The most suitable temperature for burning cement in a rotary kiln typically ranges between 1400°C to 1500°C. This temperature range ensures the proper formation of clinker, which is the intermediate product in cement manufacturing. Below this range, the chemical reactions required for clinker formation may be incomplete, while temperatures above this range can lead to excessive energy consumption and potential damage to the kiln lining. The process involves heating raw materials (limestone, clay, and other additives) to this temperature range to facilitate the chemical reactions that produce cement clinker.
Key Points Explained:
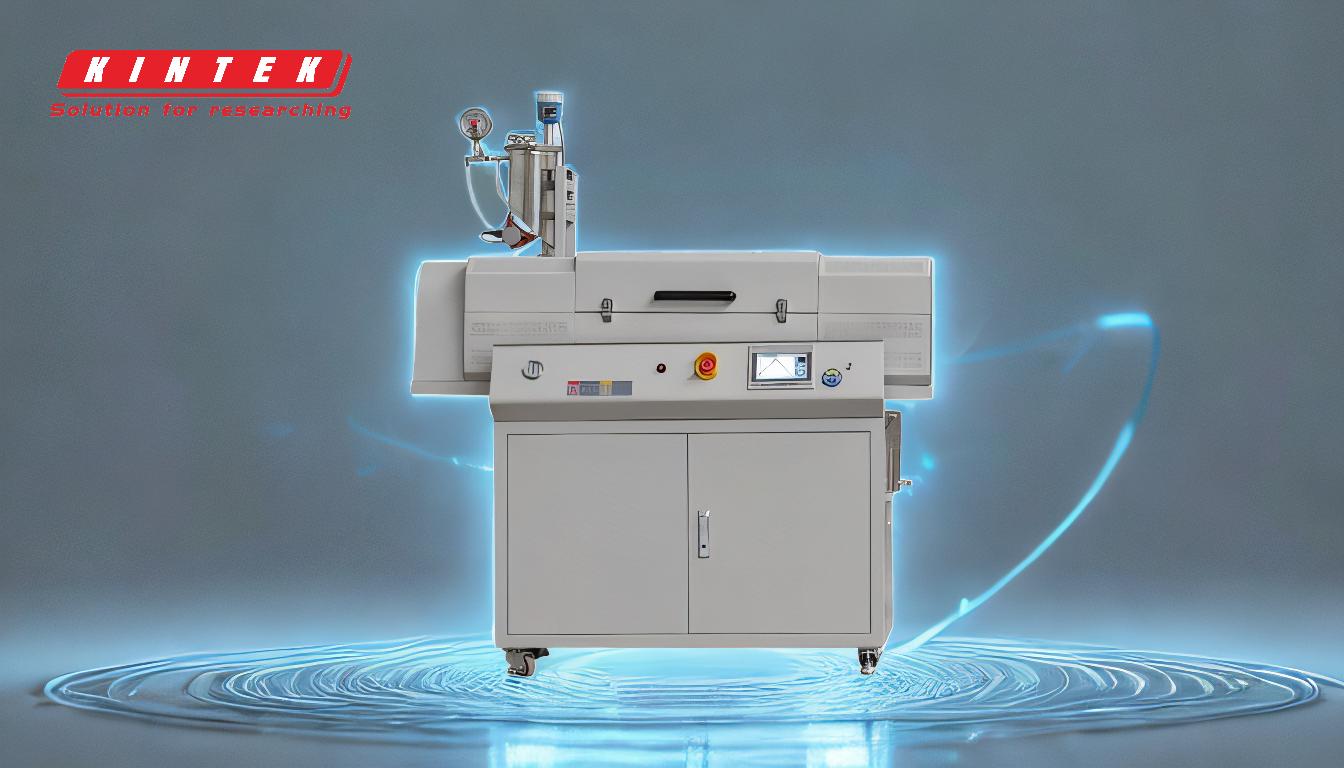
-
Optimal Temperature Range for Cement Burning:
- The ideal temperature range for burning cement in a rotary kiln is 1400°C to 1500°C. This range is critical for the formation of clinker, which is the primary component of cement.
- At this temperature, the raw materials undergo a series of chemical reactions, including calcination (decomposition of limestone into lime) and sintering (formation of clinker compounds like alite and belite).
-
Why 1400°C to 1500°C is Suitable:
- Chemical Reactions: At temperatures below 1400°C, the chemical reactions required for clinker formation may not proceed to completion, leading to poor-quality clinker. Above 1500°C, the reactions may become too intense, causing over-burning and energy inefficiency.
- Energy Efficiency: Maintaining the temperature within this range ensures efficient energy use. Excessive temperatures lead to higher fuel consumption and increased operational costs.
- Kiln Lining Protection: Prolonged exposure to temperatures above 1500°C can damage the refractory lining of the kiln, reducing its lifespan and increasing maintenance costs.
-
Comparison with Other Kiln Types:
- Indirect Rotary Kilns: These kilns typically operate at lower temperatures (1200-1300°C for the furnace tube and less than 1150°C for the material). They are not suitable for cement production as they cannot reach the temperatures required for clinker formation.
- Electric Rotary Kilns: With a maximum working temperature of 1100°C, electric rotary kilns are also unsuitable for cement production due to their inability to reach the necessary clinker formation temperatures.
-
Factors Influencing Temperature Selection:
- Raw Material Composition: The chemical composition of the raw materials can influence the required burning temperature. For example, raw materials with higher silica content may require slightly higher temperatures.
- Kiln Design: The design of the rotary kiln, including its length, diameter, and refractory lining, can affect the temperature distribution and the efficiency of heat transfer.
- Fuel Type: The type of fuel used (e.g., coal, natural gas, or alternative fuels) can influence the combustion temperature and, consequently, the overall kiln temperature.
-
Practical Considerations:
- Temperature Control: Precise temperature control is essential to maintain the optimal burning conditions. This is typically achieved through advanced control systems that monitor and adjust the fuel and air supply.
- Cooling Process: After the clinker is formed, it must be rapidly cooled to preserve its quality. This is usually done in a cooler attached to the kiln, where the clinker is cooled from around 1400°C to below 200°C.
-
Impact of Temperature on Cement Quality:
- Clinker Quality: The temperature directly affects the quality of the clinker, which in turn influences the strength and durability of the final cement product.
- Energy Consumption: Operating within the optimal temperature range minimizes energy consumption, making the process more cost-effective and environmentally friendly.
- Environmental Considerations: Maintaining the correct temperature helps reduce emissions of pollutants such as nitrogen oxides (NOx) and sulfur dioxide (SO2), which are byproducts of high-temperature combustion.
In summary, the most suitable temperature for burning cement in a rotary kiln is between 1400°C and 1500°C. This range ensures efficient clinker formation, energy efficiency, and protection of the kiln lining, while also contributing to the production of high-quality cement.
Summary Table:
Aspect | Details |
---|---|
Optimal Temperature | 1400°C to 1500°C |
Purpose | Ensures proper clinker formation and energy efficiency |
Chemical Reactions | Calcination and sintering occur at this range |
Energy Efficiency | Minimizes fuel consumption and operational costs |
Kiln Lining Protection | Prevents damage to refractory lining |
Cement Quality | High-quality clinker leads to durable and strong cement |
Environmental Impact | Reduces emissions of NOx and SO2 |
Need expert advice on optimizing your rotary kiln for cement production? Contact us today to learn more!