Vacuum arc melting (VAR) is a specialized metallurgical process used to refine and purify metals, particularly reactive alloys like titanium, zirconium, steels, and superalloys. The process involves melting a consumable electrode under a high-temperature electric arc in a vacuum environment. The molten metal drips into a water-cooled copper mold, where it solidifies into a high-purity ingot. This method ensures the removal of impurities, improves the metal's crystal structure, and enhances its mechanical properties. The key to the process lies in maintaining vacuum conditions, controlling the arc temperature, and managing the solidification rate to achieve a refined and homogeneous material.
Key Points Explained:
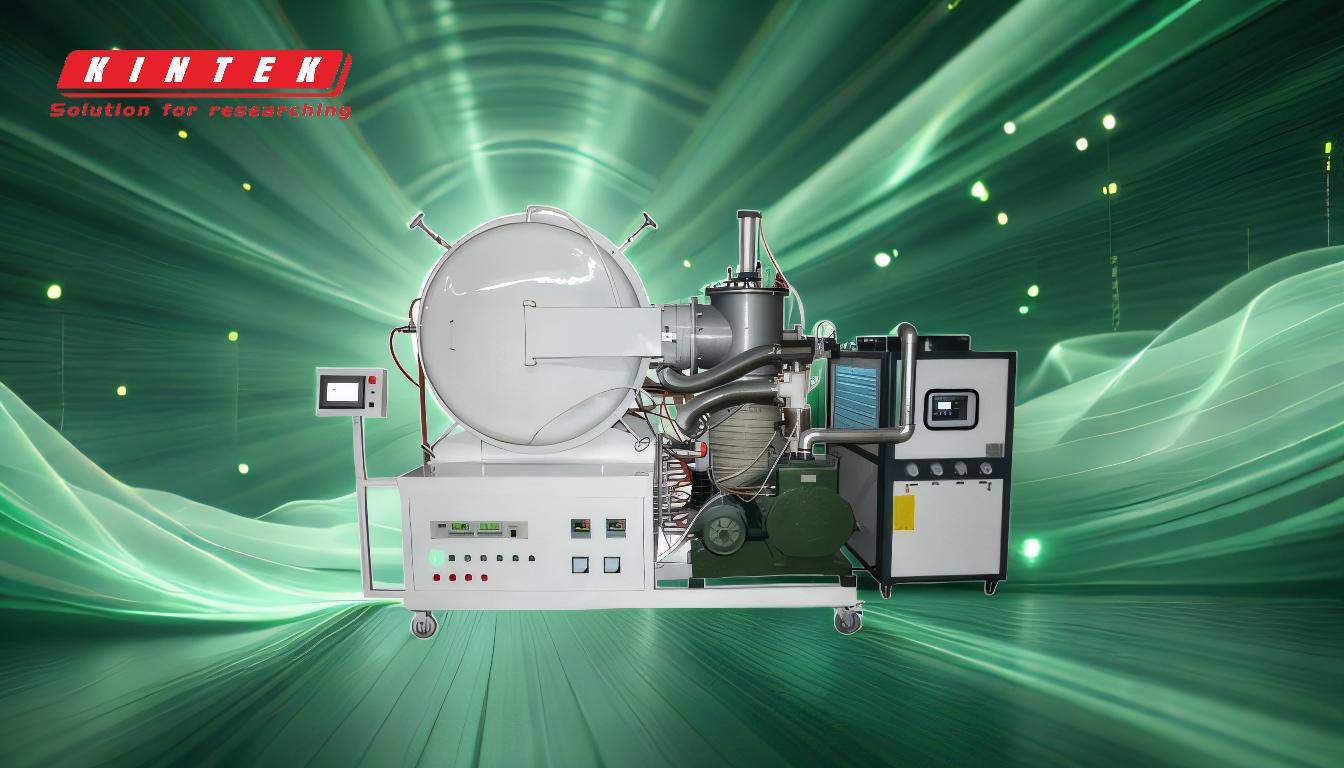
-
Principle of Vacuum Arc Melting:
- The process relies on an electric arc generated under vacuum conditions to melt a consumable electrode. The arc is struck between the electrode and a baseplate in a water-cooled copper mold.
- The intense heat of the arc (up to 5000K) melts the tip of the electrode, forming droplets that fall into the molten pool below.
- The vacuum environment prevents contamination from atmospheric gases and allows for the removal of volatile impurities like hydrogen and sulfur.
-
Role of Vacuum Environment:
- The vacuum ensures a slag-free and contamination-free melting process, which is critical for reactive metals like titanium and zirconium.
- It facilitates the removal of dissolved gases (e.g., hydrogen, oxygen) and volatile impurities, improving the purity and mechanical properties of the final product.
-
Arc Zone and Temperature Control:
- The electric arc generates extremely high temperatures, enabling rapid melting of the electrode.
- The molten metal droplets pass through the arc zone, where physical and chemical reactions occur, refining the metal and enhancing its microstructure.
-
Solidification and Crystallization:
- The molten metal solidifies in a water-cooled copper mold, which controls the cooling rate and promotes a uniform crystal structure.
- Controlled solidification minimizes defects like segregation and porosity, resulting in a high-quality ingot.
-
Purification and Refinement:
- The process refines the metal by removing impurities and improving its chemical composition.
- The absence of casting refractories and the vacuum environment ensure that the final product is ultraclean and free from inclusions.
-
Applications of VAR:
- VAR is widely used for producing high-performance alloys, including titanium, zirconium, steels, and superalloys.
- It is particularly beneficial for aerospace, medical, and industrial applications where material purity and performance are critical.
-
Advantages of VAR:
- High energy concentration and precise control over the melting and solidification processes.
- Improved material properties, including enhanced strength, ductility, and fatigue resistance.
- Ability to process reactive and refractory metals that are difficult to refine using conventional methods.
By combining the principles of vacuum technology, electric arc heating, and controlled solidification, vacuum arc melting achieves a high degree of material refinement and consistency, making it indispensable for advanced metallurgical applications.
Summary Table:
Key Aspect | Details |
---|---|
Principle | Electric arc melts consumable electrode under vacuum. |
Vacuum Role | Prevents contamination, removes gases and impurities. |
Temperature Control | Arc heats up to 5000K, refining metal microstructure. |
Solidification | Water-cooled copper mold ensures uniform crystal structure. |
Applications | Aerospace, medical, and industrial high-performance alloys. |
Advantages | Enhanced strength, ductility, and fatigue resistance. |
Discover how vacuum arc melting can transform your metal refining process—contact us today!