Preheating before welding is a critical step, especially when working with materials like cast iron, to ensure the integrity and strength of the weld. The most important part of preheating is controlling the thermal gradient to minimize tensile stress, which can lead to cracking. By reducing the temperature difference between the heat-affected zone (HAZ) and the base material, preheating helps prevent thermal shock and ensures a more uniform cooling process. This is particularly crucial in higher temperature welding methods, where the preheat temperature must be carefully managed to match the welding process and material properties.
Key Points Explained:
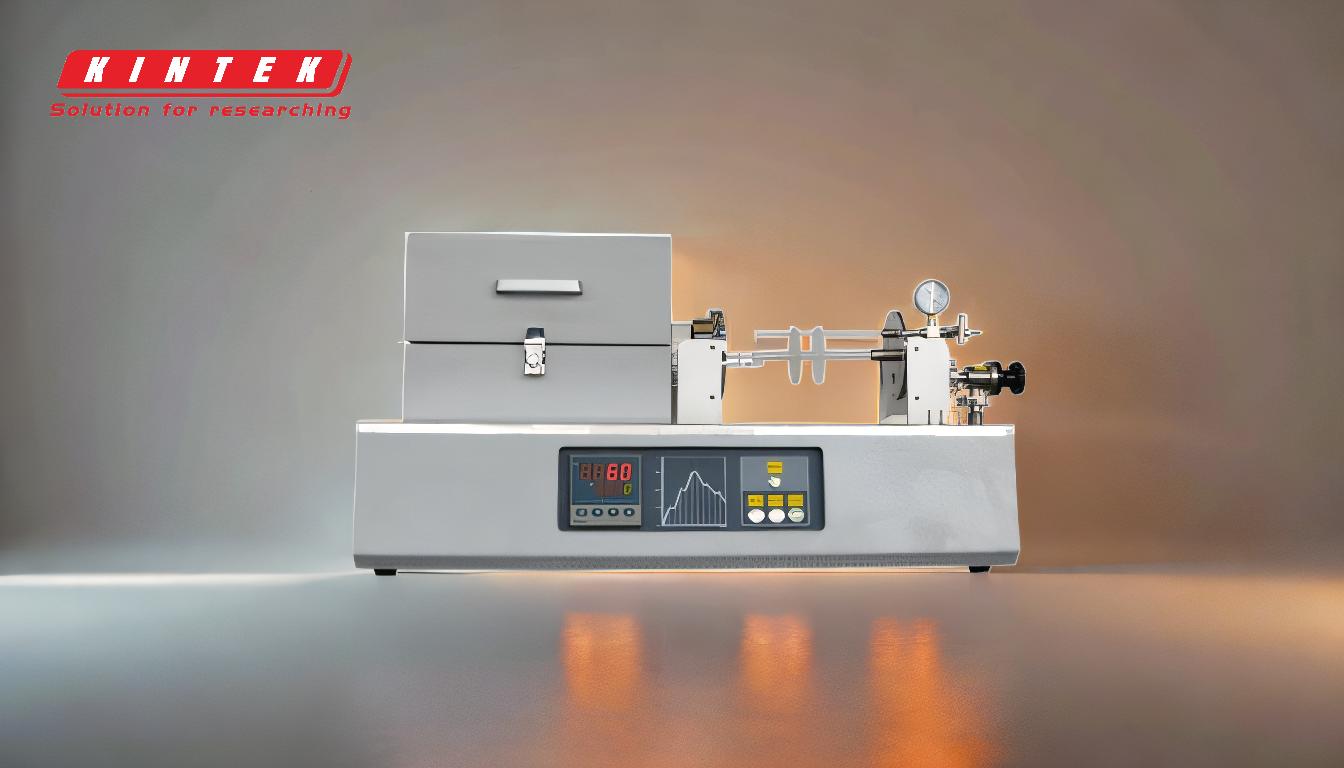
-
Minimizing Tensile Stress:
- Preheating reduces the risk of tensile stress caused by thermal expansion and contraction during welding. This is especially important for materials like cast iron, which are prone to cracking under stress.
- By heating the material before welding, the thermal gradient between the weld area and the surrounding material is reduced, preventing sudden temperature changes that can lead to cracking.
-
Controlling the Thermal Gradient:
- The thermal gradient refers to the rate of temperature change across the material. A steep gradient can cause uneven expansion and contraction, leading to stress and potential cracks.
- Preheating helps to create a more uniform temperature distribution, reducing the thermal gradient and ensuring a smoother cooling process after welding.
-
Preventing Cracking:
- Cracking is a common issue in welding, particularly with brittle materials like cast iron. Preheating helps to prevent cracking by reducing the thermal stress and ensuring a more gradual cooling process.
- The heat-affected zone (HAZ) is particularly vulnerable to cracking, and preheating helps to minimize the stress in this area by maintaining a more consistent temperature.
-
Matching Preheat Temperature to Welding Method:
- Different welding methods require different preheat temperatures. Higher temperature welding methods, such as those used for thick or high-strength materials, require higher preheat temperatures to ensure proper weld quality.
- It's important to match the preheat temperature to the specific welding process and material being used to achieve the best results.
-
Ensuring Uniform Cooling:
- After welding, the material needs to cool down uniformly to avoid residual stresses that can weaken the weld. Preheating helps to ensure that the cooling process is gradual and even, reducing the risk of post-weld cracking.
- This is particularly important for large or complex welds, where uneven cooling can lead to significant stress concentrations.
In summary, the most important part of preheating before welding is controlling the thermal gradient to minimize tensile stress and prevent cracking. This involves carefully managing the preheat temperature, ensuring uniform heating and cooling, and matching the preheat conditions to the specific welding method and material properties. By doing so, you can achieve a stronger, more reliable weld with reduced risk of failure.
Summary Table:
Key Aspect | Description |
---|---|
Minimizing Tensile Stress | Reduces risk of cracking by lowering thermal expansion and contraction stress. |
Controlling Thermal Gradient | Ensures uniform temperature distribution, preventing sudden temperature changes. |
Preventing Cracking | Reduces thermal stress in the heat-affected zone (HAZ) for brittle materials. |
Matching Preheat Temperature | Aligns preheat conditions with welding methods and material properties. |
Ensuring Uniform Cooling | Promotes gradual cooling to avoid residual stresses and post-weld cracking. |
Need expert advice on preheating for welding? Contact us today to ensure flawless results!