The melting loss of an induction furnace refers to the reduction in metal weight during the melting process due to factors such as oxidation, evaporation, and slag formation. This loss is influenced by several variables, including the melting rate, power configuration, charge cleanliness, furnace design, and refractory materials used. A clean charge, proper furnace block length, and suitable crucibles like quartz crucibles can minimize melting loss by improving efficiency and reducing heat transfer consumption. Additionally, overheating due to improper water flow, furnace lining dimensions, or refractory material can exacerbate melting loss. Understanding these factors helps optimize furnace operations and reduce material waste.
Key Points Explained:
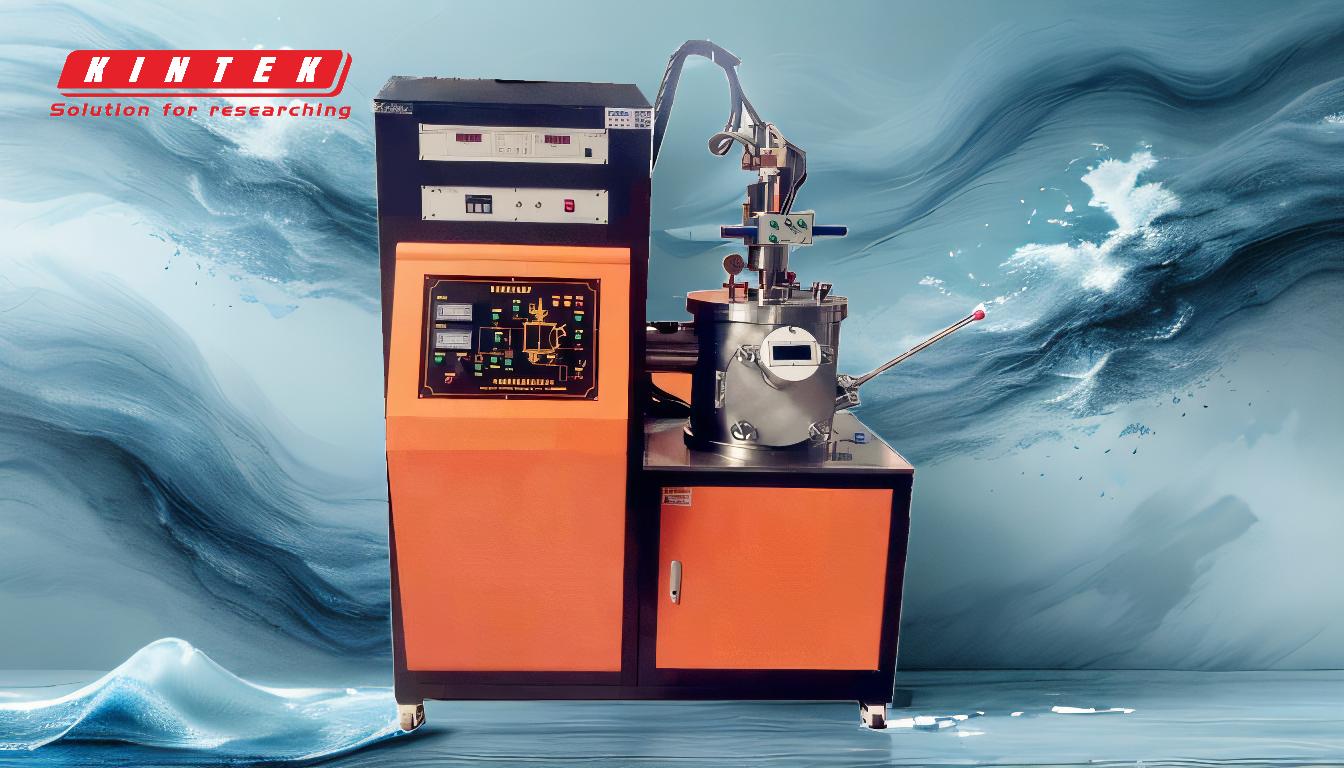
-
Definition of Melting Loss:
- Melting loss refers to the reduction in metal weight during the melting process in an induction furnace. This loss occurs due to oxidation, evaporation, and slag formation, which are inherent to the melting process.
-
Factors Influencing Melting Loss:
- Melting Rate and Power Configuration: The melting rate, calculated as (Power in kW) / (Standard power consumption in kWh/ton), directly impacts melting loss. Higher power configurations can reduce melting time but may increase oxidation and evaporation if not controlled.
- Charge Cleanliness and Size: A clean charge with minimal impurities reduces slag formation and oxidation, thereby minimizing melting loss. The size of the charge also affects the uniformity of melting and heat distribution.
- Refractory Materials and Crucibles: The type of refractory materials and crucibles used, such as quartz crucibles, plays a significant role in reducing heat transfer loss and improving overall efficiency.
- Furnace Design and Lining: Proper furnace lining dimensions and sufficient refractory material prevent overheating and damage to the coil, which can otherwise lead to increased melting loss.
-
Overheating and Its Impact:
- Overheating of the furnace coil, caused by restrictions in the water flow path or improper furnace design, can lead to increased melting loss. Overheating accelerates oxidation and evaporation, contributing to higher material waste.
-
Calculation of Melting Rate and Time:
- The melting rate is calculated using the formula: (Power in kW) / (Standard power consumption in kWh/ton) = (Weight of the metal in kg) / (1000 kg). For example, at 325 kW, the melting rate is 520 kg/hour.
- The melting time is calculated using the formula: (Power in kW * Time in hours) / (Weight of the metal in kg) = (Standard power consumption in kWh/ton * 1 hour) / (1000 kg). For a 550 kg furnace with a 325 kW power supply, the melting time is 1.06 hours (64 minutes).
-
Optimization Strategies:
- Clean Charge: Ensuring the charge is free from impurities and contaminants reduces slag formation and oxidation.
- Proper Furnace Design: Maintaining appropriate furnace block length and lining dimensions prevents overheating and improves efficiency.
- Suitable Crucibles: Using crucibles like quartz crucibles reduces heat transfer loss and enhances melting efficiency.
- Regular Maintenance: Regularly inspecting and maintaining water flow paths, heat exchangers, and power cables prevents overheating and ensures consistent performance.
By understanding and addressing these factors, operators can minimize melting loss, improve furnace efficiency, and reduce material waste in induction furnace operations.
Summary Table:
Key Factor | Impact on Melting Loss |
---|---|
Melting Rate & Power | Higher power reduces melting time but may increase oxidation and evaporation. |
Charge Cleanliness & Size | Clean charges minimize slag formation and oxidation, reducing melting loss. |
Refractory Materials | Suitable materials like quartz crucibles reduce heat transfer loss and improve efficiency. |
Furnace Design & Lining | Proper dimensions prevent overheating and coil damage, reducing material waste. |
Overheating | Overheating accelerates oxidation and evaporation, increasing melting loss. |
Optimize your induction furnace operations and reduce melting loss—contact our experts today for tailored solutions!