Ceramic dental implants are known for their biocompatibility, aesthetic appeal, and durability. However, like all medical devices, they are not immune to failure. The most common mode of failure associated with ceramic dental implants is fracture. This can occur due to mechanical stress, material defects, or improper placement. Understanding the causes and mechanisms of fracture is crucial for improving implant design and clinical outcomes.
Key Points Explained:
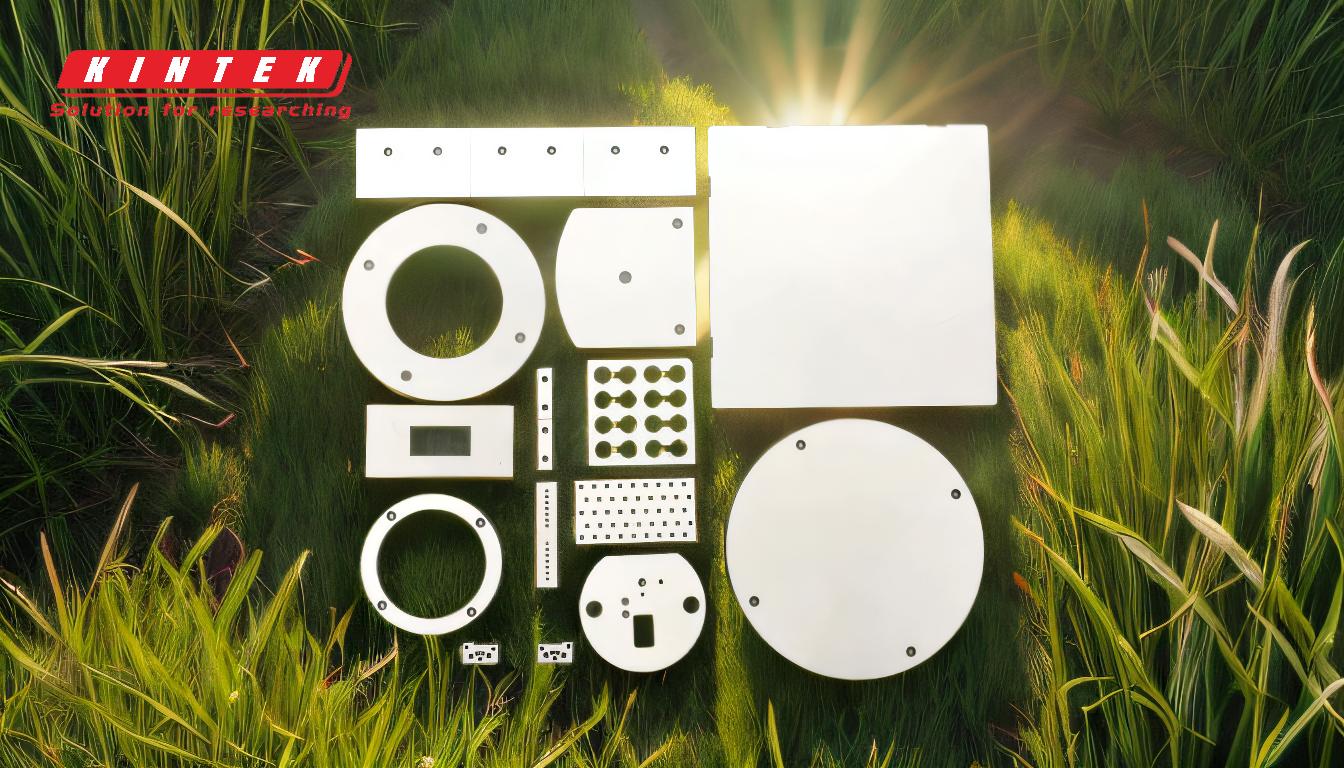
-
Fracture as the Primary Mode of Failure:
- Ceramic dental implants are prone to fracture due to their brittle nature. Unlike metals, ceramics do not deform plastically under stress, making them more susceptible to cracking.
- Fractures can occur during insertion, under functional loading, or due to trauma. The high stresses encountered during chewing or grinding can exceed the material's strength, leading to catastrophic failure.
-
Causes of Fracture:
- Mechanical Stress: Excessive occlusal forces or improper loading can lead to stress concentrations, causing cracks to initiate and propagate.
- Material Defects: Microcracks or impurities in the ceramic material can act as stress concentrators, reducing the overall strength of the implant.
- Improper Placement: Misalignment or inadequate bone support can lead to uneven stress distribution, increasing the risk of fracture.
-
Types of Fractures:
- Complete Fracture: The implant breaks into two or more pieces, rendering it non-functional.
- Partial Fracture: Cracks or chips may form on the surface or within the implant, compromising its structural integrity over time.
-
Prevention and Mitigation:
- Material Selection: Using advanced ceramics with higher fracture toughness, such as zirconia, can reduce the risk of failure.
- Design Optimization: Implants should be designed to distribute stress evenly and minimize stress concentrations.
- Proper Placement: Ensuring accurate placement and adequate bone support can help prevent uneven loading and subsequent fracture.
-
Clinical Implications:
- Fracture of ceramic dental implants can lead to significant clinical challenges, including the need for implant removal and replacement.
- Long-term studies and improved manufacturing techniques are essential to enhance the reliability and longevity of ceramic dental implants.
In conclusion, while ceramic dental implants offer numerous advantages, their susceptibility to fracture remains a critical concern. Addressing this issue through material innovation, design improvements, and meticulous clinical practices is essential for their continued success in dental applications.
Summary Table:
Aspect | Details |
---|---|
Primary Failure Mode | Fracture due to brittle nature of ceramics |
Causes of Fracture | Mechanical stress, material defects, improper placement |
Types of Fractures | Complete fracture (breaks into pieces), partial fracture (cracks or chips) |
Prevention Strategies | Advanced materials (e.g., zirconia), design optimization, proper placement |
Clinical Implications | Implant removal/replacement, need for long-term studies and improvements |
Concerned about ceramic dental implant fractures? Contact our experts for insights on prevention and solutions!