Calendering is a manufacturing process used to smooth, compress, or combine materials by passing them through a series of heated rollers or calenders. It is commonly applied in industries such as paper production, rubber manufacturing, and textiles. The process enhances the material's surface finish, thickness, and density, and can also be used to bond materials together. Calendering is versatile, with applications ranging from creating smooth paper surfaces to combining rubber sheets with fabrics. The process involves precise control of temperature, pressure, and roller speed to achieve the desired material properties.
Key Points Explained:
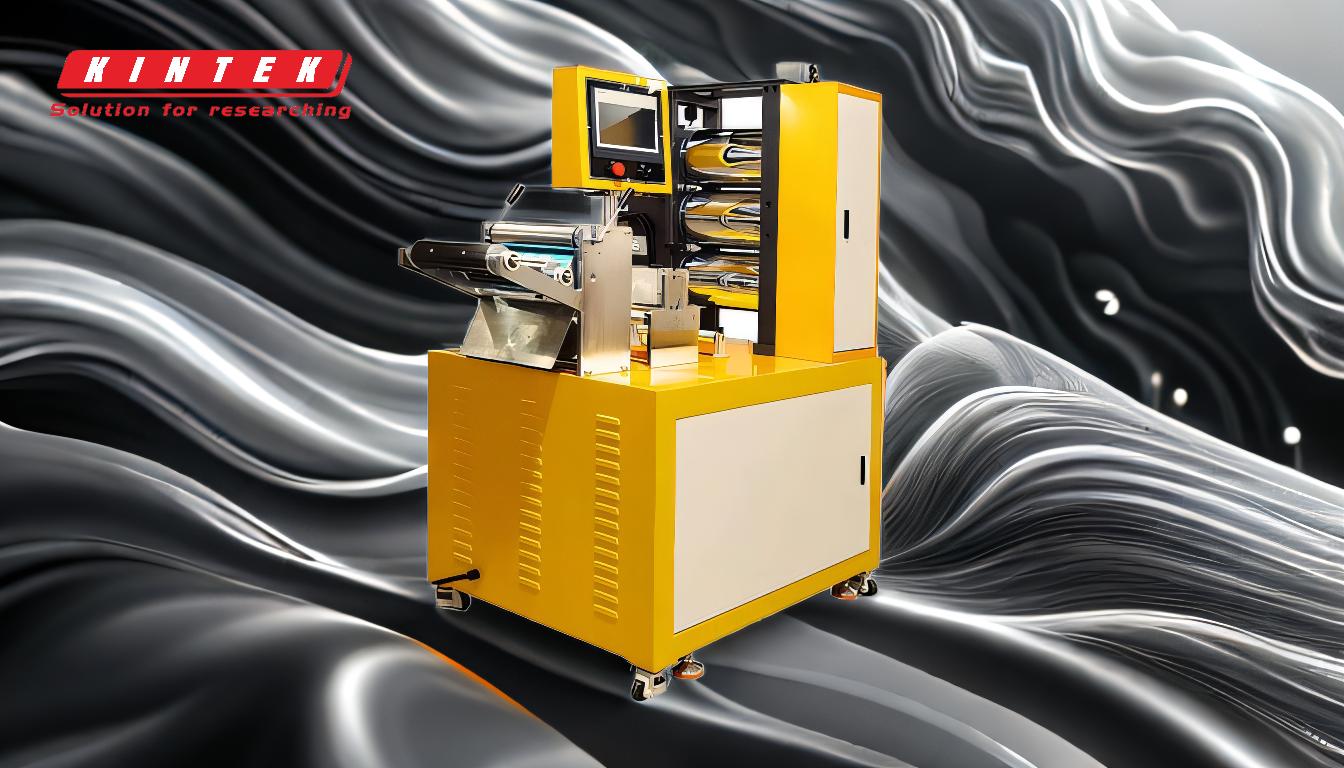
-
Definition of Calendering:
- Calendering is a process that involves passing a material, such as paper, rubber, or textiles, through a series of heated rollers (calenders) to achieve specific properties like smoothness, compression, or bonding.
- The rollers apply pressure and heat, which helps in refining the material's surface and structure.
-
Applications of Calendering:
- Paper Production: Calendering is widely used in the paper industry to create smooth and glossy paper surfaces. The process compresses the paper fibers, resulting in a uniform thickness and improved printability.
- Rubber Manufacturing: In the rubber industry, calendering machines are used to produce rubber sheets of precise thickness and to combine rubber with other materials or fabrics. This is often done through processes like frictioning or combining.
- Textiles: Calendering is also employed in the textile industry to enhance fabric properties, such as smoothness, sheen, or water resistance.
-
Types of Calendering Processes:
- Frictioning: A process where rubber is passed through rollers to bond it with fabric or other materials. This is commonly used in the production of rubberized fabrics.
- Combining: This involves layering different materials together using calendering rollers to create composite materials with specific properties.
-
Key Components of Calendering Machines:
- Rollers/Calenders: The primary components of a calendering machine, these rollers are typically heated and can be adjusted for pressure and speed.
- Heating System: Ensures the rollers are at the optimal temperature to achieve the desired material properties.
- Control Systems: Modern calendering machines are equipped with advanced control systems to regulate temperature, pressure, and roller speed, ensuring precision and consistency.
-
Benefits of Calendering:
- Improved Surface Finish: Calendering provides a smooth and polished surface, which is essential for materials like paper and textiles.
- Enhanced Material Properties: The process can improve the density, thickness uniformity, and durability of materials.
- Versatility: Calendering can be adapted for various materials and applications, making it a versatile manufacturing process.
-
Challenges in Calendering:
- Precision Requirements: Achieving the desired material properties requires precise control of temperature, pressure, and roller speed, which can be challenging.
- Material Limitations: Not all materials are suitable for calendering, as some may degrade under heat and pressure.
- Equipment Costs: High-quality calendering machines can be expensive, requiring significant investment.
-
Future Trends in Calendering:
- Automation: Increasing use of automation and advanced control systems to improve precision and efficiency.
- Eco-Friendly Processes: Development of more sustainable calendering processes to reduce environmental impact.
- Advanced Materials: Calendering is being adapted for new materials, such as composites and nanomaterials, to meet evolving industry demands.
In summary, calendering is a critical process in various industries, offering significant benefits in terms of material properties and surface finish. However, it requires precise control and investment in specialized equipment. As technology advances, calendering is likely to become even more efficient and adaptable to new materials and applications.
Summary Table:
Aspect | Details |
---|---|
Definition | Process of passing materials through heated rollers for smoothing, bonding, or compressing. |
Applications | Paper production, rubber manufacturing, textiles. |
Key Benefits | Improved surface finish, enhanced material properties, versatility. |
Challenges | Precision requirements, material limitations, high equipment costs. |
Future Trends | Automation, eco-friendly processes, advanced materials. |
Learn how calendering can optimize your manufacturing process—contact us today for expert guidance!