The holding time for sintering, which refers to the duration the material is kept at the sintering temperature, varies significantly depending on the material, desired properties, and specific sintering process. Generally, sintering can take anywhere from seconds to several hours, with typical industrial processes often ranging between 15 to 20 hours. The exact holding time is influenced by factors such as temperature, pressure, particle size, composition, and the type of furnace used. Understanding these variables is crucial for optimizing the sintering process to achieve the desired material properties, such as density, strength, and porosity.
Key Points Explained:
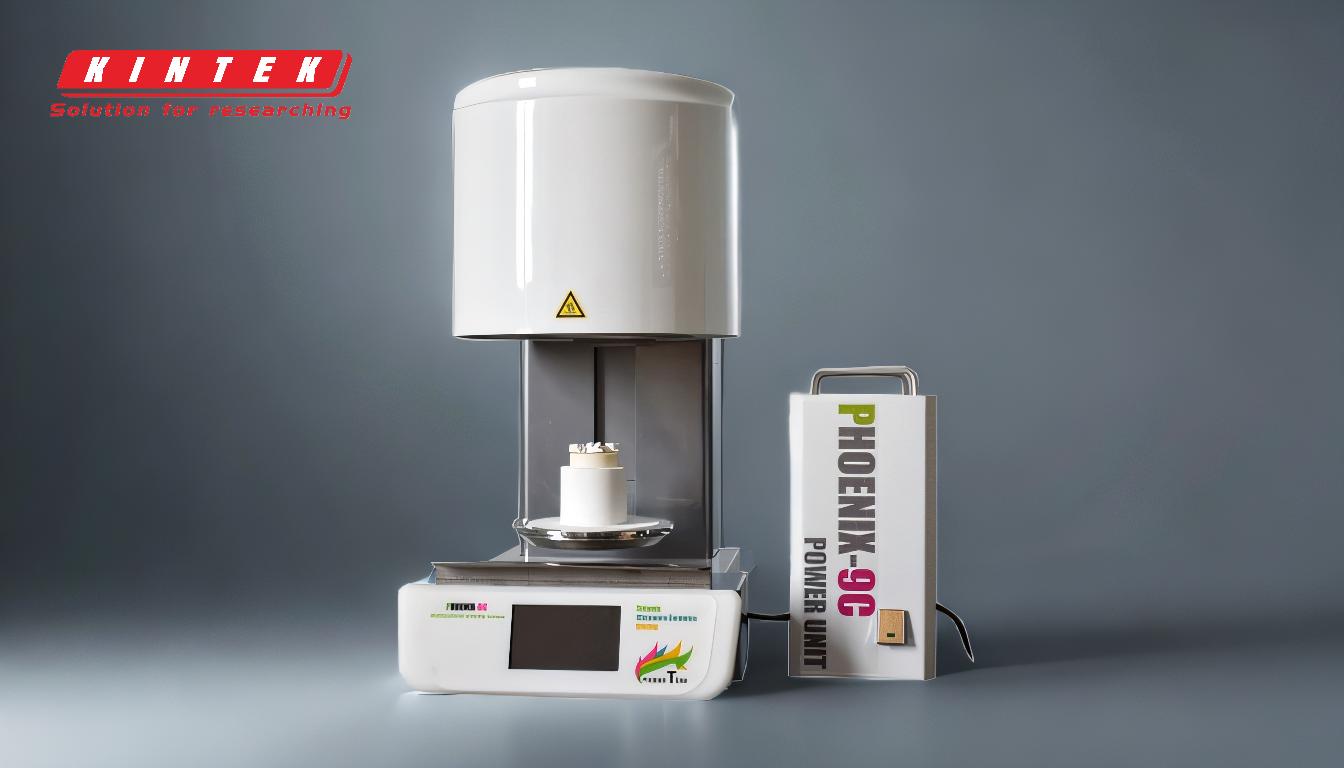
-
Definition of Holding Time in Sintering:
- The holding time is the period during which the material is maintained at the sintering temperature to allow for densification and bonding of particles. This phase is critical for achieving the desired mechanical and physical properties of the sintered product.
-
Typical Duration of Sintering:
- Sintering can range from seconds to several hours. For example:
- Short-duration sintering: Some processes, particularly those involving fine powders or high temperatures, can complete in seconds.
- Long-duration sintering: Industrial processes, especially those requiring high-density parts, often take between 15 to 20 hours.
- Sintering can range from seconds to several hours. For example:
-
Factors Influencing Holding Time:
- Temperature: Higher temperatures can reduce the required holding time by accelerating sintering kinetics. However, excessively high temperatures may lead to undesirable grain growth or material degradation.
- Pressure: Applied pressure can enhance particle rearrangement and reduce porosity, potentially shortening the holding time.
- Particle Size: Smaller particles have a higher surface area-to-volume ratio, promoting faster densification and potentially reducing the holding time.
- Composition: Homogeneous compositions with uniform particle distribution tend to sinter more efficiently, influencing the optimal holding time.
- Atmosphere: The sintering environment (e.g., air, vacuum, or inert gases) can affect oxidation or contamination, indirectly impacting the holding time.
-
Sintering Techniques and Their Impact on Holding Time:
- Conventional Sintering: Typically involves longer holding times (15-20 hours) to achieve high-density parts.
- Spark Plasma Sintering (SPS): Uses electrical currents to rapidly heat the material, significantly reducing the holding time to minutes or even seconds.
- Hot Pressing: Combines heat and pressure, often resulting in shorter holding times compared to conventional sintering.
-
Material-Specific Considerations:
- Different materials require varying holding times based on their thermal and mechanical properties. For instance:
- Ceramics: Often require longer holding times due to their high melting points and low diffusion rates.
- Metals: May sinter faster, especially when using fine powders or high pressures.
- Composites: The holding time must balance the sintering behavior of each component to avoid delamination or uneven densification.
- Different materials require varying holding times based on their thermal and mechanical properties. For instance:
-
Furnace Type and Its Role:
- The type of furnace used (e.g., belt conveyor, push, or batch furnace) can influence the holding time. For example:
- Belt Conveyor Furnaces: Suitable for continuous processes with shorter holding times.
- Batch Furnaces: Allow for precise control over temperature and atmosphere, often used for longer holding times in high-precision applications.
- The type of furnace used (e.g., belt conveyor, push, or batch furnace) can influence the holding time. For example:
-
Optimizing Holding Time:
- The optimal holding time is determined by balancing the desired material properties (e.g., density, strength) with process efficiency. Over-sintering can lead to excessive grain growth, while under-sintering may result in insufficient densification.
-
Practical Implications for Equipment and Consumable Purchasers:
- Understanding the holding time is essential for selecting the appropriate sintering equipment and consumables. For instance:
- Furnace Selection: Choose a furnace that can maintain the required temperature and atmosphere for the specified holding time.
- Material Selection: Ensure the material's sintering behavior aligns with the chosen process parameters.
- Cost Considerations: Longer holding times may increase energy consumption and operational costs, so optimizing the process is crucial for cost-effectiveness.
- Understanding the holding time is essential for selecting the appropriate sintering equipment and consumables. For instance:
By carefully considering these factors, purchasers and engineers can optimize the sintering process to achieve high-quality products efficiently.
Summary Table:
Factor | Impact on Holding Time |
---|---|
Temperature | Higher temps reduce time; excessive heat may cause grain growth or degradation. |
Pressure | Applied pressure shortens time by enhancing particle rearrangement. |
Particle Size | Smaller particles reduce time due to higher surface area-to-volume ratio. |
Composition | Homogeneous compositions sinter more efficiently, influencing optimal time. |
Atmosphere | Sintering environment (air, vacuum, inert gases) affects oxidation and contamination. |
Sintering Technique | Conventional: 15-20 hrs; SPS: minutes/seconds; Hot Pressing: shorter than conventional. |
Material Type | Ceramics: longer; Metals: faster; Composites: balanced sintering behavior required. |
Furnace Type | Belt conveyor: shorter times; Batch: precise control, longer times for high precision. |
Optimize your sintering process today—contact our experts for tailored solutions!