The PVD (Physical Vapor Deposition) coating process is a sophisticated method used to create thin, durable, and functional coatings on various substrates. It involves vaporizing a solid material in a vacuum environment, transporting the vaporized atoms to the substrate, and depositing them to form a thin film. This process enhances the substrate's properties, such as hardness, wear resistance, and corrosion resistance, while also improving its aesthetic appeal. The mechanism of PVD coating can be broken down into several key steps, including cleaning, vaporization, transportation, reaction, and deposition. Each step is critical to ensuring the quality and performance of the final coating.
Key Points Explained:
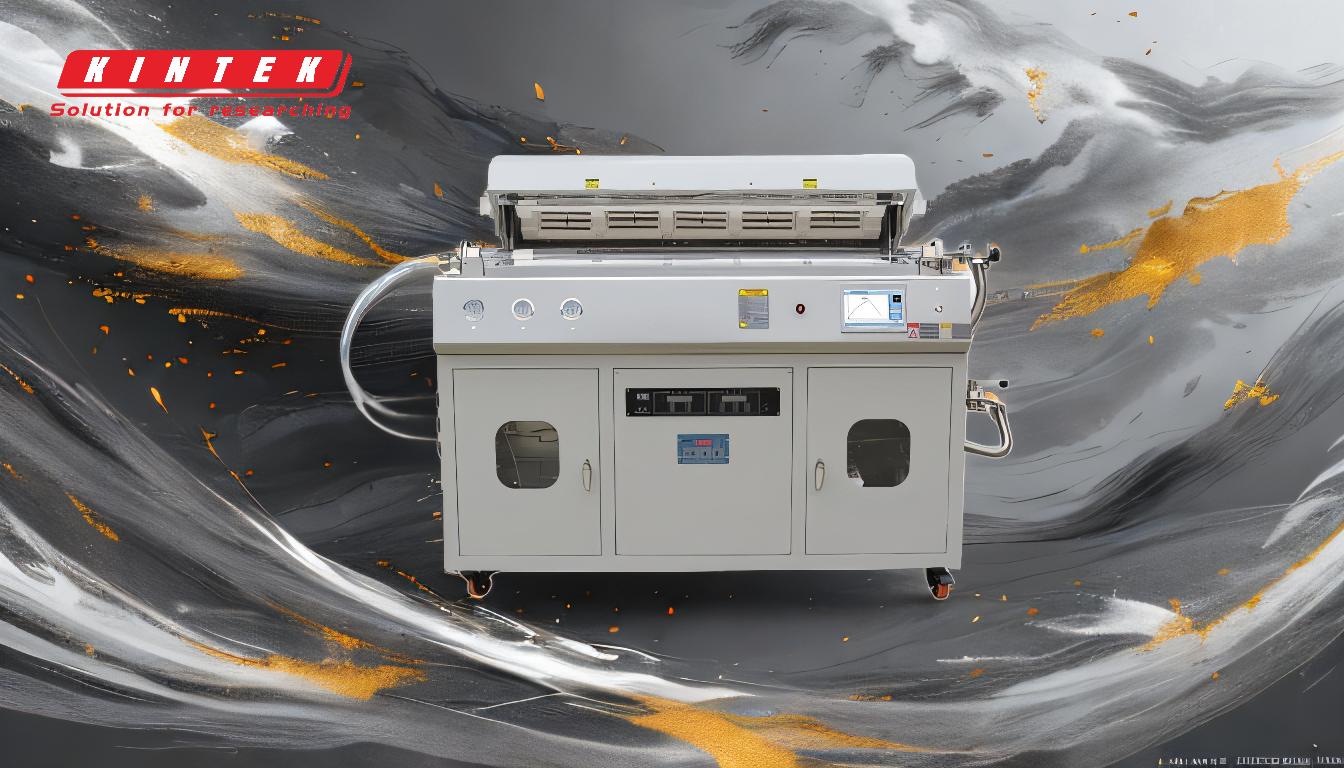
-
Cleaning and Pretreatment of the Substrate:
- Before the PVD coating process begins, the substrate must be thoroughly cleaned to remove any contaminants such as oils, dust, or oxides. This is crucial because any impurities on the surface can negatively affect the adhesion and quality of the coating.
- Pretreatment processes, such as plasma cleaning or etching, may also be employed to improve the surface energy and adhesion of the coating. This step ensures that the coating will bond effectively to the substrate.
-
Creation of a High-Vacuum Environment:
- The PVD coating process takes place in a vacuum chamber, which is evacuated to an extremely low pressure, typically in the range of 10^-3 to 10^-9 Torr. This high-vacuum environment is essential to prevent contamination from atmospheric gases and to allow the vaporized material to travel unimpeded to the substrate.
- The vacuum also ensures that the vaporized material remains clean and pure, which is critical for achieving high-quality coatings.
-
Vaporization of the Target Material:
- The target material, which is the source of the coating, is vaporized using one of several techniques, such as sputtering, arc evaporation, or electron beam evaporation. In sputtering, high-energy ions bombard the target, dislodging atoms from its surface. In arc evaporation, an electric arc vaporizes the target material, while in electron beam evaporation, a focused electron beam heats and vaporizes the target.
- The choice of vaporization technique depends on the material being coated and the desired properties of the coating.
-
Transportation of Vaporized Atoms:
- Once the target material is vaporized, the atoms or molecules are transported through the vacuum chamber to the substrate. This transportation occurs in a straight line due to the absence of air molecules in the vacuum environment.
- The distance between the target and the substrate, as well as the energy of the vaporized atoms, influences the uniformity and thickness of the coating.
-
Reaction with Reactive Gases (Optional):
- During the transportation phase, reactive gases such as nitrogen, oxygen, or acetylene can be introduced into the vacuum chamber. These gases react with the vaporized metal atoms to form compounds such as metal nitrides, oxides, or carbides.
- This reaction step is crucial for modifying the properties of the coating. For example, adding nitrogen can result in the formation of a hard, wear-resistant metal nitride coating.
-
Deposition and Condensation on the Substrate:
- The vaporized atoms or molecules eventually reach the substrate, where they condense and form a thin, uniform film. This deposition occurs atom by atom, resulting in a highly controlled and precise coating.
- The deposition process is influenced by factors such as the substrate temperature, the energy of the vaporized atoms, and the angle of incidence of the atoms on the substrate.
-
Quality Control and Finishing:
- After the coating is deposited, quality control measures are taken to ensure that the coating meets the required specifications. This may involve testing the coating's thickness, adhesion, hardness, and other properties.
- Finishing processes, such as polishing or additional surface treatments, may also be applied to enhance the coating's appearance or performance.
-
Environmental and Operational Advantages:
- PVD coating is considered an environmentally friendly process because it does not involve harmful chemicals or produce significant waste. The process is also highly efficient, with minimal material loss.
- The resulting coatings are durable, resistant to wear and corrosion, and can be tailored to meet specific functional or aesthetic requirements.
In summary, the mechanism of PVD coating involves a series of carefully controlled steps that transform a solid target material into a thin, high-performance coating on a substrate. Each step, from cleaning and vaporization to deposition and finishing, plays a critical role in ensuring the quality and functionality of the final product. The process is highly versatile, allowing for the creation of coatings with a wide range of properties, making it a valuable technique in industries such as automotive, aerospace, medical devices, and consumer electronics.
Summary Table:
Step | Description |
---|---|
Cleaning and Pretreatment | Remove contaminants and improve adhesion through cleaning and surface treatment. |
High-Vacuum Environment | Create a vacuum to prevent contamination and ensure clean vaporized material. |
Vaporization of Target | Use sputtering, arc evaporation, or electron beam to vaporize the target material. |
Transportation of Atoms | Transport vaporized atoms to the substrate in a straight line. |
Reaction with Gases (Optional) | Introduce reactive gases to modify coating properties (e.g., hardness). |
Deposition and Condensation | Deposit atoms onto the substrate to form a thin, uniform film. |
Quality Control and Finishing | Test and enhance coating properties for performance and appearance. |
Environmental Advantages | Eco-friendly, efficient, and produces durable, tailored coatings. |
Unlock the potential of PVD coatings for your applications—contact our experts today!