An induction furnace is a highly efficient and versatile piece of equipment used primarily for melting metals. Its output is influenced by several factors, including the design of the furnace, the type of power supply, and the materials being processed. The key characteristics of an induction furnace, such as its main control board, medium frequency power supply, and comprehensive protection systems, play a crucial role in determining its performance and output. The furnace's ability to start smoothly, maintain constant power, and adjust automatically based on the furnace charge ensures that it operates efficiently and reliably. Below, we will explore the key points that define the output of an induction furnace, particularly focusing on the role of the IGBT induction furnace in achieving these outputs.
Key Points Explained:
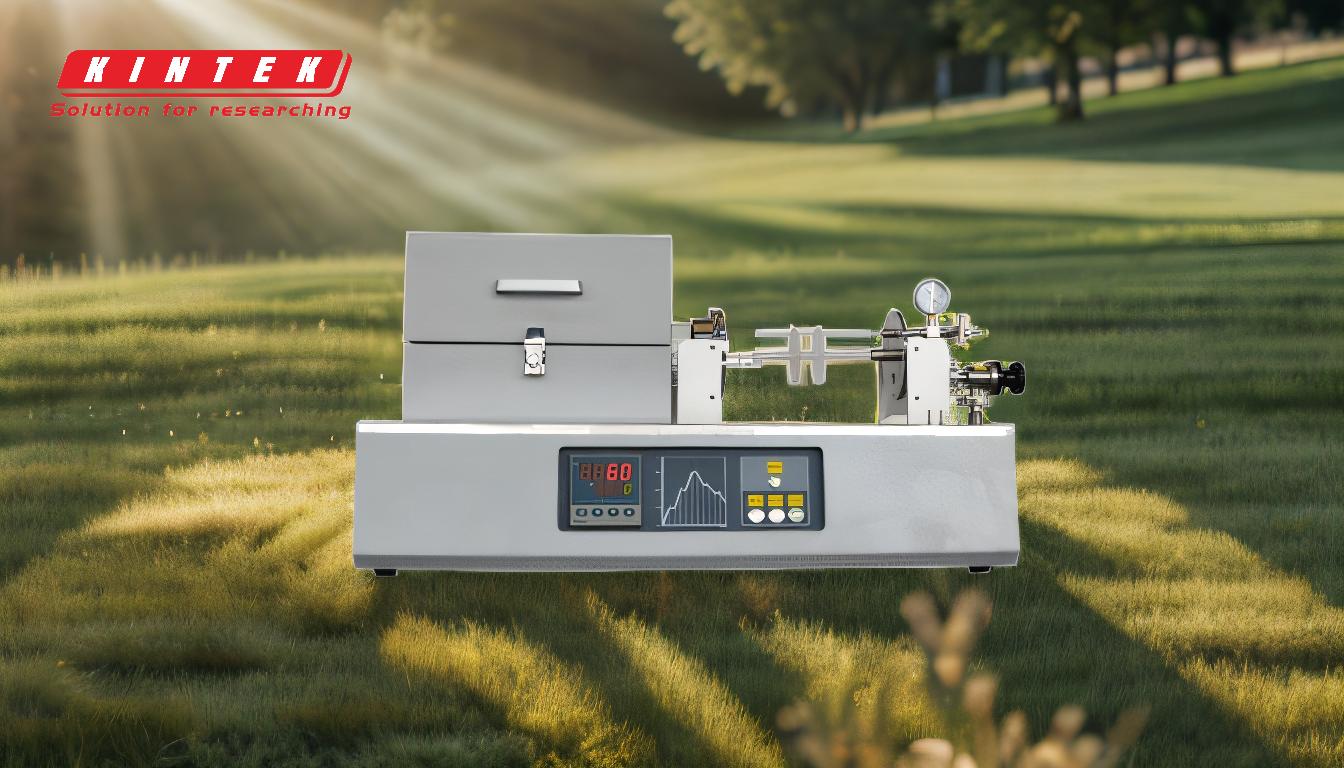
-
Main Control Board and Stability:
- The main control board in an induction furnace is optimized using large-scale integrated circuits, which ensures stable performance and strong anti-interference capabilities. This stability is crucial for maintaining consistent output, especially in environments where electrical noise or fluctuations might otherwise disrupt operations.
-
Medium Frequency Power Supply:
- The medium frequency power supply cabinet is well-coordinated with components like AC contactors, silicon-controlled rectifiers, and inverter boards. This coordination not only makes the furnace easier to maintain but also ensures that the power supply is consistent and reliable, which directly impacts the furnace's output efficiency.
-
Automatic Frequency Scanning and Repeated Starting:
- The main control circuit board features automatic frequency scanning and repeated starting functions. These features ensure that the furnace operates smoothly and stably, even under varying load conditions. This is particularly important for maintaining a consistent output when melting different types of metals or when the furnace charge changes.
-
High-Sensitivity Trigger Circuit:
- The induction furnace is equipped with a high-sensitivity trigger circuit for inverter starting, which achieves a 100% start-up success rate. This reliability in starting ensures that the furnace can begin operations without delays or failures, contributing to overall output efficiency.
-
Constant Power Circuit Control:
- The constant power circuit control system adjusts the voltage and current automatically based on the furnace charge. This automatic adjustment ensures that the furnace operates at optimal power levels, which is essential for achieving the desired output in terms of both quantity and quality of the melted metal.
-
Comprehensive Protection Systems:
- The furnace includes comprehensive protection systems for over-voltage, over-current, under-voltage, and other conditions. These systems ensure that the furnace operates safely and reliably, minimizing downtime and maximizing output. The protection systems also help in preventing damage to the furnace, which could otherwise lead to costly repairs and reduced output.
-
High Integrated Circuit Design:
- The high integrated circuit design simplifies debugging, operation, and learning processes. This ease of use ensures that the furnace can be operated efficiently by personnel with varying levels of expertise, which in turn contributes to consistent and reliable output.
-
Zero Voltage Startup:
- The induction furnace features a zero voltage startup that begins gently, with high initial power and minimal impact on the electric network. This gentle startup not only reduces wear and tear on the furnace components but also ensures that the furnace can achieve high output levels quickly and efficiently.
In summary, the output of an induction furnace is determined by a combination of advanced technological features and robust design elements. The IGBT induction furnace plays a pivotal role in ensuring that these features work harmoniously to deliver consistent, high-quality output. From the main control board to the comprehensive protection systems, each component is designed to optimize performance and reliability, making the induction furnace a highly effective tool for metal melting and processing.
Summary Table:
Key Factor | Impact on Output |
---|---|
Main Control Board | Ensures stable performance and anti-interference for consistent output. |
Medium Frequency Power Supply | Provides reliable and consistent power, enhancing efficiency. |
Automatic Frequency Scanning | Maintains smooth operation under varying load conditions. |
High-Sensitivity Trigger Circuit | Achieves 100% startup success, reducing delays and improving output. |
Constant Power Circuit Control | Adjusts voltage and current automatically for optimal power levels. |
Comprehensive Protection Systems | Minimizes downtime and prevents damage, ensuring reliable output. |
High Integrated Circuit Design | Simplifies operation, making it easier to achieve consistent output. |
Zero Voltage Startup | Reduces wear and tear while enabling quick, high-output operations. |
Ready to optimize your metal melting process? Contact us today to learn more about our advanced induction furnaces!