Chemical vapor deposition (CVD) is a widely used method for synthesizing graphene, particularly for producing large-area, high-quality graphene sheets. The process involves the decomposition of carbon-containing precursors on a catalytic substrate, typically at high temperatures, to form graphene. The mechanism of CVD graphene involves several key steps, including the adsorption of carbon precursors, their decomposition into carbon species, nucleation, and growth of graphene crystals. This method is highly controllable and scalable, making it suitable for industrial applications. The quality and properties of the graphene produced depend on factors such as the type of precursor, the catalytic substrate, and the process conditions.
Key Points Explained:
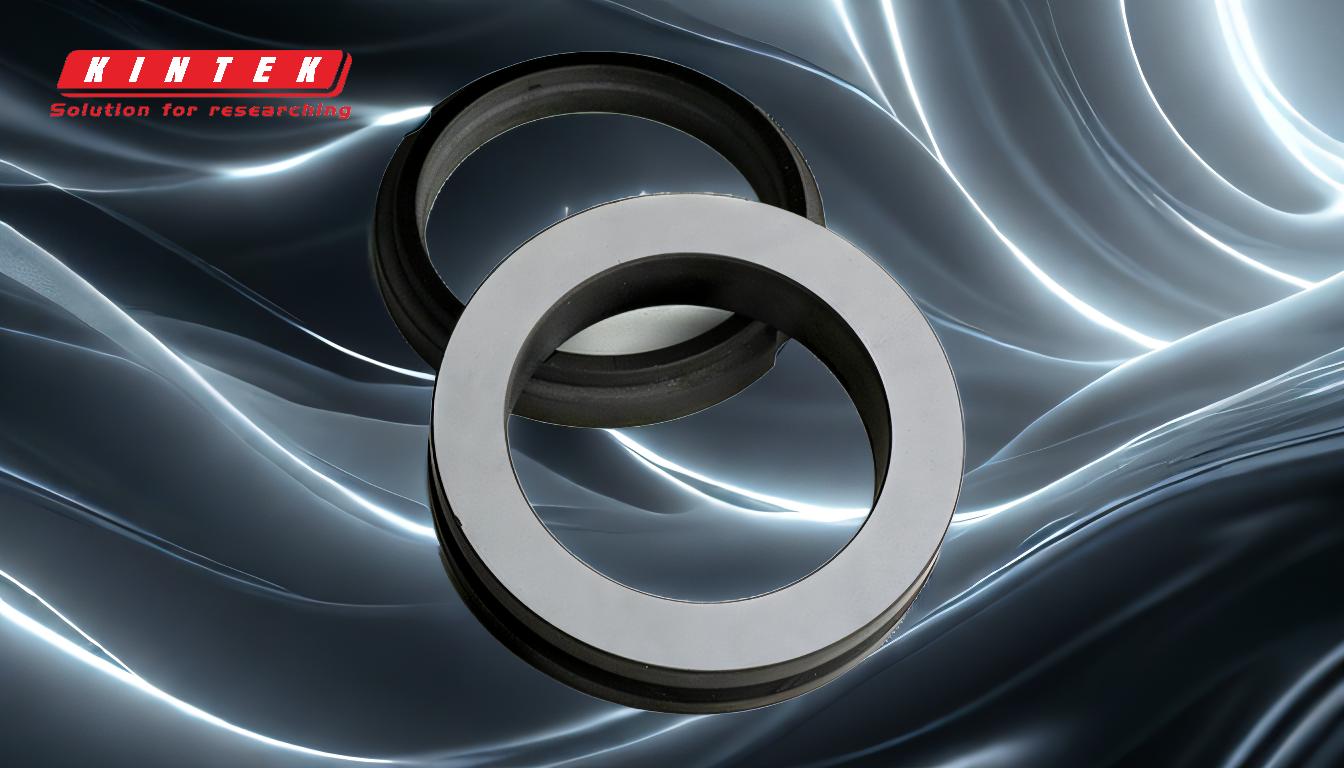
-
Introduction to CVD Graphene Synthesis:
- CVD is a bottom-up approach for synthesizing graphene, where carbon atoms are deposited onto a catalytic substrate to form a graphene layer.
- The process is particularly effective for producing large-area, monolayer graphene sheets, which are essential for various applications in electronics, energy storage, and composites.
-
Role of Precursors and Catalysts:
- The carbon precursor, often methane (CH₄), is introduced into the CVD reactor. Methane is chosen because it decomposes easily at high temperatures to release carbon atoms.
- The catalytic substrate, typically copper (Cu) or nickel (Ni), plays a crucial role in the process. Copper is preferred for producing monolayer graphene due to its low carbon solubility, which limits the formation of multiple layers.
- The catalyst lowers the energy barrier for the decomposition of the precursor and facilitates the formation of graphene.
-
Steps in the CVD Process:
- Transport of Gaseous Species: The carbon precursor and other gases are transported into the reactor and pass through a high-temperature zone.
- Adsorption and Decomposition: The carbon precursor adsorbs onto the catalytic substrate and decomposes into carbon radicals at high temperatures (around 1000 °C).
- Nucleation and Growth: The carbon radicals diffuse across the substrate surface and nucleate to form graphene crystals. The growth of these crystals results in the formation of a continuous graphene layer.
- Desorption and Removal of By-products: Gaseous by-products, such as hydrogen, are desorbed from the surface and removed from the reactor.
-
Factors Influencing Graphene Quality:
- Temperature: The temperature must be carefully controlled to ensure the proper decomposition of the precursor and the growth of high-quality graphene. Too high or too low temperatures can lead to defects or incomplete graphene layers.
- Pressure: The pressure inside the reactor affects the rate of precursor decomposition and the diffusion of carbon species on the substrate.
- Substrate Nature: The choice of substrate (e.g., Cu, Ni) and its surface properties (e.g., roughness, crystallinity) influence the nucleation and growth of graphene.
- Gas Flow Rate: The flow rate of the precursor and carrier gases must be optimized to ensure uniform deposition and avoid the formation of defects.
-
Types of CVD Processes:
- Thermal CVD: This is the most common method, where the substrate is heated to high temperatures to facilitate the decomposition of the precursor and the growth of graphene.
- Plasma-Enhanced CVD (PECVD): In this method, a plasma is used to lower the temperature required for precursor decomposition, making it suitable for temperature-sensitive substrates.
-
Challenges and Considerations:
- Scalability: While CVD is the most scalable method for graphene production, achieving uniform quality over large areas remains a challenge.
- Defects and Contamination: Defects such as grain boundaries, wrinkles, and contamination from the substrate can affect the electrical and mechanical properties of graphene.
- Transfer Process: After graphene is grown on the catalytic substrate, it often needs to be transferred to another substrate for practical applications. This transfer process can introduce defects or damage the graphene layer.
-
Applications of CVD Graphene:
- Electronics: CVD graphene is used in transistors, sensors, and flexible electronics due to its excellent electrical conductivity and mechanical flexibility.
- Energy Storage: Graphene produced by CVD is used in supercapacitors and batteries to enhance energy storage capacity and charge/discharge rates.
- Composites: CVD graphene is incorporated into polymers and other materials to improve their mechanical, thermal, and electrical properties.
In summary, the mechanism of CVD graphene involves a series of well-controlled steps, from the decomposition of carbon precursors to the nucleation and growth of graphene crystals on a catalytic substrate. The process is highly dependent on factors such as temperature, pressure, and substrate properties, which must be carefully optimized to produce high-quality graphene. Despite some challenges, CVD remains the most promising method for large-scale graphene production, with applications spanning various industries.
Summary Table:
Key Aspect | Details |
---|---|
Process | Chemical vapor deposition (CVD) |
Precursor | Methane (CH₄) or other carbon-containing gases |
Catalytic Substrate | Copper (Cu) or Nickel (Ni) |
Steps | Adsorption, decomposition, nucleation, growth, and by-product removal |
Key Factors | Temperature, pressure, substrate nature, and gas flow rate |
Types of CVD | Thermal CVD, Plasma-Enhanced CVD (PECVD) |
Applications | Electronics, energy storage, and composites |
Challenges | Scalability, defects, contamination, and transfer process |
Learn how CVD graphene can revolutionize your industry—contact our experts today for more information!