The main difference between Atomic Layer Deposition (ALD) and Chemical Vapor Deposition (CVD) lies in their deposition mechanisms, control over film properties, and application suitability. ALD is a sequential, self-limiting process that deposits thin films layer-by-layer, offering exceptional precision in thickness, conformality, and uniformity, making it ideal for ultra-thin films (10-50 nm) and high-aspect-ratio structures. CVD, on the other hand, is a continuous process that allows for higher deposition rates and thicker films, with a broader range of precursor materials. While ALD operates at controlled temperatures, CVD often requires higher temperatures. Both methods are used for thin film deposition, but ALD excels in precision and conformality, whereas CVD is better suited for high-throughput applications.
Key Points Explained:
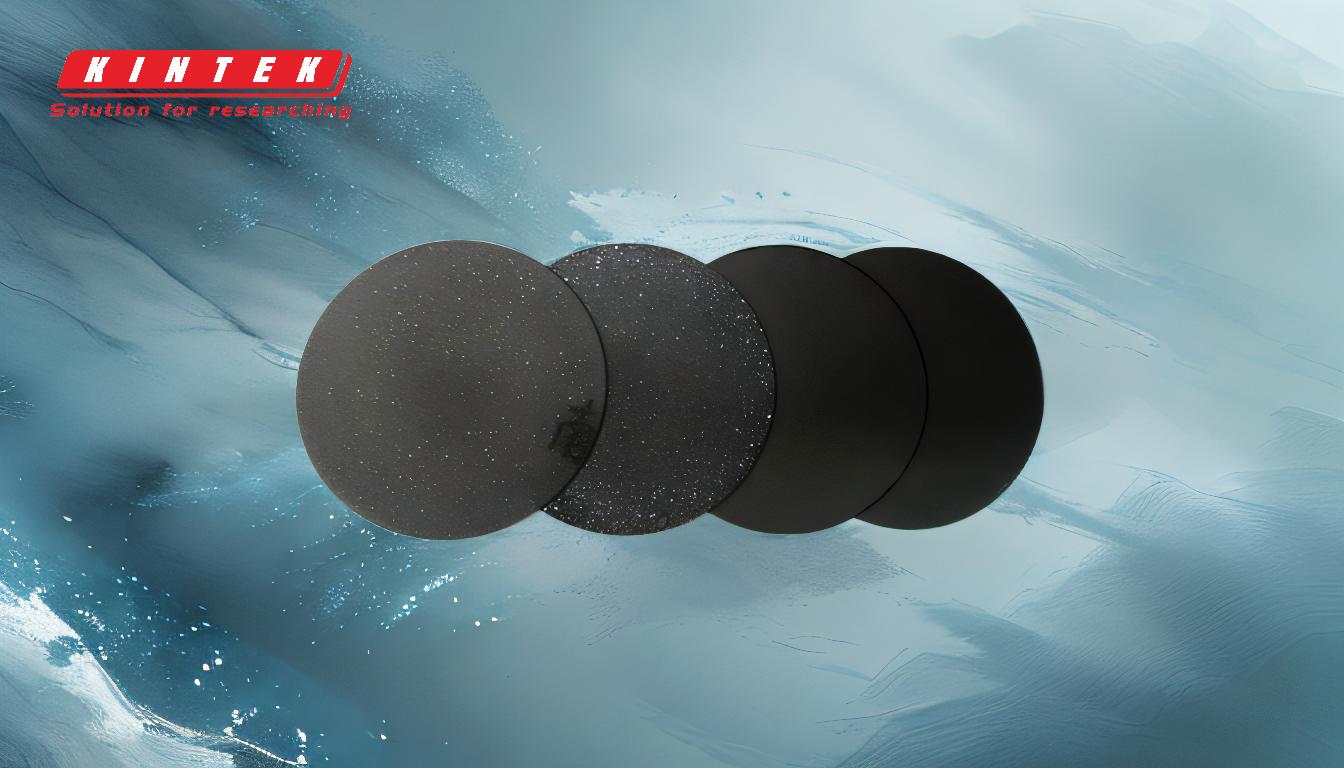
-
Deposition Mechanism:
- ALD: ALD breaks the deposition process into discrete, self-limiting steps. Precursors and reactants are introduced sequentially, ensuring that only one monolayer is deposited at a time. This results in precise control over film thickness and uniformity.
- CVD: CVD is a continuous process where precursors and reactants are simultaneously introduced into the chamber, leading to simultaneous chemical reactions and deposition. This allows for faster deposition rates but less control over individual layers.
-
Control Over Film Properties:
- ALD: ALD provides superior control over film thickness, density, and conformality. Its layer-by-layer approach ensures uniformity even on complex, high-aspect-ratio structures. This makes ALD ideal for applications requiring ultra-thin, precise films.
- CVD: CVD offers less precise control over individual layers but is better suited for depositing thicker films at higher rates. It is more versatile in terms of precursor availability and can handle a wider range of materials.
-
Application Suitability:
- ALD: ALD is preferred for applications requiring ultra-thin films (10-50 nm) and high conformality, such as in semiconductor manufacturing, MEMS, and nanotechnology. Its precision makes it ideal for multi-layer films and high-aspect-ratio structures.
- CVD: CVD is better suited for applications requiring thicker films and higher deposition rates, such as in coatings, solar cells, and large-area electronics. Its versatility in precursor selection allows for a broader range of material deposition.
-
Temperature Requirements:
- ALD: ALD operates at relatively controlled and lower temperatures compared to CVD, making it suitable for temperature-sensitive substrates.
- CVD: CVD often requires higher temperatures to facilitate the chemical reactions, which can limit its use with certain substrates.
-
Precursor Usage:
- ALD: ALD uses two precursors that are introduced sequentially, ensuring they never coexist in the chamber. This sequential process enhances control over the deposition and reduces unwanted reactions.
- CVD: CVD allows for the simultaneous presence of multiple precursors, enabling faster deposition but increasing the risk of unwanted side reactions.
-
Conformality and Uniformity:
- ALD: ALD excels in conformality, ensuring uniform deposition even on complex 3D structures. This is due to its self-limiting nature and sequential precursor introduction.
- CVD: While CVD can achieve good conformality, it is generally less uniform than ALD, especially on high-aspect-ratio structures.
In summary, ALD and CVD are complementary techniques, each with its strengths. ALD is the go-to method for precision and conformality in ultra-thin films, while CVD is preferred for high-throughput and thicker film applications. The choice between the two depends on the specific requirements of the application, such as film thickness, deposition rate, and substrate compatibility.
Summary Table:
Aspect | ALD | CVD |
---|---|---|
Deposition Mechanism | Sequential, self-limiting process | Continuous process with simultaneous precursor introduction |
Film Control | Superior precision in thickness, density, and conformality | Less precise but faster deposition rates for thicker films |
Applications | Ideal for ultra-thin films (10-50 nm) and high-aspect-ratio structures | Suitable for thicker films, coatings, and high-throughput applications |
Temperature | Operates at controlled, lower temperatures | Requires higher temperatures for chemical reactions |
Precursor Usage | Sequential introduction of two precursors | Simultaneous presence of multiple precursors |
Conformality | Exceptional uniformity on complex 3D structures | Good conformality but less uniform on high-aspect-ratio structures |
Need help choosing between ALD and CVD for your application? Contact our experts today!