PVD (Physical Vapor Deposition) coatings are renowned for their durability, resistance to corrosion, scratches, and wear, making them highly suitable for a wide range of industrial applications. These coatings are extremely thin yet strong, providing enhanced hardness, wear resistance, and reduced friction, which contribute to the extended lifespan of components. Despite their robustness, PVD coatings can be susceptible to color damage under aggressive conditions, and such damage may not always be repairable. Overall, PVD coatings are valued for their purity, durability, and performance-enhancing properties, making them ideal for use in industries such as electronics, optics, solar energy, and medical devices.
Key Points Explained:
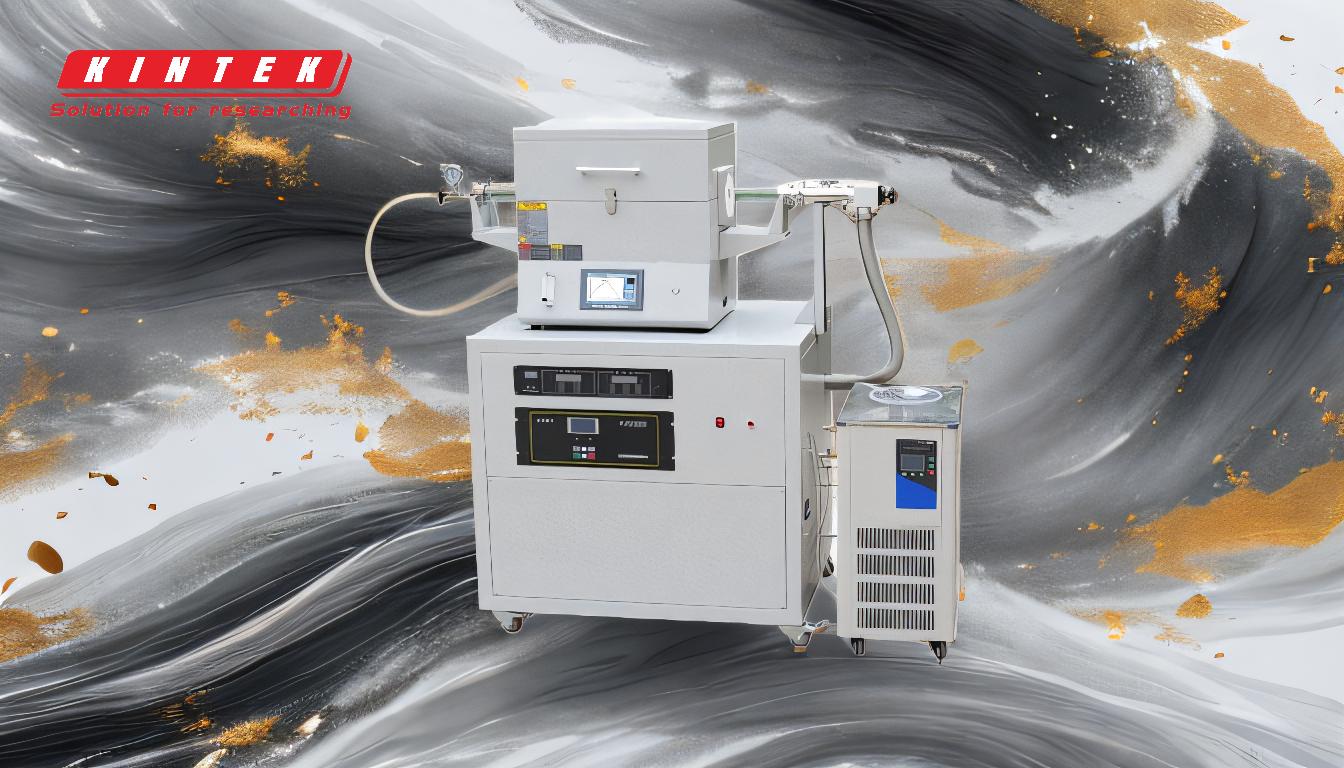
-
Durability and Resistance Properties:
- PVD coatings are highly durable and resistant to corrosion, scratches, and wear and tear. This makes them ideal for applications where components are exposed to harsh environments or mechanical stress.
- The coatings are designed to withstand high levels of temperature and abrasion, often eliminating the need for additional protective layers or top coatings.
-
Enhanced Performance and Longevity:
- PVD coatings improve the hardness and wear resistance of components, which enhances their overall performance and extends their operational life.
- By reducing friction and improving oxidation resistance, these coatings allow components to operate efficiently in environments where uncoated parts would fail.
-
Thinness and Strength:
- Despite being extremely thin, PVD coatings are strong and corrosion-resistant. This thinness allows the coated product to retain its original shape while providing a rich finish and color.
- The combination of thinness and strength makes PVD coatings suitable for applications requiring precise dimensions and high durability.
-
Limitations and Potential Damage:
- While PVD coatings are wear and weather resistant, they can be susceptible to color damage if aggressively attacked. In some cases, this damage may not be repairable, which is an important consideration for applications where aesthetics are crucial.
-
Applications Across Industries:
- PVD coatings are used in a variety of industries, including microchips, semiconductor devices, optical lenses, solar panels, and medical devices.
- These coatings provide crucial performance attributes such as thinness, purity, durability, and cleanliness, making them preferable for many high-performance applications.
In summary, the life of PVD coatings is significantly extended due to their durability, resistance properties, and ability to enhance the performance of components. However, potential limitations such as color damage should be considered when selecting PVD coatings for specific applications.
Summary Table:
Aspect | Details |
---|---|
Durability | Highly resistant to corrosion, scratches, and wear. |
Performance | Enhances hardness, wear resistance, and reduces friction. |
Thinness & Strength | Extremely thin yet strong, retaining original shape and finish. |
Limitations | Susceptible to color damage in aggressive conditions; may not be repairable. |
Applications | Used in electronics, optics, solar energy, and medical devices. |
Learn more about how PVD coatings can benefit your industry—contact our experts today!