Pyrolysis is a thermal decomposition process that breaks down materials at high temperatures in the absence of oxygen. The order of the pyrolysis reaction is typically first-order, meaning the rate of reaction depends on the concentration of the material being pyrolyzed. This process is influenced by factors such as temperature, residence time, heating rate, and the composition of the material. Different types of pyrolysis—slow, fast, and flash—vary in their heating rates, temperatures, and residence times, leading to different product distributions. The process is characterized by the rupture of carbon-carbon bonds and the formation of carbon-oxygen bonds, with temperatures ranging from 400–550°C or higher. The products of pyrolysis include gases, liquids (bio-oil), and solid char, with their distribution heavily dependent on process conditions and material properties.
Key Points Explained:
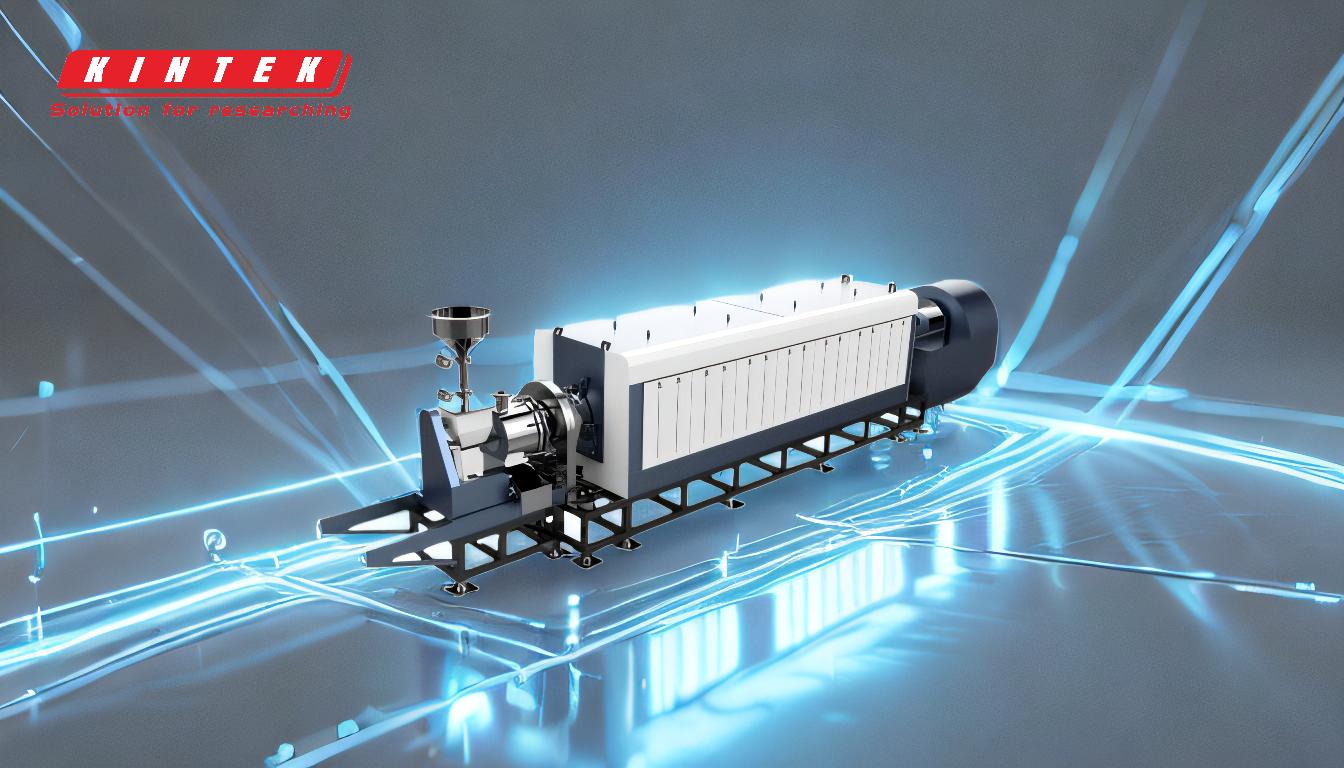
-
Order of the Pyrolysis Reaction:
- Pyrolysis is a first-order reaction, meaning the rate of reaction is directly proportional to the concentration of the material being decomposed. This implies that as the material concentration decreases over time, the reaction rate also decreases.
-
Types of Pyrolysis:
- Slow Pyrolysis: Characterized by low heating rates, longer residence times, and lower temperatures. This type favors the production of solid char.
- Fast Pyrolysis: Involves high heating rates, short residence times, and moderate temperatures. It primarily produces bio-oil.
- Flash Pyrolysis: Similar to fast pyrolysis but conducted at even higher heating rates, resulting in very high bio-oil yields (up to 75–80 wt%).
-
Factors Influencing Pyrolysis:
- Temperature: Higher temperatures generally increase the production of non-condensable gases, while lower temperatures favor solid char and bio-oil.
- Residence Time: Longer residence times can lead to more complete thermal conversion but may also reduce the yield of desired products like bio-oil.
- Heating Rate: Faster heating rates promote the formation of bio-oil, while slower rates favor char production.
- Material Composition: Different components of biomass or waste decompose at different temperatures, affecting the overall product distribution.
- Particle Size: Smaller particles decompose more quickly, leading to higher yields of pyrolysis oil.
-
Mechanism of Pyrolysis:
- Pyrolysis involves the thermal degradation of solid fuels, primarily through the rupture of carbon-carbon bonds and the formation of carbon-oxygen bonds. This process typically occurs at temperatures between 400–550°C, although higher temperatures can also be used.
- During pyrolysis, part of the biomass is reduced to carbon (char), while the remaining part is oxidized and hydrolyzed to form various compounds, including gases and liquids.
-
Product Distribution:
- The distribution of pyrolysis products (gases, liquids, and solids) is influenced by several factors:
- Heating Rate: Faster heating rates increase bio-oil yields.
- Final Temperature: Higher temperatures favor gas production.
- Composition of Raw Material: Different materials yield different product distributions.
- Pressure: Higher pressures can influence the types of products formed.
- The distribution of pyrolysis products (gases, liquids, and solids) is influenced by several factors:
-
High-Temperature Pyrolysis Factors:
- In high-temperature pyrolysis, additional factors such as pressure, time, atmosphere, and feed rate play significant roles in determining the reaction kinetics and product distribution.
-
Ablative Pyrolysis:
- In ablative pyrolysis, the rate of reaction is influenced by:
- Pressure on the Particle: Higher pressure can increase the rate of decomposition.
- Relative Velocity of Wood on the Heat Exchange Surface: Faster relative velocities can enhance heat transfer and reaction rates.
- Reactor Surface Temperature: Higher surface temperatures accelerate the pyrolysis process.
- In ablative pyrolysis, the rate of reaction is influenced by:
-
Applications of Pyrolysis:
- Pyrolysis is used in various fields, including waste management, biofuel production, and chemical synthesis. The specific application depends on the temperature and conditions of the pyrolysis process.
By understanding these key points, one can better control and optimize the pyrolysis process to achieve desired product distributions, whether the goal is to maximize bio-oil, char, or gas production.
Summary Table:
Aspect | Details |
---|---|
Reaction Order | First-order reaction, rate depends on material concentration |
Types of Pyrolysis | Slow (char), Fast (bio-oil), Flash (high bio-oil yields) |
Key Factors | Temperature, residence time, heating rate, material composition, particle size |
Mechanism | Rupture of carbon-carbon bonds, formation of carbon-oxygen bonds (400–550°C) |
Products | Gases, bio-oil, solid char |
Applications | Waste management, biofuel production, chemical synthesis |
Optimize your pyrolysis process for maximum efficiency—contact our experts today!