The pressure of a pellet machine, particularly an xrf pellet press, typically ranges between 15 and 35 tons. This pressure is essential for creating high-quality pellets suitable for XRF analysis. The process involves grinding the sample to a fine particle size, mixing it with a binder, and pressing it in a die to form a pellet. Smaller particle sizes, ideally less than 50µm, ensure better binding and more accurate analytical results. This pressure range ensures the sample is compacted sufficiently to produce a durable and homogeneous pellet.
Key Points Explained:
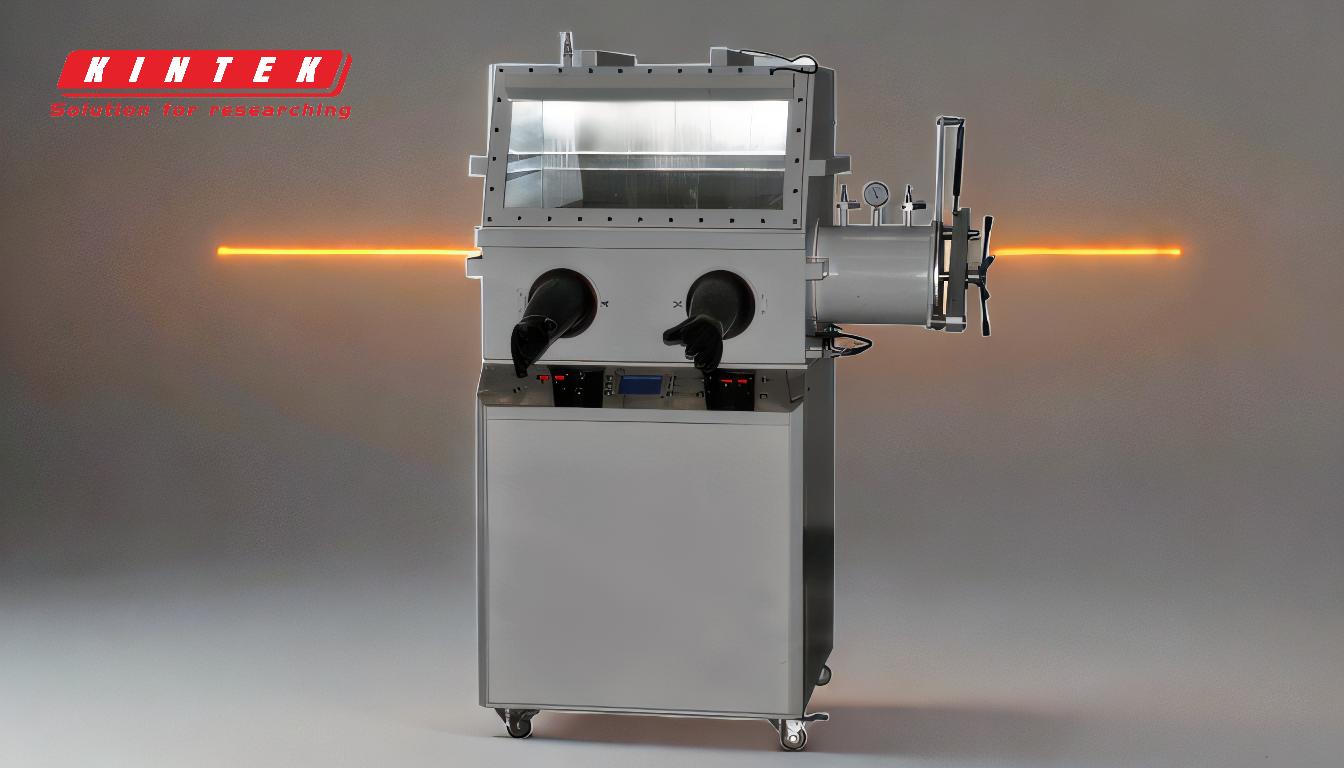
-
Pressure Range for XRF Pellet Pressing:
- The standard pressure range for an xrf pellet press is between 15 and 35 tons. This range is critical for ensuring the sample is compressed adequately to form a solid pellet. Lower pressures may result in weak or crumbly pellets, while excessive pressure can cause cracking or damage to the die.
-
Importance of Particle Size:
- Samples should be ground to a particle size of less than 50µm, though sizes up to 75µm are acceptable. Smaller particles ensure better binding under pressure, leading to a more homogeneous pellet. This homogeneity is crucial for accurate XRF analysis, as it minimizes variability in the sample.
-
Role of Binders:
- Binders or grinding aids are often mixed with the sample to improve pellet formation. These additives help the particles adhere together under pressure, enhancing the structural integrity of the pellet. The choice of binder depends on the sample type and the specific requirements of the analysis.
-
Steps in the Pellet Pressing Process:
- Grinding: The sample is ground to a fine powder to achieve the desired particle size.
- Mixing: The powdered sample is mixed with a binder to ensure uniform distribution.
- Pressing: The mixture is poured into a pressing die and compressed at the specified pressure (15-35 tons).
- Final Product: The resulting pellet is a compact, durable tablet ready for XRF analysis.
-
Impact of Pressure on Pellet Quality:
- The applied pressure directly affects the density and durability of the pellet. Optimal pressure ensures the pellet is dense enough to withstand handling and analysis while maintaining uniformity. Too little pressure can lead to weak pellets, while too much pressure may cause deformation or damage.
-
Applications of XRF Pellet Pressing:
- XRF pellet presses are widely used in industries such as mining, metallurgy, and environmental testing. They are essential for preparing samples for elemental analysis, ensuring consistent and reliable results.
By understanding the pressure requirements and the factors influencing pellet quality, users can optimize their xrf pellet press operations for accurate and efficient XRF analysis.
Summary Table:
Key Factor | Details |
---|---|
Pressure Range | 15-35 tons |
Particle Size | Less than 50µm (up to 75µm acceptable) |
Binders | Improve pellet formation and structural integrity |
Process Steps | Grinding → Mixing → Pressing → Final Pellet |
Applications | Mining, metallurgy, environmental testing |
Optimize your XRF pellet pressing process—contact our experts today for tailored solutions!