Calcination is a thermal treatment process widely used in various industrial applications. It involves heating materials to high temperatures in the absence or limited supply of air or oxygen to bring about thermal decomposition, phase transitions, or removal of volatile substances. Key industrial applications include cement production, synthesis of zeolites, devitrification of glass, and removal of water or volatile components from materials. These processes are essential in industries such as construction, chemical manufacturing, and materials science, where precise thermal treatment is required to achieve desired material properties or chemical compositions.
Key Points Explained:
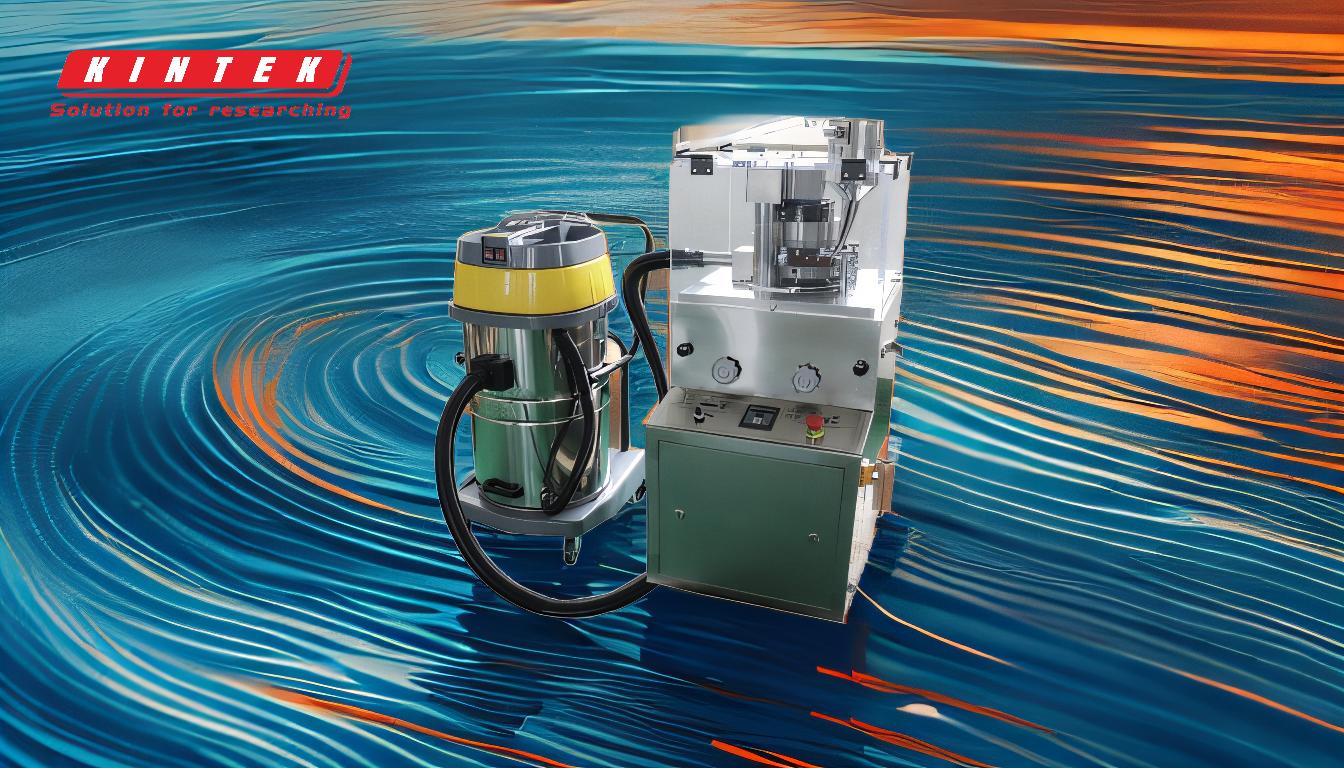
-
Cement Production:
- Calcination is a critical step in cement manufacturing. It involves heating limestone (calcium carbonate) to high temperatures (around 900–1000°C) in a calcination furnace.
- During this process, calcium carbonate decomposes into calcium oxide (quicklime) and carbon dioxide.
- The calcium oxide is a key ingredient in cement, reacting with other materials to form clinker, which is then ground into cement powder.
- This application is the most common and economically significant use of calcination furnaces.
-
Synthesis of Zeolites:
- Zeolites are microporous, aluminosilicate minerals used as catalysts, adsorbents, and ion-exchange materials in chemical processes.
- Calcination is used to remove ammonium ions from the zeolite structure, which is essential for activating the material for industrial use.
- The process ensures the stability and functionality of zeolites in applications such as water purification, gas separation, and petrochemical refining.
-
Devitrification of Glass:
- Devitrification refers to the process of converting glass from an amorphous (non-crystalline) state to a crystalline state.
- Calcination furnaces are used to control phase transformations in glass, enhancing its mechanical and thermal properties.
- This process is crucial in manufacturing specialty glass products, such as those used in optics, electronics, and high-temperature applications.
-
Removal of Water and Volatile Components:
- Calcination is used to remove water (dehydration) or volatile components (e.g., carbon dioxide, sulfur dioxide) from materials.
- This is important in industries like ceramics, where removing water and organic impurities ensures the material's structural integrity and performance.
- It is also used in the production of metal oxides, where volatile impurities must be eliminated to achieve high-purity products.
-
Oxidation and Thermal Decomposition:
- In some industrial processes, calcination is used to oxidize part or all of a substance, altering its chemical composition.
- For example, in the production of titanium dioxide (a white pigment), calcination is used to oxidize titanium compounds to achieve the desired product.
- This process is also applied in the extraction of metals from ores, where thermal decomposition separates the metal from other components.
-
Environmental and Energy Considerations:
- Calcination furnaces must be designed to handle high temperatures efficiently, often requiring energy-intensive operations.
- Modern calcination processes focus on optimizing energy use and reducing carbon emissions, especially in cement production, where the release of carbon dioxide is a significant environmental concern.
- Innovations in furnace design and alternative fuels are being explored to make calcination more sustainable.
In summary, calcination is a versatile and essential process in various industries, enabling the production of critical materials like cement, zeolites, and specialty glass, as well as the purification and transformation of raw materials. Its applications are broad, ranging from construction to advanced materials science, highlighting its importance in industrial processes.
Summary Table:
Application | Key Process | Industry Impact |
---|---|---|
Cement Production | Heating limestone to produce calcium oxide (quicklime) | Essential for cement manufacturing, a cornerstone of construction |
Synthesis of Zeolites | Removing ammonium ions to activate zeolites | Critical for water purification, gas separation, and petrochemical refining |
Devitrification of Glass | Converting amorphous glass to crystalline state | Enhances mechanical and thermal properties for optics and electronics |
Removal of Volatile Components | Dehydration or elimination of impurities | Ensures material integrity in ceramics and metal oxide production |
Oxidation and Decomposition | Altering chemical composition through thermal treatment | Used in titanium dioxide production and metal extraction |
Environmental Considerations | Optimizing energy use and reducing emissions | Focus on sustainability in high-temperature industrial processes |
Learn how calcination can optimize your industrial processes—contact our experts today!