A muffle furnace serves as a critical tool in high-temperature applications, particularly in industrial and laboratory settings. Its primary purpose is to provide a controlled, isolated environment for heating materials to extreme temperatures, often up to 1400°C, without contamination from combustion byproducts. This is achieved through its unique design, which includes a ceramic or refractory-lined chamber that acts as a "muffle," insulating the heating process and ensuring efficient heat retention. The furnace operates using electrical heating elements, often controlled by advanced systems like PID controllers, to maintain precise temperature regulation. Applications range from fusing glass and heat-treating metals to conducting high-temperature chemical reactions and ashing samples. The muffle furnace's ability to separate the material being heated from external contaminants and its energy-efficient design make it indispensable for processes requiring high temperatures and controlled environments.
Key Points Explained:
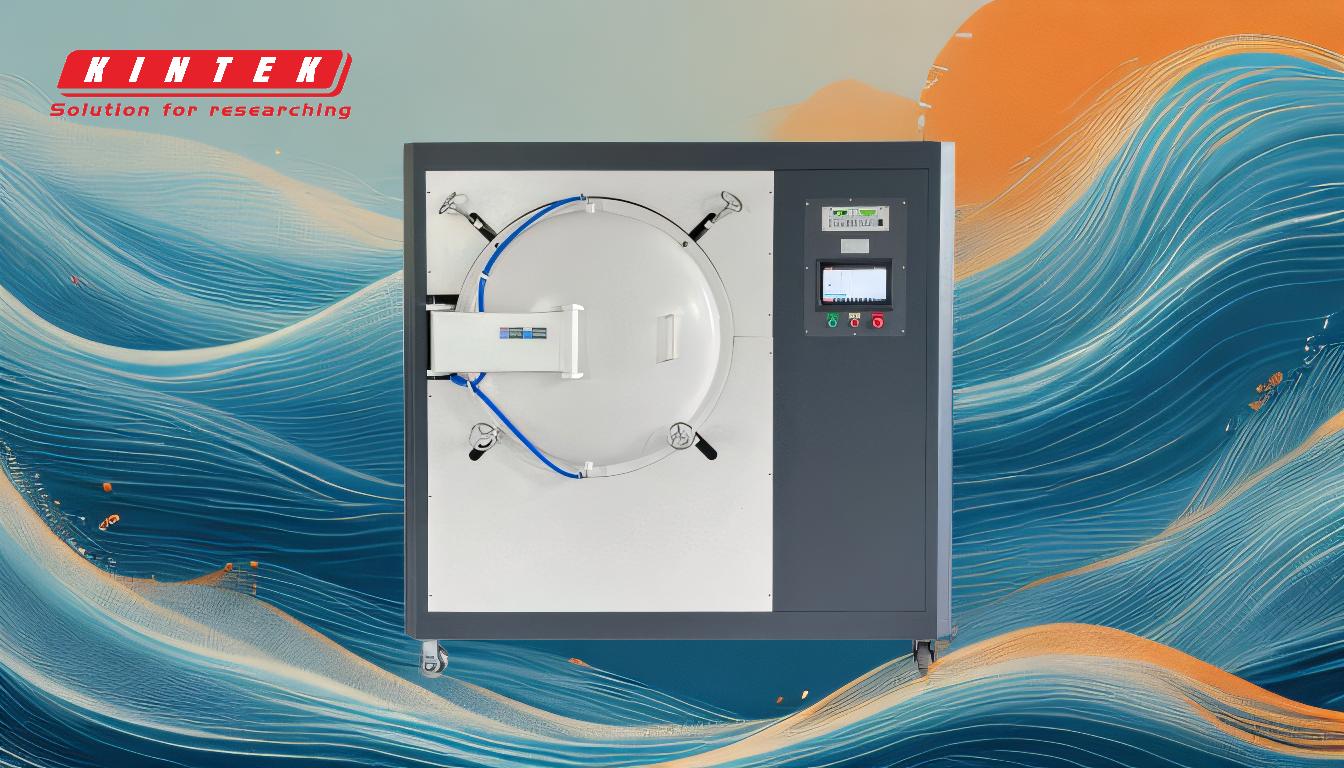
1. Purpose of a Muffle Furnace
- Isolation of Materials: The muffle furnace creates a closed chamber where materials can be heated without exposure to combustion byproducts, ensuring purity and preventing contamination.
- High-Temperature Applications: It is designed to reach and maintain temperatures up to 1400°C, making it suitable for processes like fusing glass, brazing, and heat-treating metals.
- Controlled Environment: The furnace provides a controlled environment for high-temperature chemical reactions, such as solid-state reactions, metal reduction, and chemical vapor deposition (CVD).
2. Design and Construction
- Ceramic or Refractory Lining: The chamber is lined with materials like ceramic fiber or refractory bricks, which act as insulators to minimize heat loss and ensure durability under extreme conditions.
- Heating Elements: Modern muffle furnaces use electrical heating elements made of materials like Nichrome, which generate heat through resistance heating. These elements are located outside the chamber to heat its walls indirectly.
- Insulation Box: The furnace includes an insulation box that surrounds the heating chamber, further enhancing heat retention and energy efficiency.
3. Working Principles
- Convection and Radiation: Heat is transferred to the material through convection and radiation. The heating elements warm the chamber walls, which then radiate heat to the sample inside.
- Temperature Control: A PID controller, in conjunction with a thermocouple, regulates the temperature by adjusting the power supplied to the heating elements. This ensures precise and uniform heating.
- Energy Efficiency: The furnace's design minimizes heat loss, making it energy-efficient and capable of rapid heating, cooling, and recovery.
4. Applications
- Industrial Processes: Muffle furnaces are used for smelting, casting, and heat-treating metals, as well as for fusing glass and brazing.
- Laboratory Experiments: They are essential for high-temperature chemical reactions, such as creating oxides, reducing metals, and conducting CVD processes.
- Ashing Samples: In analytical chemistry, muffle furnaces are used to combust samples at high temperatures, turning them into ash for analysis.
5. Advantages
- Contamination-Free Heating: By separating the material from combustion byproducts, the furnace ensures that the heating process is free from contamination.
- Precise Temperature Control: Advanced control systems allow for precise temperature regulation, which is crucial for sensitive experiments and industrial processes.
- Durability and Efficiency: The robust construction and insulation make the furnace durable and energy-efficient, capable of withstanding extreme conditions.
6. Key Components
- Heating Chamber: The core component where the material is placed and heated.
- Insulation Box: Surrounds the heating chamber to prevent heat loss.
- Electric Control System: Includes heating elements, PID controllers, and thermocouples for temperature regulation.
- Refractory Materials: Used in the construction of the chamber and insulation to withstand high temperatures and minimize heat loss.
7. Operational Considerations
- Material Selection: The choice of materials for the chamber and insulation is critical for ensuring durability and efficiency.
- Maintenance: Regular maintenance of heating elements and insulation is necessary to maintain optimal performance.
- Safety: Proper safety measures, such as temperature monitoring and ventilation, are essential to prevent accidents and ensure safe operation.
In summary, the muffle furnace is a versatile and essential tool for high-temperature applications, offering precise control, contamination-free heating, and energy efficiency. Its design and working principles make it suitable for a wide range of industrial and laboratory processes, ensuring reliable and consistent performance.
Summary Table:
Aspect | Details |
---|---|
Purpose | Provides a controlled, isolated environment for high-temperature heating. |
Temperature Range | Up to 1400°C, suitable for processes like glass fusing and metal brazing. |
Design Features | Ceramic/refractory lining, heating elements, insulation box for efficiency. |
Applications | Industrial (smelting, casting) and lab (chemical reactions, ashing). |
Advantages | Contamination-free heating, precise temperature control, energy efficiency. |
Key Components | Heating chamber, insulation box, PID controllers, thermocouples. |
Need a muffle furnace for your high-temperature applications? Contact us today for expert guidance!