The maximum temperature of an arc furnace typically exceeds 3000℃ in the arc area during electric discharge, making it capable of melting and refining a wide range of materials, including metals and alloys. This high temperature is achieved through the intense heat generated by the electric arc between the electrodes and the charge. Arc furnaces are designed with components like water-cooled copper hearths, graphite or carbon electrodes, and refractory-lined casings to withstand these extreme temperatures. Their simplicity, ease of access, and ability to maintain high purity levels make them highly effective for industrial applications.
Key Points Explained:
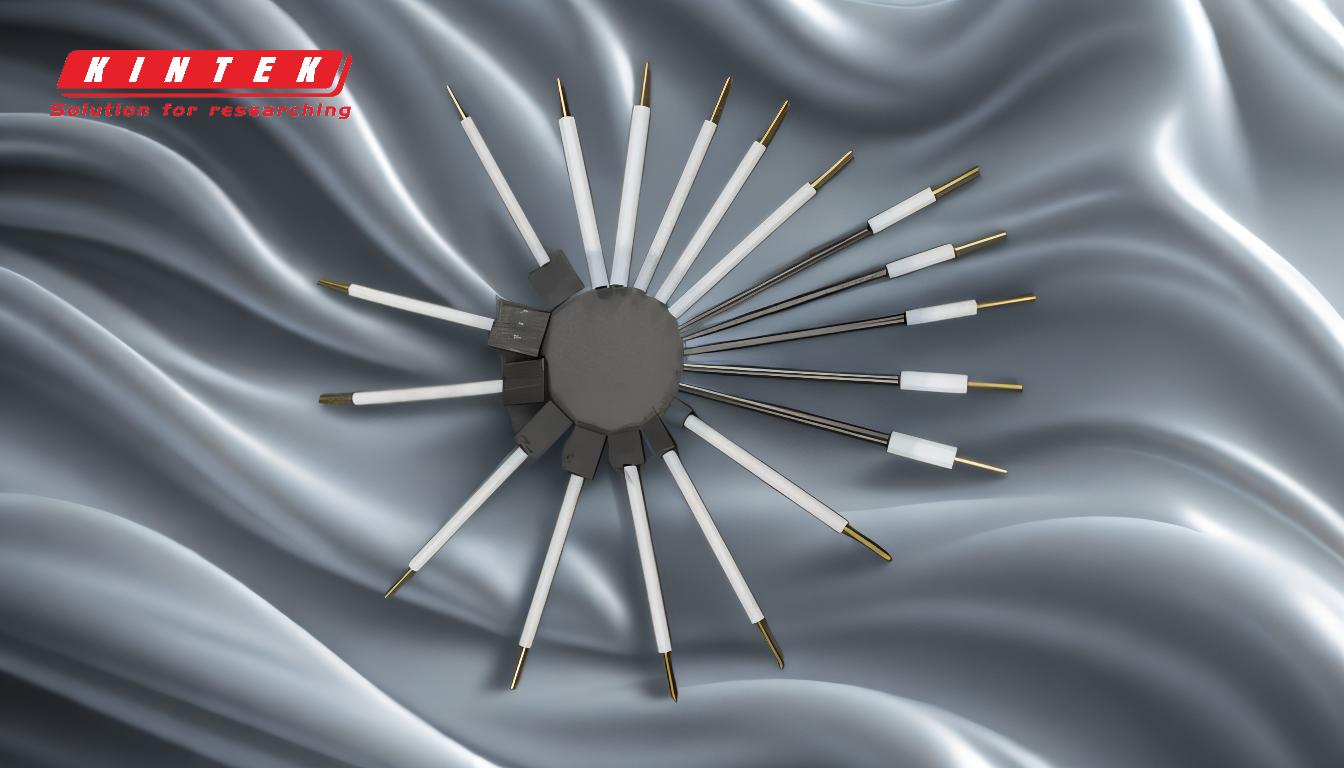
-
Maximum Temperature in the Arc Area:
- The arc area of an electric arc furnace can reach temperatures above 3000℃ during operation. This extreme heat is generated by the electric arc formed between the electrodes and the charge, enabling the melting and refining of metals and alloys.
-
Components Designed for High Temperatures:
- Graphite or Carbon Electrodes: These materials are used because they can withstand the high temperatures and electrical conductivity required for arc formation.
- Water-Cooled Copper Hearth: The hearth is designed to collect molten metal and is water-cooled to prevent overheating and damage.
- Refractory-Lined Casing: The furnace's metal casing is lined with refractory materials to endure the intense heat and protect the structure.
-
Advantages of Arc Furnaces:
- High Purity: The design ensures a high degree of purity in the molten metal, making it suitable for applications requiring clean, uncontaminated materials.
- Simplicity and Accessibility: The furnace's small volume and ease of access allow for quick specimen preparation and efficient operation.
- Efficient Heat Generation: The electric arc provides a concentrated and controllable heat source, enabling precise temperature management.
-
Operational Considerations:
- Temperature Limits: While the arc area can exceed 3000℃, other components like the resistance furnace have lower temperature limits, and exceeding these can cause damage.
- Model Variations: Different models of furnaces, such as preheating furnaces, have varying maximum temperatures, with some reaching around 1200℃. However, arc furnaces are specifically designed for much higher temperatures.
-
Industrial Applications:
- Arc furnaces are widely used in industries requiring high-temperature processing, such as steelmaking, metal recycling, and alloy production. Their ability to handle extreme temperatures and maintain material purity makes them indispensable in these fields.
By understanding these key points, equipment purchasers can make informed decisions about the suitability of arc furnaces for their specific industrial needs.
Summary Table:
Key Feature | Details |
---|---|
Maximum Temperature | Exceeds 3000℃ in the arc area |
Key Components | Graphite/carbon electrodes, water-cooled copper hearth, refractory-lined casing |
Advantages | High purity, simplicity, accessibility, efficient heat generation |
Applications | Steelmaking, metal recycling, alloy production |
Ready to harness the power of arc furnaces for your industrial needs? Contact us today to learn more!