Pyrolysis technology has a rich history rooted in the chemical industry, where it has been used to produce essential substances like methanol, activated carbon, and charcoal from wood. Over time, the focus of pyrolysis has expanded to address modern challenges such as CO2 mitigation, electricity generation from biomass, and energy independence. These goals have driven advancements in pyrolysis processes, including improvements in reactor design, feedstock preparation, and safety standards. Today, pyrolysis plants are sophisticated systems that involve multiple stages, from biomass pretreatment to the separation of biochar, bio-oil, and syn gases. The evolution of pyrolysis technology reflects its adaptability and importance in addressing both historical and contemporary industrial and environmental needs.
Key Points Explained:
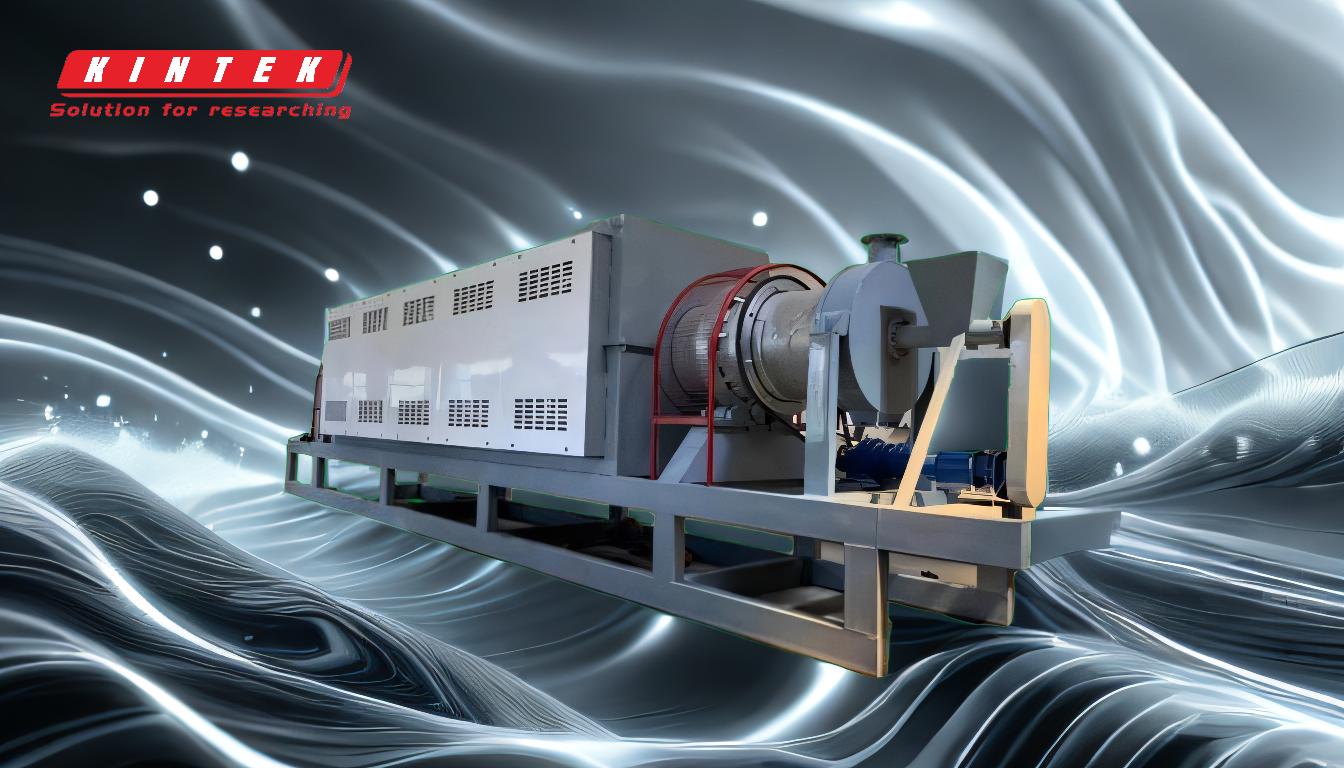
-
Origins of Pyrolysis in the Chemical Industry
- Pyrolysis has been a fundamental process in the chemical industry for centuries, primarily used to convert wood into valuable products like methanol, activated carbon, and charcoal.
- This early application laid the groundwork for understanding the thermal decomposition of organic materials in the absence of oxygen, which is the core principle of pyrolysis.
-
Modern Applications and Goals
- Today, pyrolysis technology is driven by three main interests:
- CO2 Mitigation: Pyrolysis helps reduce carbon emissions by converting biomass into stable carbon forms like biochar.
- Electricity Generation: Biomass pyrolysis produces bio-oil and syn gases, which can be used as renewable energy sources.
- Energy Independence: By utilizing locally available biomass, pyrolysis reduces reliance on fossil fuels and enhances energy security.
- These goals have spurred innovations in pyrolysis processes and reactor designs, making them more efficient and environmentally friendly.
- Today, pyrolysis technology is driven by three main interests:
-
Industrial Pyrolysis Process
- The modern pyrolysis process involves several key steps:
- Feed Preparation: Biomass is collected, dried, and sized to ensure optimal processing.
- Pretreatment: The biomass may undergo treatments like torrefaction to improve its pyrolysis efficiency.
- Pyrolysis Reactor: The biomass is fed into a reactor with low oxygen levels, where it decomposes under high temperatures.
- Combustion Chamber: Heat is supplied to the reactor, often using a portion of the syn gases produced during pyrolysis.
- Separation: The decomposed material is separated into biochar, bio-oil, and syn gases using equipment like cyclotrons and quenchers.
- This multi-stage process ensures maximum yield and quality of the end products.
- The modern pyrolysis process involves several key steps:
-
Advancements in Pyrolysis Plant Technology
- Continuous improvements in pyrolysis plant design and operation have enhanced safety and efficiency.
- Modern pyrolysis plants incorporate advanced monitoring systems, automated controls, and robust safety protocols to minimize risks.
- Industry best practices focus on optimizing feedstock utilization, reducing energy consumption, and ensuring compliance with environmental regulations.
- These advancements have made pyrolysis plants more reliable and scalable, enabling their use in diverse applications, from small-scale rural energy solutions to large-scale industrial operations.
-
Future Prospects of Pyrolysis Technology
- The future of pyrolysis technology lies in further optimizing processes to increase yield, reduce costs, and enhance sustainability.
- Research is ongoing to develop catalysts that improve the quality of bio-oil and syn gases, making them more viable for commercial use.
- Integration with other renewable energy systems, such as solar and wind, could enhance the overall efficiency and versatility of pyrolysis plants.
- As global demand for sustainable energy solutions grows, pyrolysis technology is poised to play a critical role in the transition to a low-carbon economy.
By understanding the history and evolution of pyrolysis technology, we can appreciate its significance in addressing both historical industrial needs and modern environmental challenges. The development of pyrolysis plants continues to be a dynamic field, driven by innovation and a commitment to sustainability. For more information on pyrolysis plants, visit pyrolysis plant.
Summary Table:
Key Aspect | Details |
---|---|
Origins | Used to produce methanol, activated carbon, and charcoal from wood. |
Modern Goals | CO2 mitigation, electricity generation, and energy independence. |
Process Steps | Feed preparation, pretreatment, pyrolysis reactor, combustion, separation. |
Advancements | Improved reactor design, safety standards, and automated controls. |
Future Prospects | Catalysts for better bio-oil, integration with renewable energy systems. |
Discover how pyrolysis technology can transform your energy solutions—contact us today!