The graphite furnace operates on the principle of utilizing graphite's excellent thermal and electrical conductivity, as well as its high-temperature resistance, to create a controlled high-temperature environment. The furnace typically consists of a graphite tube or resistor, which is heated either directly or indirectly to achieve temperatures exceeding 2500°C. This is done in an inert atmosphere (such as argon or nitrogen) or a vacuum to prevent oxidation of the materials being processed. The furnace is used for applications like graphitization, heat treatment, sintering, and high-temperature material testing. Temperature control is achieved using thermocouples or pyrometers, ensuring precise heating for various industrial and research purposes.
Key Points Explained:
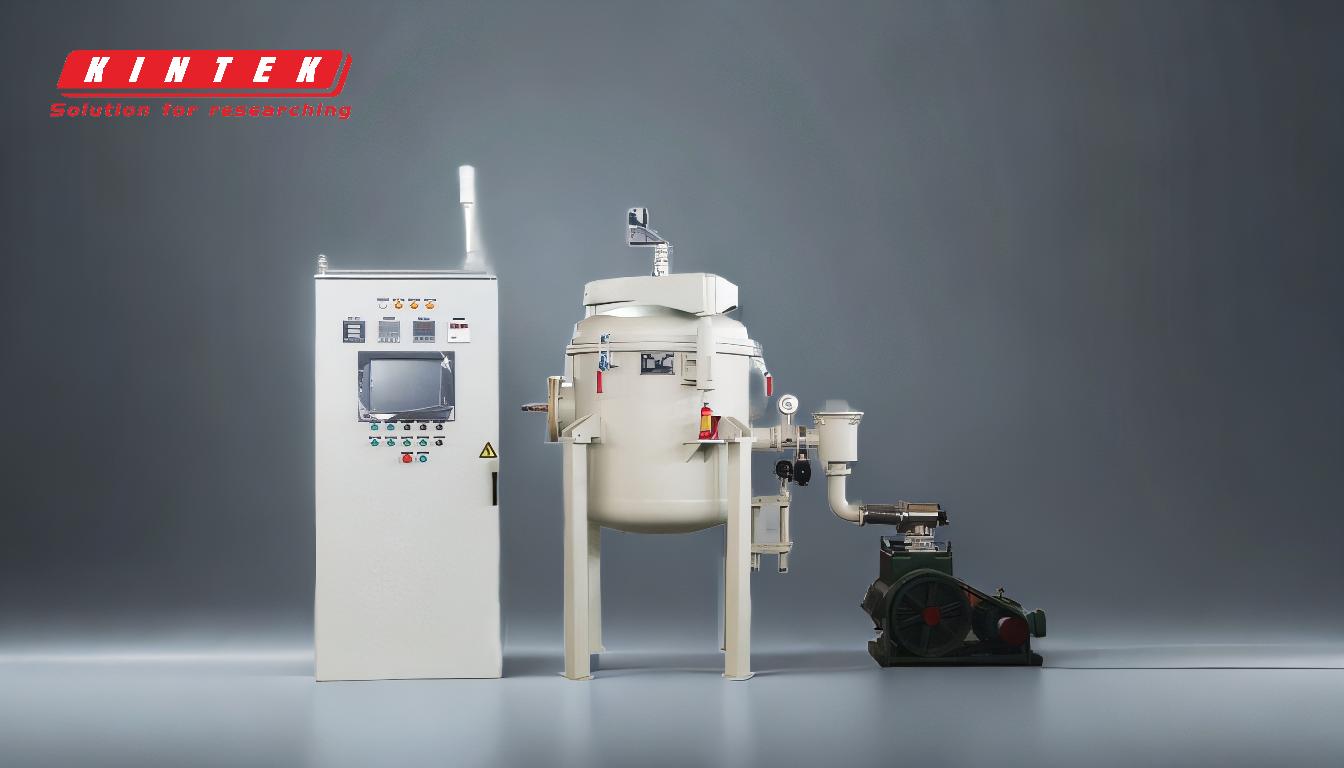
-
Graphite as the Core Material:
- Graphite is chosen for its unique properties, including high thermal conductivity, electrical conductivity, and resistance to extreme temperatures. These properties make it ideal for creating a stable and efficient high-temperature environment.
- The furnace typically uses graphite tubes or resistors as the heating elements, which can withstand temperatures above 2500°C without significant degradation.
-
Heating Mechanism:
- In a graphite resistance furnace, the graphite resistor is heated by passing an electric current through it. The electrical resistance of the graphite generates heat, which is then transferred to the sample or workpiece placed inside the furnace.
- In a graphite tube furnace, the graphite tube itself is heated, either by direct electrical resistance heating or by an external heat source, to create a uniform high-temperature environment.
-
Controlled Atmosphere:
- Graphite furnaces operate in an inert atmosphere (e.g., argon or nitrogen) or a vacuum to prevent oxidation of the materials being processed. This is critical for maintaining the integrity of carbonaceous materials and other sensitive substances at high temperatures.
- The controlled atmosphere also ensures that the graphite components do not oxidize, which would otherwise degrade their performance.
-
Temperature Measurement and Control:
- Temperature is monitored using thermocouples or pyrometers, which provide accurate readings even at extremely high temperatures.
- Precise temperature control is essential for applications like graphitization, sintering, and heat treatment, where specific temperature profiles are required to achieve desired material properties.
-
Applications of Graphite Furnaces:
- Graphitization: Heating carbonaceous materials to convert them into graphite.
- Heat Treatment: Modifying the properties of materials through controlled heating and cooling.
- Sintering: Fusing powdered materials into a solid mass using heat.
- High-Temperature Material Testing: Investigating the behavior of materials under extreme conditions.
- Melting and Alloying: Processing metals and alloys at high temperatures.
- Research and Development: Studying reaction kinetics, solid electrolytes, and other high-temperature phenomena.
-
Advantages of Graphite Furnaces:
- High Efficiency: Graphite's thermal conductivity ensures rapid and uniform heating.
- Durability: Graphite components can withstand repeated heating cycles without significant wear.
- Versatility: Suitable for a wide range of applications, from industrial processing to advanced research.
-
Types of Graphite Furnaces:
- Graphite Tube Furnace: Uses a graphite tube as the heating element, ideal for uniform heating of samples.
- Graphite Resistance Furnace: Relies on a graphite resistor to generate heat, commonly used for graphitization and sintering.
- Vacuum Graphite Furnace: Operates in a vacuum or protective atmosphere, suitable for high-purity applications.
By combining these principles, graphite furnaces provide a reliable and efficient solution for high-temperature processing across various industries and research fields.
Summary Table:
Key Aspect | Details |
---|---|
Core Material | Graphite (high thermal/electrical conductivity, extreme temperature resistance) |
Heating Mechanism | Direct/indirect heating via graphite tubes or resistors, exceeding 2500°C |
Controlled Atmosphere | Inert gases (argon/nitrogen) or vacuum to prevent oxidation |
Temperature Control | Thermocouples or pyrometers for precise monitoring and control |
Applications | Graphitization, heat treatment, sintering, material testing, R&D |
Advantages | High efficiency, durability, versatility |
Types | Graphite tube, graphite resistance, vacuum graphite furnaces |
Ready to enhance your high-temperature processes? Contact our experts today to find the perfect graphite furnace solution!