Physical Vapor Deposition (PVD) coating is a sophisticated process used to apply thin, durable, and functional layers onto the surfaces of various materials. The process involves vaporizing a solid material in a vacuum environment and then depositing the vaporized atoms onto the substrate. This results in a thin, bonded layer that enhances the substrate's appearance, durability, and functionality. The PVD coating process is highly controlled, involving precise temperature and pressure conditions, and is widely used in industries requiring high-performance coatings, such as aerospace, automotive, and medical devices.
Key Points Explained:
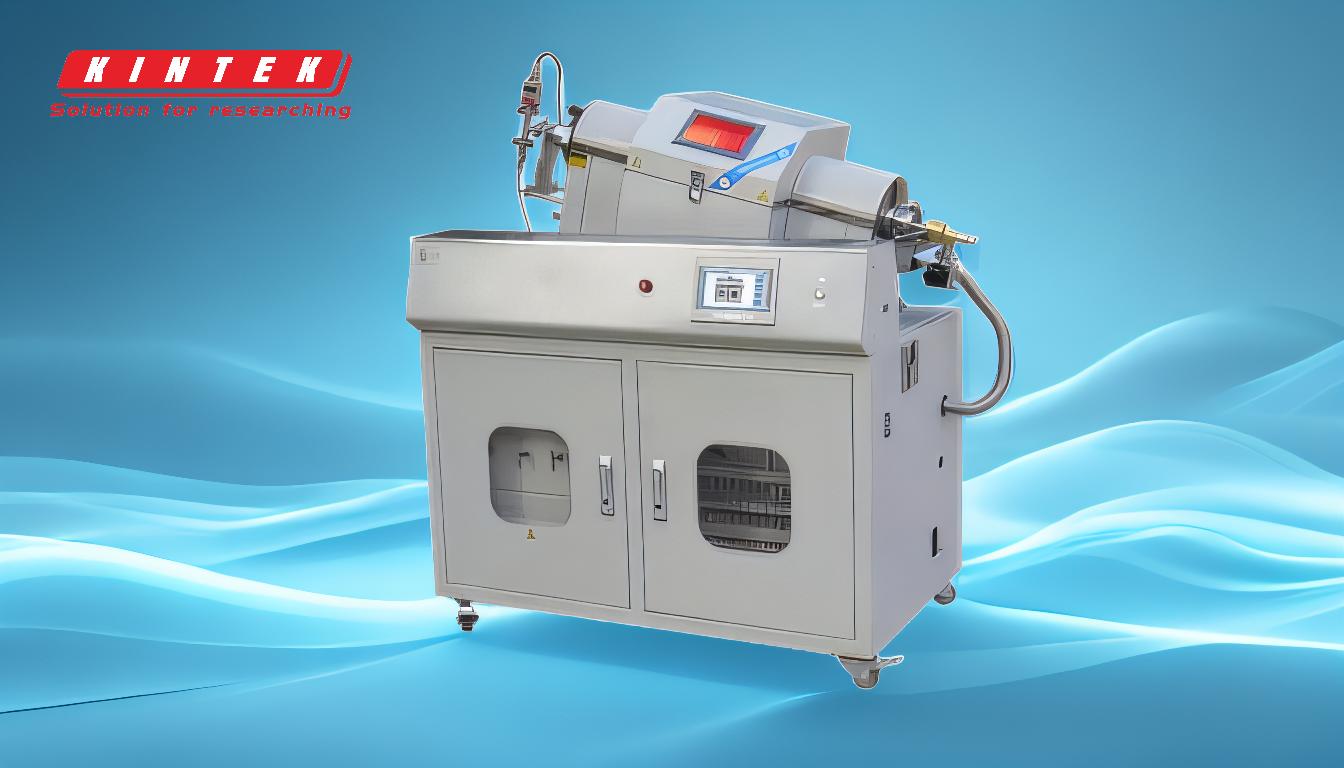
-
Basic Principle of PVD Coating:
- Vaporization of Solid Material: The core principle of PVD coating involves the vaporization of a solid material (often metals like titanium, zirconium, or chromium) in a vacuum environment. This is achieved through various methods such as sputtering, electron beam evaporation, or cathodic arc discharge.
- Deposition onto Substrate: The vaporized atoms travel through the vacuum and deposit onto the surface of the substrate. This deposition occurs atom by atom, forming a thin, uniform layer that bonds strongly with the substrate.
-
Vacuum Environment:
- High-Vacuum Conditions: The process takes place in a vacuum chamber, where the pressure is significantly reduced to create a high-vacuum environment. This ensures that the vaporized material remains clean and uncontaminated, leading to a high-quality coating.
- Controlled Atmosphere: The vacuum environment also allows for the introduction of reactive gases (e.g., nitrogen) to modify the composition of the coating. For example, adding nitrogen can result in the formation of metal nitrides, which enhance the coating's properties.
-
Methods of Vaporization:
- Sputtering: In this method, high-energy ions bombard the target material, causing atoms to be ejected from the surface and subsequently deposited onto the substrate.
- Electron Beam Evaporation: An electron beam is used to heat the target material, causing it to vaporize. The vaporized atoms then condense on the substrate.
- Cathodic Arc Discharge: An electric arc is used to vaporize the target material, producing a high-density plasma of ionized metal atoms that deposit onto the substrate.
-
Steps in the PVD Coating Process:
- Preparation: The substrate is cleaned and placed in the vacuum chamber. The target material is also positioned within the chamber.
- Evacuation: The chamber is evacuated to create a high-vacuum environment, typically reaching pressures in the range of 10^-3 to 10^-6 Pa.
- Vaporization: The target material is vaporized using one of the methods mentioned above (sputtering, electron beam evaporation, or cathodic arc discharge).
- Transport: The vaporized atoms travel through the vacuum and are transported to the substrate.
- Deposition: The atoms condense on the substrate, forming a thin, uniform layer. The substrate may be rotated or moved to ensure even coating.
- Purging: After deposition, the chamber is purged with inert gas to remove any residual vapors and prepare for the next cycle.
-
Advantages of PVD Coating:
- Durability: PVD coatings are highly durable, offering excellent resistance to wear, corrosion, and high temperatures.
- Thin and Uniform: The coatings are extremely thin (typically in the nanometer to micrometer range) and uniform, ensuring consistent performance.
- Eco-Friendly: PVD coating is considered more environmentally friendly compared to other coating methods like Chemical Vapor Deposition (CVD), as it produces fewer harmful by-products.
- Versatility: PVD coatings can be applied to a wide range of materials, including metals, ceramics, and polymers, making them suitable for various applications.
-
Applications of PVD Coating:
- Aerospace: PVD coatings are used to enhance the performance and longevity of aerospace components, such as turbine blades and engine parts.
- Automotive: In the automotive industry, PVD coatings are applied to improve the wear resistance and aesthetic appeal of components like engine parts, wheels, and trim.
- Medical Devices: PVD coatings are used on medical implants and surgical instruments to improve biocompatibility and reduce wear.
- Consumer Electronics: PVD coatings are applied to smartphone cases, watches, and other electronic devices to enhance durability and provide a premium finish.
In summary, PVD coating is a highly controlled and versatile process that involves vaporizing a solid material in a vacuum and depositing it onto a substrate to form a thin, durable, and functional layer. The process offers numerous advantages, including durability, uniformity, and environmental friendliness, making it suitable for a wide range of industrial applications.
Summary Table:
Aspect | Details |
---|---|
Basic Principle | Vaporization of solid material in a vacuum and deposition onto a substrate. |
Vacuum Environment | High-vacuum conditions ensure clean, uncontaminated coatings. |
Vaporization Methods | Sputtering, electron beam evaporation, cathodic arc discharge. |
Process Steps | Preparation, evacuation, vaporization, transport, deposition, purging. |
Advantages | Durability, thin and uniform layers, eco-friendly, versatile applications. |
Applications | Aerospace, automotive, medical devices, consumer electronics. |
Discover how PVD coating can elevate your products—contact our experts today!