temperature industrial furnaces—contact our experts today to find the best solution for your needs!