Sputtering is a thin-film deposition process widely used in industries such as semiconductor manufacturing, precision optics, and surface finishing. It involves bombarding a target material with ions in a vacuum chamber, causing atoms to be ejected from the target's surface. These ejected atoms travel through the chamber and deposit onto a substrate, forming a thin film with excellent uniformity, density, and adhesion. The process is highly controlled, allowing for precise manipulation of film properties like reflectivity, electrical resistivity, and grain structure. Sputtering is essential for creating high-quality coatings and films used in advanced technologies.
Key Points Explained:
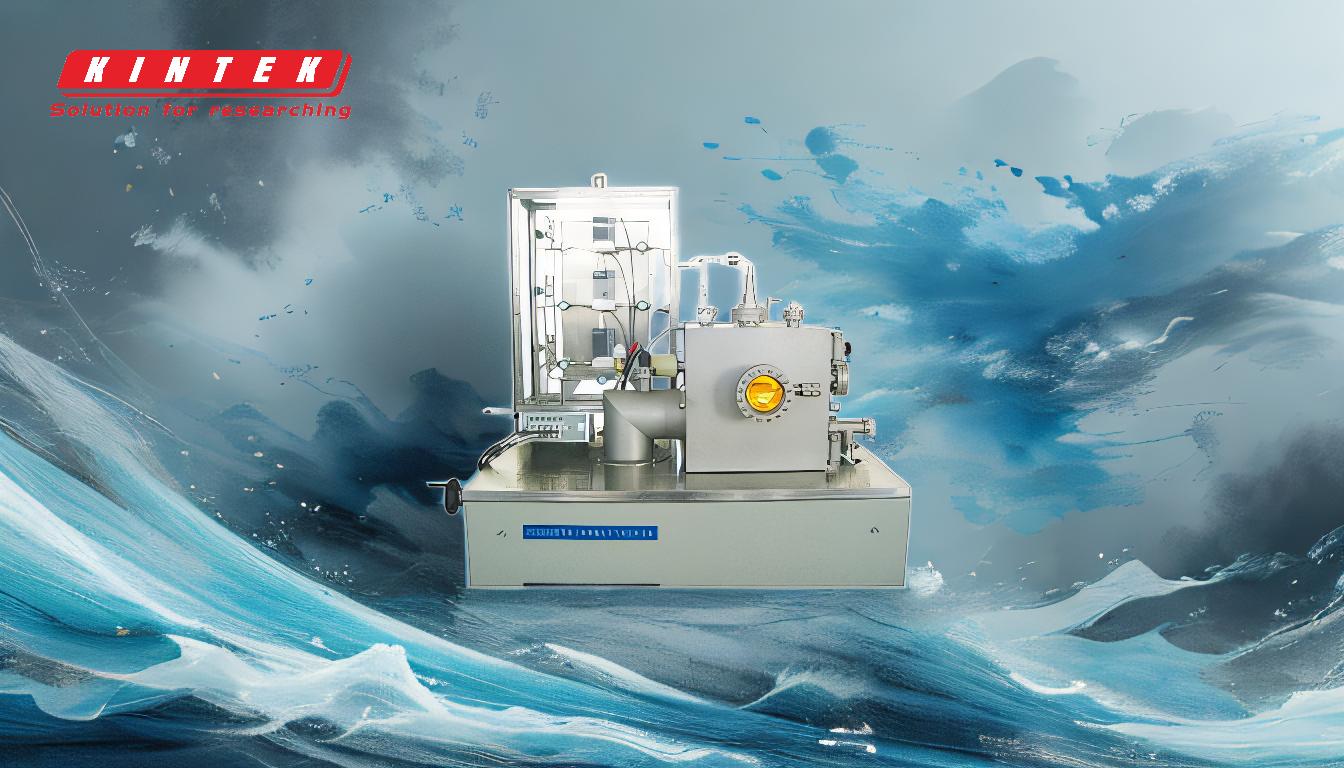
-
Definition of Sputtering:
- Sputtering is a physical vapor deposition (PVD) technique used to deposit thin films of a material onto a substrate. It involves the ejection of atoms from a solid target material due to bombardment by high-energy ions, typically from an inert gas like argon.
-
The Sputtering Process:
- Vacuum Chamber Setup: The target material and substrate are placed in a vacuum chamber to eliminate contaminants and ensure a clean deposition environment.
- Introduction of Sputtering Gas: An inert gas, such as argon, is introduced into the chamber.
- Plasma Generation: A voltage is applied to create a plasma, ionizing the gas atoms and generating positively charged ions.
- Ion Bombardment: The ions are accelerated toward the target material (cathode) due to the applied electric field.
- Ejection of Target Atoms: The ions strike the target with sufficient kinetic energy to dislodge atoms or molecules from its surface.
- Film Deposition: The ejected atoms travel through the chamber and deposit onto the substrate, forming a thin film.
-
Key Components of Sputtering:
- Target Material: The source material from which atoms are ejected. Common targets include metals, alloys, and ceramics.
- Substrate: The surface onto which the thin film is deposited. Substrates can be silicon wafers, glass, plastics, or other materials.
- Sputtering Gas: Typically an inert gas like argon, which is ionized to create the plasma.
- Plasma: A high-energy state of matter where gas atoms are ionized, creating a mixture of ions, electrons, and neutral particles.
-
Advantages of Sputtering:
- High Precision: Sputtering allows for the deposition of thin films with excellent uniformity, density, and adhesion.
- Versatility: It can deposit a wide range of materials, including metals, semiconductors, and insulators.
- Controlled Film Properties: The process enables precise control over film morphology, grain size, and orientation, making it suitable for specialized applications.
- Scalability: Sputtering is compatible with large-scale industrial production.
-
Applications of Sputtering:
- Semiconductor Industry: Used for depositing thin films in the fabrication of integrated circuits, transistors, and other electronic components.
- Optics: Applied in the production of anti-reflective coatings, mirrors, and precision optical components.
- Surface Finishing: Used to enhance the durability, corrosion resistance, and aesthetic appeal of materials.
- Energy: Utilized in the manufacturing of solar cells, batteries, and fuel cells.
-
Types of Sputtering:
- DC Sputtering: Uses a direct current (DC) power supply to generate the plasma. Suitable for conductive target materials.
- RF Sputtering: Employs radio frequency (RF) power to ionize the gas, making it suitable for insulating materials.
- Magnetron Sputtering: Incorporates magnetic fields to enhance plasma density and deposition rates, improving efficiency.
-
Challenges and Considerations:
- Target Erosion: Continuous bombardment can lead to target degradation, requiring periodic replacement.
- Contamination: Impurities in the sputtering gas or chamber can affect film quality.
- Energy Efficiency: The process can be energy-intensive, particularly for large-scale applications.
-
Future Trends in Sputtering:
- Advanced Materials: Development of new target materials for emerging technologies like flexible electronics and quantum computing.
- Process Optimization: Improvements in energy efficiency and deposition rates through advanced plasma control techniques.
- Nanotechnology: Increasing use of sputtering for nanoscale thin films and nanostructured materials.
In summary, sputtering is a versatile and precise thin-film deposition technique with widespread applications in modern technology. Its ability to produce high-quality coatings with controlled properties makes it indispensable in industries ranging from electronics to optics and energy.
Summary Table:
Aspect | Details |
---|---|
Definition | Physical vapor deposition (PVD) technique for thin-film deposition. |
Process Steps | Vacuum setup, gas introduction, plasma generation, ion bombardment, deposition. |
Key Components | Target material, substrate, sputtering gas (e.g., argon), plasma. |
Advantages | High precision, versatility, controlled film properties, scalability. |
Applications | Semiconductors, optics, surface finishing, energy (solar cells, batteries). |
Types | DC sputtering, RF sputtering, magnetron sputtering. |
Challenges | Target erosion, contamination, energy efficiency. |
Future Trends | Advanced materials, process optimization, nanotechnology applications. |
Ready to explore how sputtering can enhance your applications? Contact our experts today for tailored solutions!