The muffle furnace method involves using a specialized high-temperature oven, known as a muffle furnace, to heat materials in a controlled environment. This method is widely used in industries and research fields for applications such as heat treatment, ashing, sintering, and material analysis. The furnace isolates the sample from direct contact with combustion byproducts, ensuring accurate and contamination-free results. It operates on the principles of convection and radiation, with precise temperature control achieved through heating elements and refractory insulation. The method is versatile, catering to fields like metallurgy, ceramics, electronics, and environmental analysis, making it a critical tool for high-temperature processing and experimentation.
Key Points Explained:
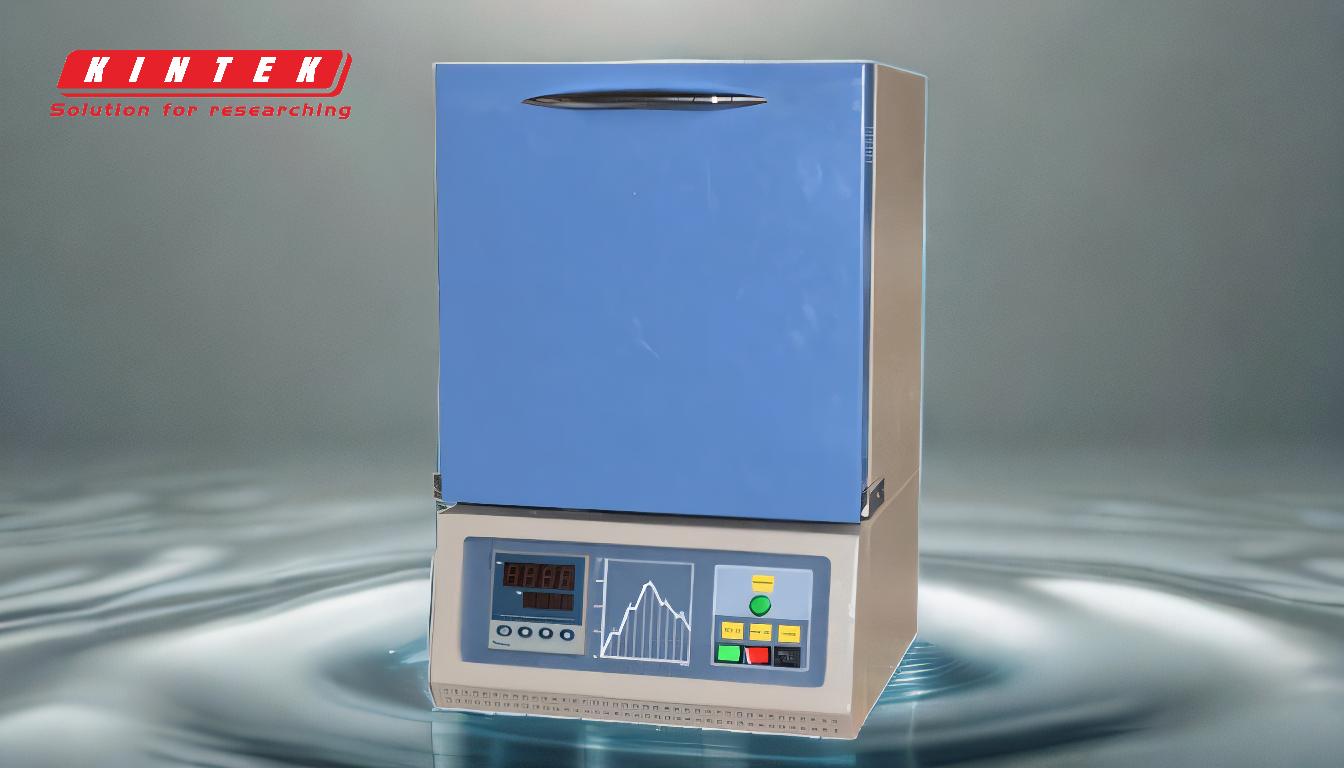
-
Definition and Purpose of Muffle Furnace:
- A muffle furnace is a high-temperature oven designed to heat materials in an isolated environment, preventing contamination from combustion byproducts.
- It is used for applications such as heat treatment, ashing, sintering, and material analysis, ensuring precise and controlled heating.
-
Working Principle:
- The furnace operates on the principles of convection and radiation.
- Heating elements, often made of materials like Nichrome, heat the walls of the muffle chamber, which is constructed from refractory materials to minimize heat loss.
- Temperature control is achieved by adjusting the power supplied to the heating elements, with some models featuring built-in controllers for enhanced precision.
-
Applications:
- Heat Treatment: Used for processes like annealing, quenching, and normalizing metals.
- Material Analysis: Determines moisture, ash, volatile content, and ash melting points.
- Sintering and Calcination: Essential for ceramics, metals, and other materials requiring high-temperature processing.
- Environmental and Medical Testing: Applied in water quality analysis, drug testing, and medical sample pretreatment.
-
Key Features:
- Isolation from Contaminants: The muffle design ensures that samples are not exposed to combustion byproducts, making it ideal for sensitive applications.
- Versatility: Suitable for a wide range of industries, including ceramics, metallurgy, electronics, and chemical research.
- Temperature Precision: Advanced models offer precise temperature control, critical for experiments requiring exact thermal conditions.
-
Industries and Fields of Use:
- Scientific Research: Used in universities and research institutes for high-temperature experiments and material studies.
- Industrial Applications: Employed in metallurgy, ceramics, glass manufacturing, and chemical industries for processes like powder roasting and sintering.
- Quality Control: Essential for industries requiring rigorous material testing and analysis.
-
Advantages:
- Contamination-Free Heating: The isolation of samples ensures accurate results, free from external impurities.
- High-Temperature Capability: Capable of reaching temperatures necessary for advanced material processing.
- Durability: Constructed with refractory materials, muffle furnaces are built to withstand extreme conditions.
-
Limitations:
- Energy Consumption: High-temperature operations can be energy-intensive.
- Cost: Advanced models with precise temperature control and additional features can be expensive.
- Maintenance: Regular maintenance is required to ensure optimal performance and longevity.
By understanding the muffle furnace method, purchasers can make informed decisions about its suitability for their specific applications, ensuring efficient and accurate high-temperature processing.
Summary Table:
Aspect | Details |
---|---|
Definition | High-temperature oven for isolated, contamination-free heating. |
Working Principle | Operates via convection and radiation with precise temperature control. |
Applications | Heat treatment, material analysis, sintering, environmental testing. |
Key Features | Isolation from contaminants, versatility, precise temperature control. |
Industries | Metallurgy, ceramics, electronics, scientific research, quality control. |
Advantages | Contamination-free, high-temperature capability, durability. |
Limitations | Energy-intensive, high cost, requires regular maintenance. |
Discover how the muffle furnace method can enhance your processes—contact our experts today!