The main frequency of an induction furnace is not fixed but varies depending on the specific application, material being melted, furnace capacity, and desired melting speed. It typically ranges from utility frequency (50 or 60 Hz) to as high as 400 kHz or more. Smaller furnaces or those melting smaller volumes of metal often operate at higher frequencies due to the skin depth effect, which ensures efficient heating with shallower penetration. Larger furnaces, on the other hand, may use lower frequencies to generate stirring or turbulence in the molten metal. The frequency is also influenced by factors such as the melting material, desired stirring effect, and energy efficiency.
Key Points Explained:
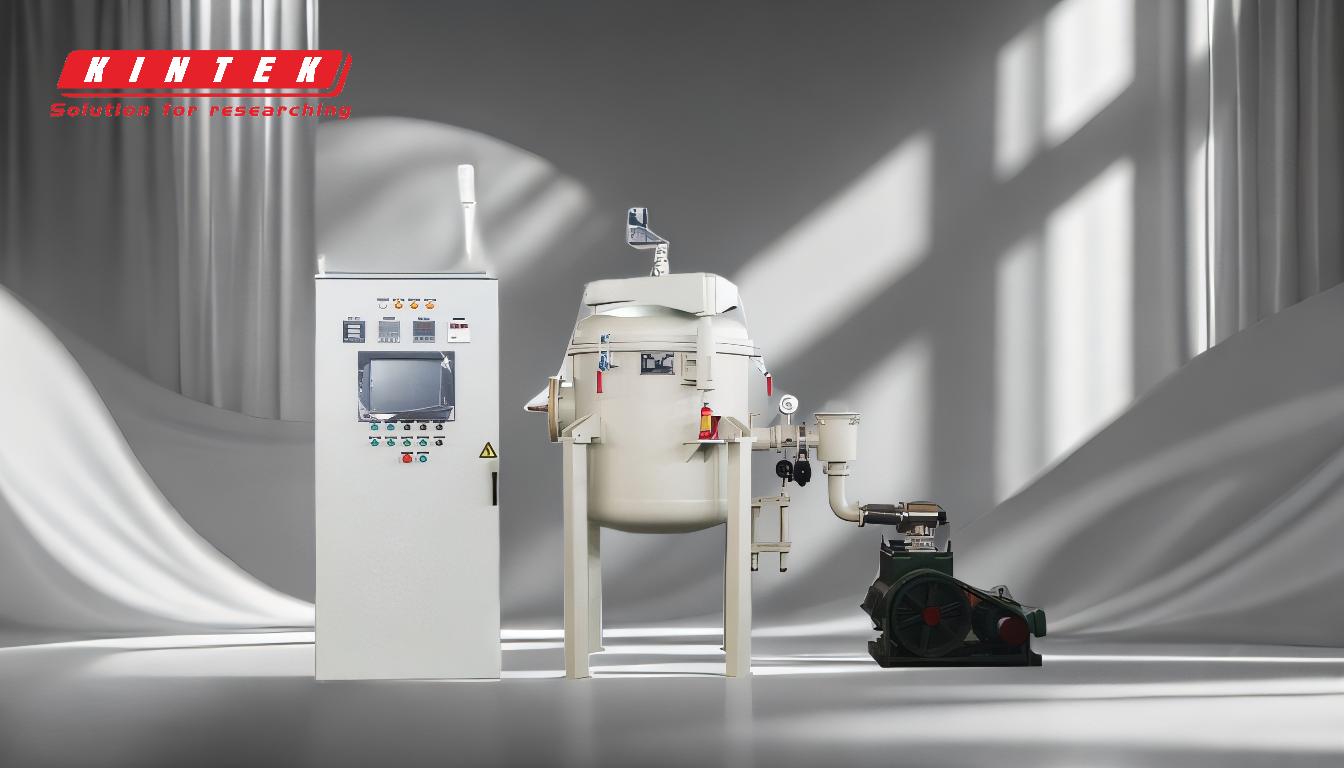
-
Frequency Range of Induction Furnaces:
- Induction furnaces operate across a wide frequency range, from utility frequency (50 or 60 Hz) to 400 kHz or higher. This flexibility allows them to be tailored for specific applications and materials.
- Higher frequencies are typically used for smaller furnaces or smaller volumes of metal, while lower frequencies are suitable for larger furnaces or when stirring is required.
-
Factors Influencing Frequency Selection:
- Material Being Melted: Different materials have varying electrical and thermal properties, which affect the optimal frequency for efficient heating.
- Furnace Capacity: Smaller furnaces benefit from higher frequencies due to the skin depth effect, ensuring efficient heating with minimal energy loss.
- Melting Speed: Higher frequencies can achieve faster melting rates for smaller volumes, while lower frequencies are better for larger volumes and slower, more controlled melting.
-
Skin Depth Effect:
- The skin depth effect refers to how deeply an alternating current can penetrate a conductor. Higher frequencies result in shallower penetration, which is ideal for smaller volumes or thin materials.
- Lower frequencies penetrate deeper, making them suitable for larger volumes and generating turbulence or stirring in the molten metal.
-
Advantages of Frequency Adjustment:
- Efficiency: Higher frequencies ensure efficient heating for small volumes, reducing energy consumption.
- Stirring Effect: Lower frequencies can create turbulence in the molten metal, improving composition uniformity and aiding in scum removal.
- Flexibility: The ability to adjust frequency based on the material and furnace capacity makes induction furnaces versatile for various industrial applications.
-
Practical Applications:
- Small-Scale Melting: High-frequency induction furnaces are ideal for melting small quantities of metal, such as in jewelry making or laboratory settings.
- Large-Scale Melting: Lower-frequency furnaces are used in industrial settings for melting large volumes of metal, such as in foundries or steel production.
-
Design Considerations:
- The frequency of an induction furnace can be designed by adjusting the coil and compensating capacitor. This allows customization based on the melting material, quantity, and desired effects like stirring or noise reduction.
- Advanced features like automatic frequency scanning and constant power circuit control ensure smooth and stable operation across a range of frequencies.
In summary, the main frequency of an induction furnace is highly adaptable and depends on the specific requirements of the application. Understanding the relationship between frequency, material properties, and furnace capacity is crucial for optimizing performance and efficiency.
Summary Table:
Factor | Impact on Frequency |
---|---|
Material Being Melted | Different materials require specific frequencies for efficient heating. |
Furnace Capacity | Smaller furnaces use higher frequencies; larger furnaces use lower frequencies. |
Melting Speed | Higher frequencies for faster melting; lower frequencies for slower, controlled melting. |
Skin Depth Effect | Higher frequencies = shallow penetration; lower frequencies = deeper penetration. |
Optimize your induction furnace performance—contact our experts today for tailored solutions!