Debinding is a critical step in various manufacturing processes, particularly in powder metallurgy, 3D printing, and technical ceramics. It involves the removal of binding materials (also called carrier materials) that are initially used to shape and compact parts. These binders are essential during the molding or printing phase but become unnecessary and even detrimental during sintering. Debinding ensures the final product is sturdy, prevents furnace contamination, and improves process efficiency. The process can be carried out through thermal or chemical methods, depending on the material and application. Proper control of temperature, time, and atmosphere is crucial to avoid defects such as warping, cracking, or residual contamination, which could compromise the part's mechanical and corrosion-resistant properties.
Key Points Explained:
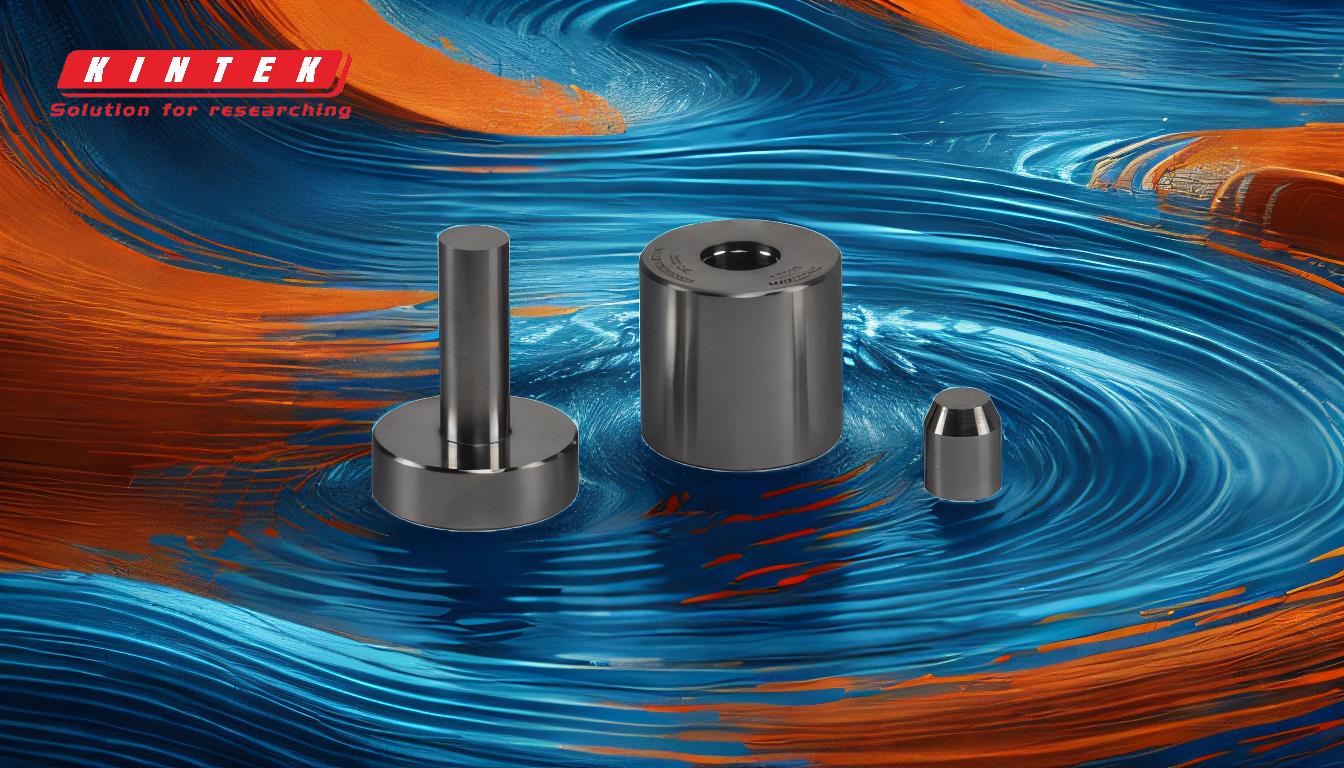
-
Definition of Debinding
- Debinding is the process of removing binding or carrier materials from molded or 3D-printed parts.
- These binders are initially used to shape and compact the part but must be removed before sintering to ensure the final product's integrity.
-
Purpose of Debinding
- Prevents Furnace Contamination: Residual binders can clog furnaces and contaminate the sintering environment.
- Enhances Part Quality: Removing binders ensures the part becomes sturdy and free from defects.
- Improves Process Efficiency: Debinding makes the overall manufacturing process faster and more efficient compared to sintering alone.
-
Methods of Debinding
-
Thermal Debinding: Involves heating the part in a furnace to burn off or evaporate the binder.
- For organic binders, evaporation typically starts around 392°F (200°C) and is completed before reaching 932°F (500°C).
- Requires careful control of temperature profiles to avoid cracking or warping.
-
Chemical Debinding: Uses chemical baths to dissolve the binder.
- Suitable for parts with complex geometries or materials sensitive to high temperatures.
- Time Considerations: Debinding can take up to 24-36 hours, depending on the part's geometry and binder type.
-
Thermal Debinding: Involves heating the part in a furnace to burn off or evaporate the binder.
-
Importance in Specific Applications
- Powder Metallurgy: Ensures binders are removed before sintering to avoid interference with the final product's properties.
- 3D Printing: Removes carrier materials from printed parts, preparing them for sintering or further processing.
- Technical Ceramics: Involves removing moisture and organic binders from green bodies, typically finishing at 600°C.
-
Challenges and Considerations
- Defect Prevention: Improper debinding can lead to cracks, deformations, or residual carbon-based materials, negatively impacting corrosion resistance and mechanical properties.
- Process Control: Requires precise management of temperature, pressure, gas atmosphere, and anneal time.
- Material-Specific Requirements: Different binders and part geometries necessitate tailored debinding parameters.
-
Impact on Final Product
- Ensures the part is free from contaminants that could compromise its performance.
- Enhances the part's structural integrity and mechanical properties.
- Prepares the part for the sintering process, where it achieves its final density and strength.
By understanding the debinding process and its critical role, manufacturers can optimize their workflows, reduce defects, and produce high-quality components efficiently.
Summary Table:
Aspect | Details |
---|---|
Definition | Removal of binding materials from molded or 3D-printed parts. |
Purpose | Prevents furnace contamination, enhances part quality, improves efficiency. |
Methods | Thermal (heating) or Chemical (dissolving) debinding. |
Applications | Powder metallurgy, 3D printing, technical ceramics. |
Challenges | Cracking, warping, residual contamination. |
Impact | Ensures structural integrity, prepares parts for sintering. |
Optimize your manufacturing process with expert debinding solutions—contact us today!