The most common method used for the synthesis of nanomaterials depends on the type of nanomaterial being produced. For general nanomaterials, traditional chemical synthesis methods such as hydrothermal and sol-gel methods are widely used. These methods are favored for their simplicity, scalability, and ability to produce a variety of nanostructures. For carbon-based nanomaterials, techniques like chemical vapor deposition (CVD), laser ablation, and arc-discharge are more prevalent due to their precision and ability to produce high-quality carbon nanostructures like graphene and carbon nanotubes. Each method has its unique advantages and is chosen based on the desired properties and applications of the nanomaterial.
Key Points Explained:
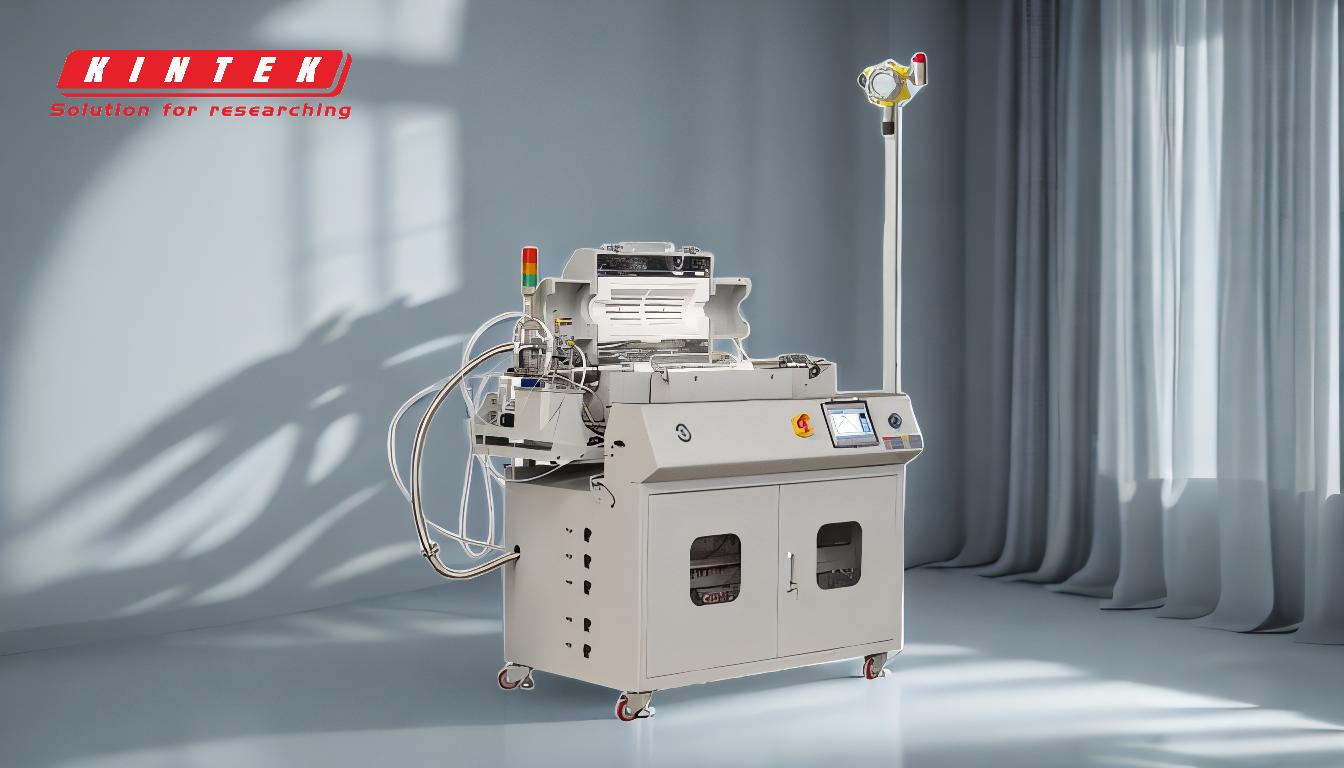
-
Traditional Chemical Synthesis Methods:
-
Hydrothermal Method:
- This method involves the use of high-temperature and high-pressure water to facilitate the synthesis of nanomaterials.
- It is particularly useful for producing metal oxides, hydroxides, and other inorganic nanomaterials.
- The process allows for the control of particle size and morphology by adjusting parameters like temperature, pressure, and reaction time.
-
Sol-Gel Method:
- This technique involves the transition of a system from a liquid "sol" into a solid "gel" phase.
- It is widely used for the synthesis of metal oxides and hybrid organic-inorganic materials.
- The sol-gel process offers excellent control over the composition and homogeneity of the nanomaterials.
-
Hydrothermal Method:
-
Synthesis of Carbon Nanomaterials:
-
Chemical Vapor Deposition (CVD):
- CVD is a widely used method for synthesizing carbon nanomaterials such as graphene and carbon nanotubes.
- It involves the decomposition of a carbon-containing gas on a substrate at high temperatures.
- CVD allows for the production of high-quality, large-area graphene and aligned carbon nanotubes.
-
Laser Ablation:
- This technique uses a high-power laser to vaporize a carbon target in the presence of an inert gas.
- It is suitable for producing carbon nanotubes and other carbon-based nanostructures.
- The method offers good control over the size and structure of the nanomaterials.
-
Arc-Discharge:
- Arc-discharge involves the use of an electric arc to vaporize carbon in a controlled environment.
- It is commonly used for the synthesis of carbon nanotubes and fullerenes.
- The process can produce high-quality nanomaterials but often requires post-synthesis purification.
-
Chemical Vapor Deposition (CVD):
-
Advantages and Applications:
-
Hydrothermal and Sol-Gel Methods:
- These methods are cost-effective and scalable, making them suitable for industrial applications.
- They are used in the production of catalysts, sensors, and energy storage materials.
-
CVD, Laser Ablation, and Arc-Discharge:
- These techniques are preferred for producing high-performance carbon nanomaterials used in electronics, composites, and energy applications.
- They offer precise control over the nanostructure, which is critical for applications requiring specific electrical, thermal, or mechanical properties.
-
Hydrothermal and Sol-Gel Methods:
-
Selection Criteria for Synthesis Methods:
- The choice of synthesis method depends on the type of nanomaterial, desired properties, and intended application.
- Factors such as cost, scalability, and the need for post-synthesis processing also play a significant role in determining the most suitable method.
In summary, while hydrothermal and sol-gel methods are common for general nanomaterials, CVD, laser ablation, and arc-discharge are more prevalent for carbon nanomaterials. Each method has its own set of advantages and is chosen based on the specific requirements of the nanomaterial being synthesized.
Summary Table:
Method | Type of Nanomaterial | Key Advantages | Applications |
---|---|---|---|
Hydrothermal | General Nanomaterials | High-temperature and high-pressure water; control over particle size and morphology | Catalysts, sensors, energy storage materials |
Sol-Gel | General Nanomaterials | Transition from liquid to solid; excellent control over composition and homogeneity | Metal oxides, hybrid organic-inorganic materials |
Chemical Vapor Deposition (CVD) | Carbon Nanomaterials | Decomposition of carbon-containing gas; produces high-quality graphene and nanotubes | Electronics, composites, energy applications |
Laser Ablation | Carbon Nanomaterials | Vaporizes carbon target; good control over size and structure | Carbon nanotubes, other carbon-based nanostructures |
Arc-Discharge | Carbon Nanomaterials | Electric arc vaporizes carbon; produces high-quality nanomaterials | Carbon nanotubes, fullerenes (requires post-synthesis purification) |
Need help selecting the right nanomaterial synthesis method? Contact our experts today for tailored solutions!