The pressure required for isostatic pressing, particularly in cold isostatic pressing (CIP), varies significantly depending on the material, application, and desired outcomes. Generally, the pressure ranges from less than 5,000 psi (34.5 MPa) to over 100,000 psi (690 MPa). For ceramics, the typical forming pressures range from 21 to 210 MPa (3,000 to 30,000 psi), while most industrial applications use an average pressure of 200–250 MPa for the CIP cycle. Warm isostatic pressing operates at higher pressures, around 300 MPa. The specific pressure used depends on factors such as material properties, vessel size, and the level of automation in the cold isostatic pressing machine.
Key Points Explained:
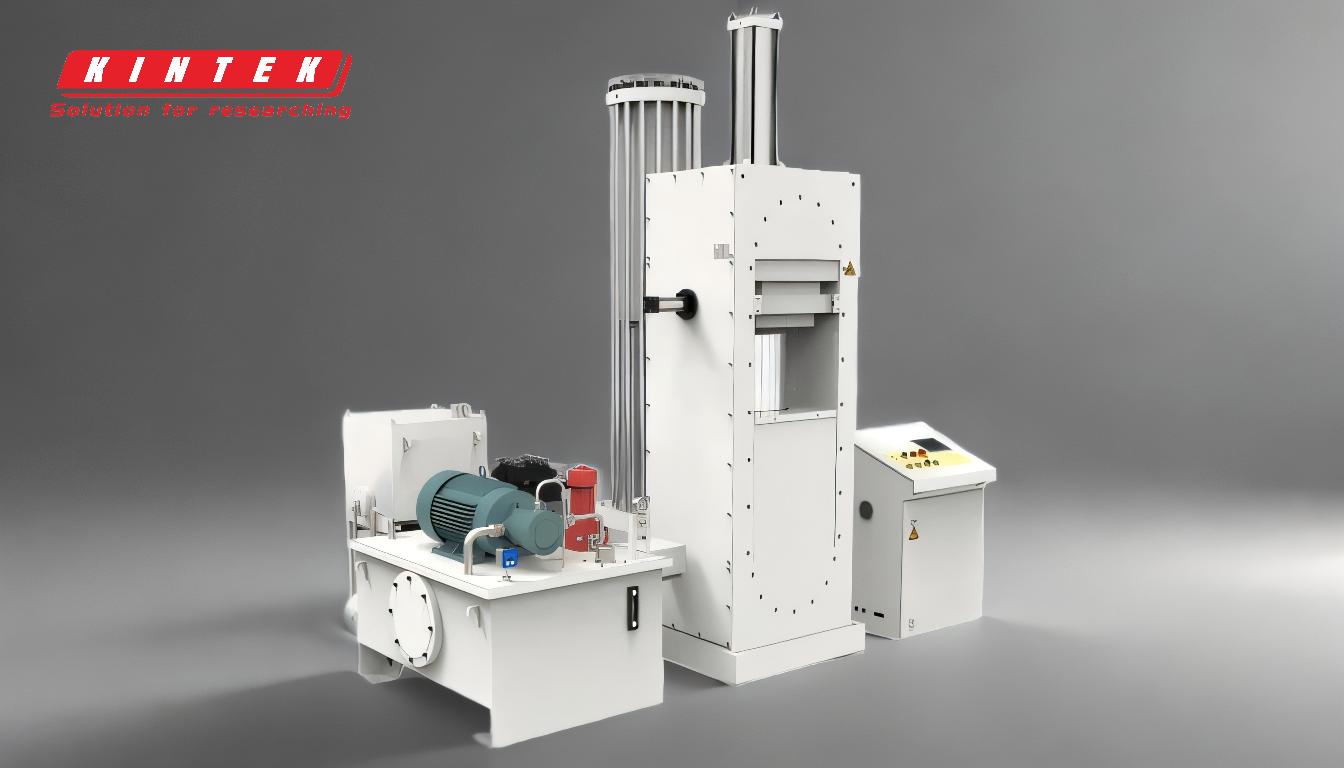
-
Pressure Range in Cold Isostatic Pressing (CIP):
- The pressure in CIP typically ranges from 1,035 to 4,138 bar (15,000 to 60,000 psi) or 34.5 to 690 MPa.
- This wide range accommodates different materials and applications, from low-density powders to high-performance ceramics and metals.
- Lower pressures (e.g., 5,000 psi or 34.5 MPa) are used for softer materials, while higher pressures (e.g., 100,000 psi or 690 MPa) are required for denser or more complex shapes.
-
Typical Pressures for Ceramics:
- For ceramic materials, the forming pressures in isostatic pressing usually range from 21 to 210 MPa (3,000 to 30,000 psi).
- This range ensures uniform compaction and high green density, which are critical for achieving the desired mechanical properties in the final product.
-
Average Pressure in Industrial CIP Cycles:
- Most industrial applications use an average pressure of 200–250 MPa during the CIP cycle.
- This pressure range is optimal for achieving consistent compaction and high-density parts without causing material degradation.
-
Warm Isostatic Pressing (WIP) Pressures:
- Warm isostatic pressing operates at higher pressures, typically around 300 MPa.
- WIP combines elevated temperatures with high pressure to enhance material consolidation, making it suitable for advanced materials and complex geometries.
-
Factors Influencing Pressure Selection:
- Material Properties: Harder or denser materials require higher pressures for effective compaction.
- Application Requirements: Intricate shapes or high-density parts may necessitate higher pressures.
- Equipment Capabilities: The size of the pressure vessel and pump capacity determine the maximum achievable pressure.
-
Production Rates and Automation:
- Production rates in isostatic pressing depend on factors such as applied pressure, vessel size, and automation levels.
- Modern cold isostatic pressing machines can achieve one operation cycle per minute or faster, making them highly efficient for large-scale production.
By understanding these key points, equipment and consumable purchasers can make informed decisions about the appropriate pressure settings and machinery for their specific needs, ensuring optimal results in material compaction and shaping.
Summary Table:
Type of Pressing | Pressure Range | Applications |
---|---|---|
Cold Isostatic Pressing (CIP) | 1,035–4,138 bar (15,000–60,000 psi) or 34.5–690 MPa | Soft materials to high-performance ceramics and metals |
Ceramics (CIP) | 21–210 MPa (3,000–30,000 psi) | Uniform compaction and high green density for ceramics |
Industrial CIP Cycles | 200–250 MPa | Consistent compaction and high-density parts without material degradation |
Warm Isostatic Pressing (WIP) | ~300 MPa | Advanced materials and complex geometries with enhanced consolidation |
Need help selecting the right pressure for your isostatic pressing? Contact our experts today for tailored solutions!